Last Updated on March 12, 2025
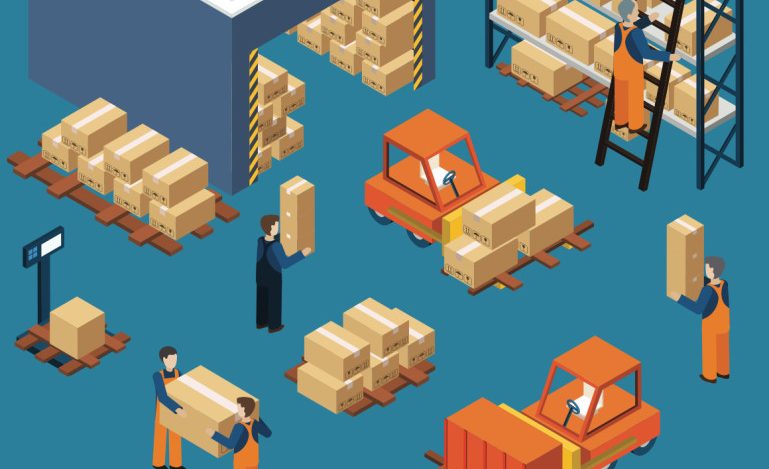
Keeping track of inventory in manufacturing isn't just about counting boxes—it's about ensuring efficiency, reducing waste, and keeping production running smoothly. Manufacturing inventory management plays a crucial role in the success of any operation, especially for companies relocating or starting in Mexico, where supply chain dynamics and logistics require extra attention. This is where nearshore manufacturing partners like NovaLink can help. In this blog post, we will explore what manufacturing inventory management is, why it is essential for manufacturing operations, and how partnering with NovaLink can help small and medium-sized businesses optimize their inventory management processes and reduce costs.
What is Manufacturing Inventory Management?
Manufacturing inventory management is the process of effectively tracking, controlling, and optimizing a manufacturer's inventory levels. It involves developing and implementing a system for tracking inventory, determining optimal levels of inventory, managing inventory replenishment, and minimizing inventory costs. Manufacturing inventory management is essential for manufacturing operations as it helps to ensure that businesses have the right materials and products on hand when they need them, while also preventing overstocking and reducing waste.
Inventory management is an overarching term that refers to your tracking system for every phase in the product life cycle. It can include your sales forecasting, product ordering, supply chain management, warehouse management, and customer fulfillment solutions.
Business.org
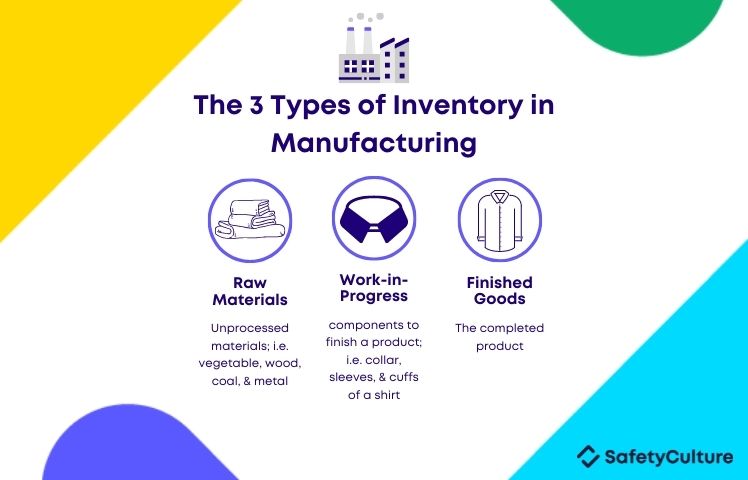
Source: Safety Culture
Why is Manufacturing Inventory Management Important?
Effective manufacturing inventory management requires careful planning and analysis. Manufacturers must understand the demand for their products and accurately forecast future demand, so they can order the right amount of raw materials and finished products. This requires a deep understanding of the manufacturing process and supply chain management. Manufacturers must also have the right tools and technology in place to track inventory levels, monitor production schedules, and manage replenishment.
