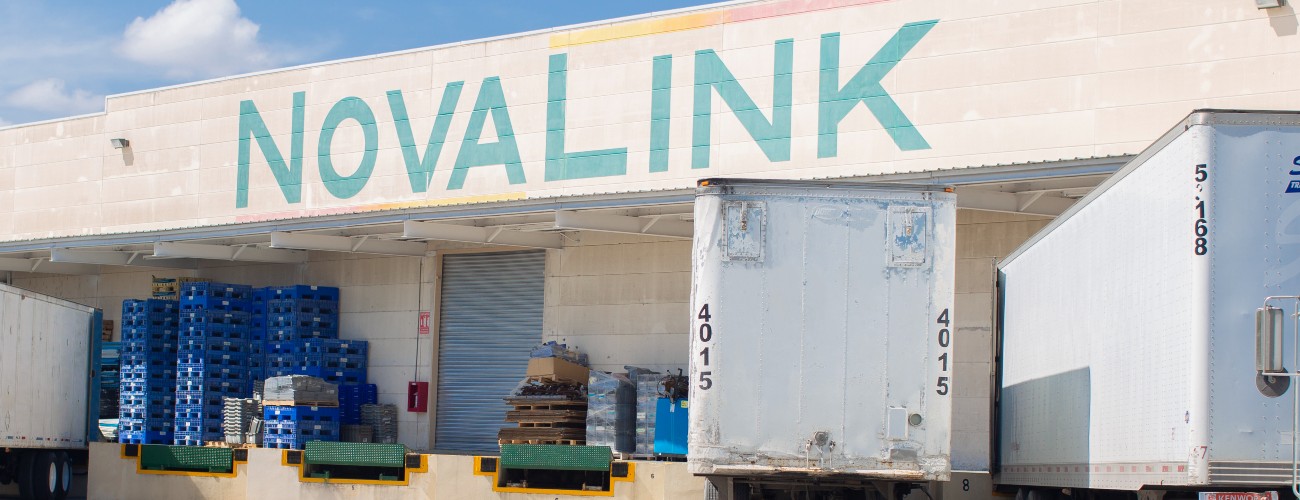
Mexico Supply Chain Services
NovaLink thinks that producing goods in Mexico using Mexico's supply chain services should be a simple, speedy, and economical process.
Optimizing Operations: Managing Mexico Supply Chain Services with NovaLink
When it comes to the movement of equipment, raw materials, and finished goods across the U.S./Mexico border, NovaLink's Mexico Supply Chain Services are equipped to handle the task. NovaLink's services can help avoid expensive mistakes during export.
When looking for ways to streamline your supply chain, the decision between manufacturing in Mexico versus China is a no-brainer. NovaLink's Mexico Supply Chain Services make it simple, and here are some of the Nearshore Manufacturing Services they offer:
- Sourcing and Procurement
- Inventory/Warehouse Management
- Finished Product Distribution
- Transportation
- Customs Brokerage
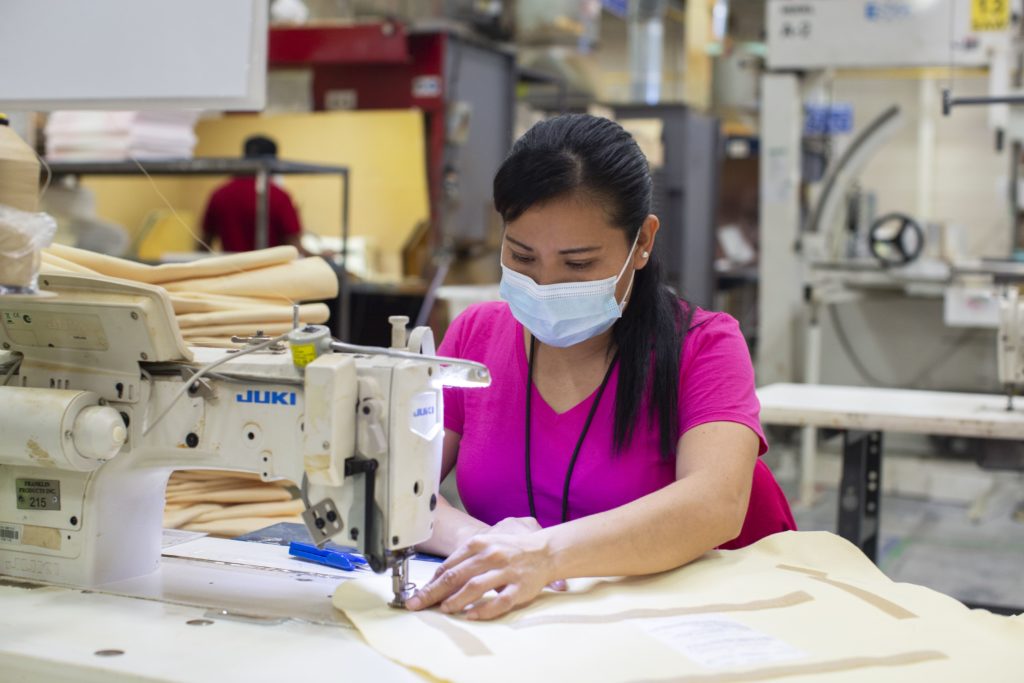
NovaLink Manufacturing Facility Video
NovaLink has released a new video highlighting the versatility of their manufacturing facility in Matamoros, Mexico. In this video, you will be able to see the factory and its associates in action. The video, which was filmed on the floor of the manufacturing facility, illustrates the variety of manufacturing operations and the wide range of skills represented by the workforce. As well as demonstrating NovaLink's commitment to first class manufacturing, the video also emphasizes its commitment to safety protocols for the health of its workers and clients.
Are Your Manufacturing Investments Suffering from Supply Chain Volatility?
Supply chain volatility has been a major issue for companies worldwide, especially those with offshore operations. The COVID-19 pandemic has only exacerbated the problem, leading to increased shipping costs, delays, and disruptions. As a result, many companies are looking for alternative solutions to offshore manufacturing. In this article, we delve into the challenges posed by supply chain disruptions and explore a potential solution: nearshore manufacturing in Mexico.
