Last Updated on February 26, 2024
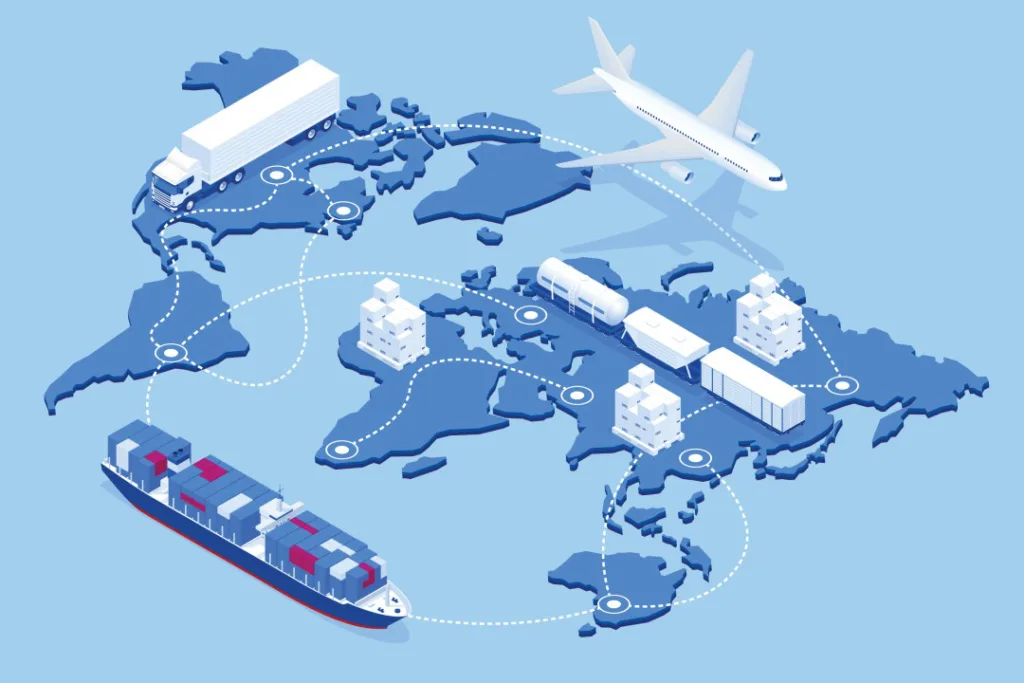
The COVID-19 pandemic exposed global supply chain vulnerabilities. Suddenly, toilet paper became a luxury, and essential medical supplies vanished overnight. It was a stark reminder that overdependence on distant production can come at a steep cost. This has sparked a surge in reshoring, the trend of returning manufacturing home. But is reshoring a silver bullet, or are there more nuanced considerations?
Understanding reshoring
Reshoring entails the relocation of manufacturing and production processes from overseas back to the country of origin. This strategic shift is driven by various factors, including the need for greater supply chain resilience, rising labor costs in offshore locations, and the desire to mitigate geopolitical risks.
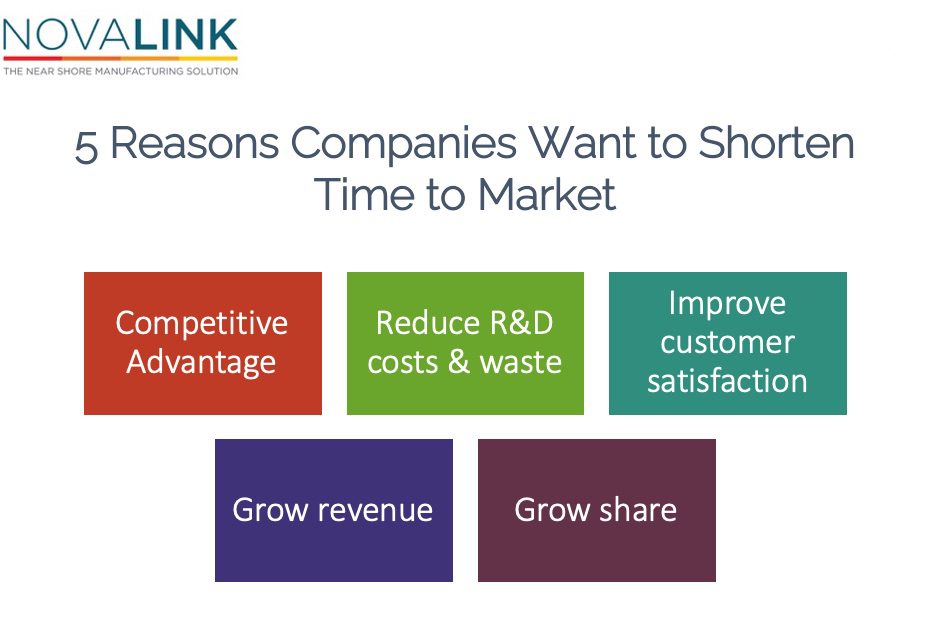
The Pre-Pandemic Landscape: Globalization's Double-Edged Sword
For decades, globalization fueled economic growth by allowing companies to source materials and labor from the cheapest locations. This led to lower production costs and, ostensibly, cheaper goods for consumers. However, this pursuit of efficiency often sacrificed transparency, sustainability, and resilience.