The Core Components of Manufacturing Inventory Management
To manage inventory effectively, you need to understand its three main categories:
- Raw Materials: These are the building blocks of your products. Whether it’s textiles, metals, or electronics, keeping an optimal supply ensures steady production.
- Work-in-Progress (WIP): These are products that are partially completed. Managing WIP efficiently prevents bottlenecks and keeps production flowing.
- Finished Goods: These are ready for shipment. Efficient tracking prevents overproduction and ensures you meet customer demand on time.
Each category requires a different approach to tracking, forecasting, and replenishment.
Why Inventory Management Can Make or Break Your Manufacturing Operation
Imagine running a production line and suddenly realizing you're out of a critical component. Or worse—your warehouse is overflowing with raw materials you won’t need for months. These scenarios highlight why a well-structured inventory system is essential.
In manufacturing, inventory isn't just stock on shelves. It’s a delicate balance between raw materials, work-in-progress (WIP), and finished goods. Too little, and you risk production delays. Too much, and you tie up valuable capital in unused stock.
A common error is the belief that if I buy a thousand pieces of X components that it will translate into a thousand finished products. However, that's not the case in most scenarios: there will be some waste that may be incurred by your suppliers or vendors, and some by process of execution which might be material related or even manpower related. Once we start touching the material for producing the product, new material needs to be applied in order to satisfy or guarantee a good quality product at the end of the line. - Manuel Campos, Engineering and Information Systems Manager at NovaLink
Common Inventory Management Challenges in Manufacturing
Running a manufacturing plant—especially in a nearshore location like Mexico—comes with unique challenges. Some common issues include:
- Supply Chain Disruptions: Delays in raw materials can stall production. Establishing strong supplier relationships and maintaining safety stock can help mitigate risks.
- Overstocking & Understocking: Buying too much ties up capital, while too little leads to production stoppages. Forecasting demand accurately is crucial.
- Tracking Errors: Relying on outdated systems or manual tracking increases the risk of mistakes. Modern inventory management software can streamline this process.
Best Strategies for Effective Manufacturing Inventory Management
So how do you stay on top of your inventory without letting it overwhelm your operation? Here are a few key strategies:
1. Implement a Reliable Inventory Management System
Spreadsheets won’t cut it when you’re managing a complex supply chain. Investing in an ERP (Enterprise Resource Planning) system or inventory management software helps automate tracking, forecasting, and order management.
2. Use Just-in-Time (JIT) Inventory Practices
JIT minimizes excess inventory by ordering raw materials only as needed. This approach reduces storage costs and waste but requires precise coordination with suppliers.
3. Adopt Barcode & RFID Tracking
Using barcode or RFID technology speeds up inventory checks, reduces human error, and provides real-time stock visibility. This is especially useful for large-scale manufacturing operations.
4. Conduct Regular Audits
Cycle counts and full inventory audits help catch discrepancies before they become major issues. Regular checks ensure that what’s recorded matches what’s actually in stock.
5. Strengthen Supplier & Logistics Partnerships
If your manufacturing plant is in Mexico, reliable suppliers and logistics partners are essential. Ensuring clear communication and having backup suppliers can prevent unexpected disruptions.
6. Set an Inventory Ratio
The inventory turnover ratio refers to the number of times a business replaces its inventory during the course of a year. The key to knowing what you have on hand (or do not have) and how much you will need to purchase to maintain viability in your production lines is having accurate and current data available. For many manufacturing industries, the definition and quality of data pose substantial challenges, often due to a lack of sound data management practices. When procurement and manufacturing lead times are inaccurate, a company is forced to rely on judgment-based inventory planning. As a result of this type of inaccurate planning, excessive orders and stock levels may be required to meet customer service requirements.
This can be avoided if manufacturers have sound data that will allow them to establish an inventory ratio that prevents overstocking and shortages in the manufacturing process.