Successfully Sourcing Suppliers in Mexico
Sourcing suppliers in Mexico for manufacturing your products can be challenging, but it can be done successfully with the right approach. The manufacturing sector in Mexico is well developed, making it a popular destination for companies looking to outsource production. The country is also known for its low labor costs, skilled workforce, and proximity to the United States, making it a great location for companies looking to reduce costs and increase productivity.
Supply Chain Questions You Should Answer Before Manufacturing in Mexico
You should always ask prospective manufacturing partners for specific supply chain metrics to make sure they’re capable of producing your product. Here are a few questions you should ask before reshoring manufacturing to Mexico:
- Turnover rate: Is your partner able to sustain a labor pool for his projects and increase them when needed?
- Factory costs: Is there some unforeseen overhead you may not have expected or need to plan for?
- Transportation costs: Again, with regards to location, what are the average costs and expenses related to the transportation of your goods to market?
- Port of Entry time for crossing trailers: If you have decided on a shelter manufacturing partner, what is the average time it takes for your goods to be transported across the border into the U.S.?
Why U.S. Companies Are Moving Their Supply Chains From China to Mexico
Does Mexico have supply chain issues? In spite of the fact that all exporting companies face supply chain challenges, Mexico seems to face fewer challenges than other manufacturing countries, such as China. Supply Chain Brain has a list of reasons why companies are moving their supply chains from China to Mexico.
Ground Transport
Goods can be imported from Mexico via ground transport in a matter of days or even hours. This is never an option for goods manufactured in China, from which everything must come by ocean or air. The former is very time consuming (it can often take weeks), and the latter is very expensive.