By sourcing materials and labor from countries with lower labor and manufacturing costs, businesses were able to capitalize on the economic boom, produce more goods and services, and minimize their costs. Today, businesses continue to look for ways to reduce costs and increase efficiency, and offshore suppliers still minimize costs in most instances for North American and European companies.
However, now we see how brittle these global supply chains are. A perfect storm of disease, war, technological innovation, overspecialization, unchecked climate change and geopolitical tensions have shattered global supply chains and had a significant impact on the global economy.
IBM
COVID-19: A Stress Test for Global Supply Chains
The pandemic exposed the fragility of long, complex supply chains. Global supply chains have revealed themselves to be like fragile houses of cards that can crumble when a breeze blows unexpectedly. Border closures, lockdowns, and transportation disruptions caused widespread shortages, highlighting the risks of relying on single sources, particularly overseas. Imagine building a house with bricks scattered across the globe – one missing component can stop the whole project.
The total cost of the current supply chain issues caused by the pandemic, labor shortages and the war in Ukraine is difficult to estimate, as the situation is constantly evolving. However, a 2022 report by the World Bank estimated that the global economy could lose up to USD 1.2 trillion in 2023 because of these disruptions. The report also found that disruptions to the global supply chain are likely to have a significant impact on developing countries, as these countries are more reliant on imported goods and services. The report estimates that developing countries could lose up to USD 426 billion in 2023 because of these disruptions.
IBM
Reshoring: A Lifeline or a Leap of Faith?
In response, reshoring has gained momentum. Governments and companies are increasingly looking to bring production closer to home, aiming for increased control, security, and quicker response times. According to BCI Global Report, more than 60% of US and European manufacturing companies planned on reshoring part of their supply chains by 2025. This shift reflects a desire to build more resilient and transparent supply chains.
Temporary trade restrictions and shortages of pharmaceuticals, critical medical supplies, and other products highlighted their weaknesses. Those developments, combined with the U.S.-China trade war, have triggered a rise in economic nationalism. As a consequence of all this, manufacturers worldwide are going to be under greater political and competitive pressures to increase their domestic production, grow employment in their home countries, reduce or even eliminate their dependence on sources that are perceived as risky, and rethink their use of lean manufacturing strategies that involve minimizing the amount of inventory held in their global supply chains.
Harvard Business Review
However, reshoring isn't a magic solution. Manufacturing requires significant investment in infrastructure, skilled labor, and automation. Additionally, higher labor costs in developed nations than some developing countries might mean price increases for consumers.
Navigating the New Landscape: A Balanced Approach
The answer lies not in blind allegiance to globalization or reshoring, but in finding a balance. Diversification, nearshoring (sourcing from geographically close countries), and strategic reshoring are all viable options depending on the specific product, industry, and risk tolerance.
Consider this: Is it essential to have every single component manufactured domestically? Perhaps reshoring key components while diversifying sourcing for less critical ones could be an optimal strategy.
Cost considerations
While offshoring was once seen as a cost-effective strategy, the landscape has shifted in the wake of the pandemic. Rising labor costs in traditional manufacturing hubs, coupled with increased transportation expenses and tariffs, have eroded offshore production cost advantages. Reshoring allows companies to streamline operations, reduce overheads, and maintain competitive pricing in the long term.
Quality and innovation
Reshoring also offers enhanced quality control and innovation. By bringing production closer to home, companies can closely monitor manufacturing processes, ensure compliance with industry standards, and implement agile production methods. Furthermore, proximity to research and development centers fosters collaboration and accelerates innovation.
The Road Ahead: Building a More Resilient Future
The pandemic has served as a wake-up call, urging us to rethink our approach to global production. By embracing diversification, strategic reshoring, and technological advancements, we can build more resilient and sustainable supply chains that can withstand future disruptions.
Remember, the goal is not to retreat from globalization, but to make it more robust and responsive to the needs of a complex and interconnected world.
Conclusion: Reshoring Emerges as a Strategic Imperative for Businesses
As we reflect on the lessons learned from COVID-19, reshoring emerges as a strategic imperative for businesses seeking to fortify their supply chains and adapt to an uncertain world. By prioritizing resilience, cost-effectiveness, and innovation, companies can position themselves for long-term success in the post-pandemic era.
About NovaLink
As a manufacturer in Mexico, NovaLink employs a unique approach that transcends the traditional model of shelter production. More than just the location of your manufacturing, we would like to become a partner in your manufacturing in Mexico. You will be able to relocate or initiate manufacturing for your company in Mexico in a low-cost labor environment with very little delay or up-front costs. Find out how we can help you by handling the manufacturing process.
There are NovaLink facilities in the border cities of Brownsville, Texas, Matamoros, Mexico, and Saltillo, Mexico.
Explore More: Discover Related Blog Posts
Expand your knowledge and delve deeper into more information about reshoring to Mexico with our curated collection of related blog posts.
- Can Moving Manufacturing to Mexico Really Be Turnkey? Here’s What You Need to Know
- What Type of Company Should Not Move to Mexico?
- Stop Waiting: Mexico Product Manufacturing Is Ready When You Are
- 3 Hidden Costs You’re Avoiding by Manufacturing in Mexico (And Why It Matters)
- What Your CFO Needs to See Before Approving a Move: Why Moving Manufacturing from China to Mexico Makes Dollars and Sense