The inventory ratio for manufacturing typically ranges from 1 to 2 on a national scale. According to the Census Bureau, the inventory ratio in all manufacturing sectors ranged from 1.21 to 1.39 from 2000 to 2010. The turnover ratio in the durable goods sector ranged from 1.40 to 1.82, while the ratios were lower in the nondurable goods sector at 0.91 to 1.14. Therefore, manufacturers should expect to maintain ratios in these general ranges.
Chron Small Business
Why Manufacturing Inventory Management Matters More in Mexico
Relocating or starting a manufacturing operation in Mexico comes with great advantages—lower labor costs, proximity to U.S. markets, and favorable trade agreements. However, effective inventory management is crucial to fully benefit from these advantages. Supply chain logistics, import/export regulations, and infrastructure must be carefully planned to avoid costly delays and inefficiencies.
Conclusion: Manufacturing Inventory Management Is a Critical Process for Manufacturing Operations
Effective manufacturing inventory management is crucial for any business, as it involves accurately tracking and forecasting inventory levels to ensure that materials and products are available when needed. Satisfactory inventory management not only refers to what is currently available, but also to predicting when more materials will be needed to keep the production line running. Poor tracking of inventory levels can lead to disruptions in the production process, potentially bringing the entire operation to a halt.
Partnering with a nearshore manufacturing partner like NovaLink can help SMBs to focus on their core competencies and business priorities. By outsourcing manufacturing to a trusted partner, SMBs can free up resources and reduce the time and effort required to manage inventory and production schedules. This allows SMBs to focus on areas of their business where they can add the most value and achieve the greatest competitive advantage.
FAQs about Inventory Management: Best Practices and Strategies
Q1: Why is effective inventory management important for businesses?
A1: Effective inventory management is crucial for businesses as it helps optimize cash flow, reduce carrying costs, minimize stockouts, and improve customer satisfaction. It enables businesses to have the right amount of inventory at the right time, ensuring smooth operations, cost control, and efficient order fulfillment.
Q2: What are some best practices for inventory management?
A2: Some best practices for inventory management include implementing accurate demand forecasting, adopting inventory tracking systems, setting optimal inventory levels, implementing just-in-time (JIT) or lean inventory principles, conducting regular inventory audits, and establishing effective supplier relationships. These practices help businesses maintain optimal inventory levels and minimize excess or obsolete stock.
Q3: How can businesses optimize inventory turnover?
A3: Businesses can optimize inventory turnover by implementing strategies such as demand forecasting, improving supply chain visibility, reducing lead times, optimizing order quantities, implementing efficient inventory replenishment processes, and analyzing sales and demand patterns. By improving inventory turnover, businesses can reduce holding costs and increase profitability.
Q4: What role does technology play in inventory management?
A4: Technology plays a significant role in inventory management by providing advanced tools and software solutions. Inventory management systems, barcode scanning, automation, and data analytics help streamline inventory tracking, order processing, and demand forecasting. Technology enables businesses to make data-driven decisions, improve accuracy, and enhance overall inventory management efficiency.
Q5: How can businesses reduce the risk of stockouts while managing inventory levels?
A5: Businesses can reduce the risk of stockouts by implementing strategies such as safety stock management, setting reorder points, maintaining reliable supplier relationships, monitoring lead times, and establishing effective communication channels with suppliers. Regularly reviewing and adjusting inventory levels based on demand fluctuations and market trends can help ensure adequate stock availability.
About NovaLink
As a manufacturer in Mexico, NovaLink employs a unique approach that transcends the traditional model of shelter production. More than just the location of your manufacturing, we would like to become a partner in your manufacturing in Mexico. You will be able to relocate or initiate manufacturing for your company in Mexico in a low-cost labor environment with very little delay or up-front costs. Find out how we can help you by handling the manufacturing process.
There are NovaLink facilities in the border cities of Brownsville, Texas, Matamoros, Mexico, and Saltillo, Mexico.