"Trusted Partner" Status for Customs
The U.S. offers two programs that help facilitate faster and easier Customs processing for U.S.-Mexico trade: FAST and C-TPAT. Initiated after 9/11, FAST is a trusted traveler/trusted shipper program that allows expedited processing for commercial carriers who have completed background checks and fulfill certain eligibility requirements (much like TSA Precheck for air travelers). FAST certification is for drivers; C-TPAT is a broader program that shippers must apply for. Once a company is certified for C-TPAT, its drivers can then apply for FAST. There are no such programs for U.S.-China trade.
A Transparent Landscape
There are also new modern options for transport that make Mexico attractive. Companies can coordinate door-to-door transportation between the U.S. and Mexico, including procurement of trucks on both sides of the border, customs clearance, insurance, financing, and reporting. This allows manufacturers to focus on their core competency, rather than logistics, and can also reduce the need for big in-house shipping and logistics teams.
Small Language Barrier
Spanish is the second-most common language spoken in the U.S., making it relatively easy to communicate with partners in Mexico (and find bilingual staff and vendors).
Spanish is the second-most common language spoken in the U.S., making it relatively easy to communicate with partners in Mexico (and find bilingual staff and vendors).
Government Incentives for Reshoring in Mexico
By strategically aligning with the global trend of reshoring, leveraging Mexico's proximity to the U.S., benefiting from favorable trade agreements like the USMCA, and tapping into cost advantages, companies can position themselves for sustained success. This white paper explores the nuanced details of government incentives in Mexico. It will provide a comprehensive guide for businesses navigating reshoring opportunities. Fill out the form to receive the white paper today.
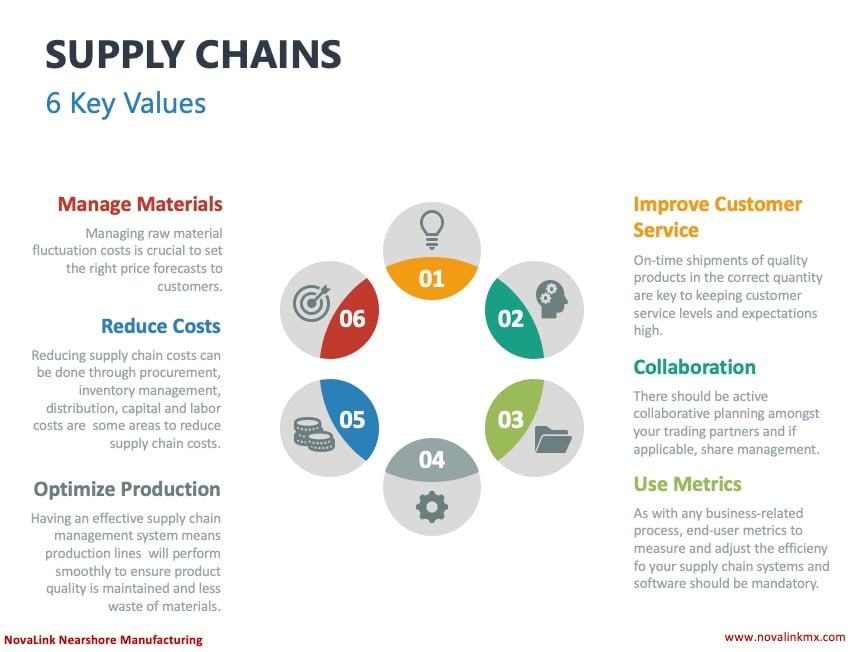
Supply Chains: 6 Key Values
We at NovaLink believe that manufacturing in Mexico should be simple, fast, and cost-effective. To understand the importance of a good supply chain to your manufacturing operations, please review the following graphic.
Are You Ready to Begin Manufacturing in Mexico? Contact Us for a Free Consultation
Contact us and let's start building something!
Use the details to the right to contact NovaLink.
Office
6665 Padre Island Highway
Suite B
Brownsville, Texas 78521
Hours
Mon-Fri: 8am - 5pm