Last Updated on February 21, 2024
Embarking on the journey of nearshore manufacturing can be an exciting yet daunting endeavor. As businesses seek to optimize their operations and tap into new markets, the transition from expectations to reality in nearshore manufacturing brings forth a myriad of challenges and opportunities. Let's delve into the nuances of starting nearshore manufacturing and uncover the intricacies that shape this transformative process.
Understanding Nearshore Manufacturing: An Introduction
Nearshore manufacturing entails the establishment of production facilities in close proximity to the target market, typically in neighboring countries or regions with favorable economic conditions. The allure of nearshore manufacturing lies in its potential to reduce lead times, lower shipping costs, and enhance supply chain resilience.
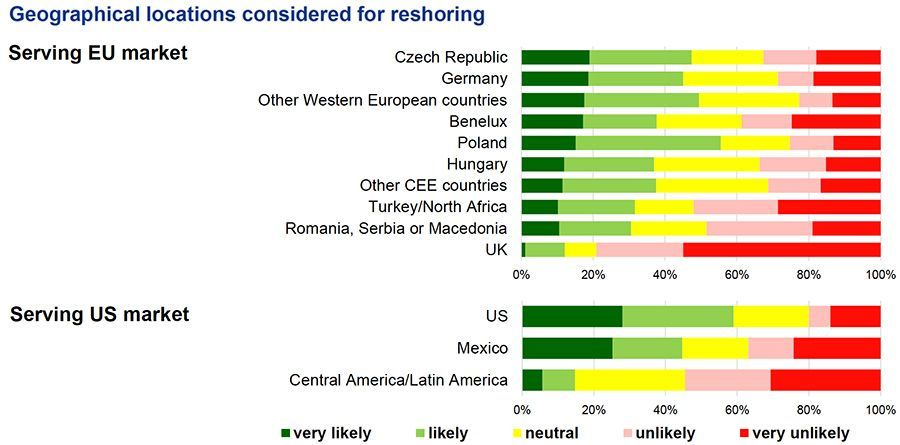
Expectation: I don't have a prototype product, but my company can make one for me.
Reality: Most Manufacturing Partners Do Not Produce Prototype Products
NovaLink does not produce spec products. Aside from the obvious legal and related trade issues, our company believes that having the functional product specifications and a product our staff can reverse engineer helps rapidly advance the product's time to enter production.
It is common practice for a company considering outsourcing manufacturing to have a prototype made before engaging a manufacturing service provider. Mexico does not typically have the capacity to deliver prototypes before production fruition unless another company makes a similar product in the country.
If a company needs a specification product completed, there are numerous resources available.
The primary reason for manufacturing prototypes of new products is to enable physical tests to take place on a fully representative sample of the designed product, prior to full production release.
These tests are useful as they can determine whether the product can do what it’s meant to. Your tests should be as meaningful as possible to replicate the true operational environment of the released product.
Technia UK
Expectation: I can run at a low volume or do a short run production.
Reality: Low Volume and Short Run Productions are Not Cost Effective
Having a nearshore manufacturing partner like Novalink necessitates a steady and consistent production flow. Companies seeking to engage with Novalink can do a short-run or limited product run as long as they have plans to continue to make the same short-run in the future.
The cost of producing the item and sourcing the labor would be too expensive for a manufacturing partner to undertake such an effort as a project. Consider the following:
- Setup Costs: Manufacturers incur significant setup costs when preparing production lines, tooling, and equipment for manufacturing processes. With low volumes or short runs, setup costs are spread over a smaller number of units, leading to higher per-unit costs.
- Economies of scale: Economies of scale refer to cost advantages gained when production volume increases. Manufacturers can achieve lower per-unit costs by spreading fixed costs (such as machinery, labor, and overhead) across a larger number of units. In low-volume or short-run productions, economies of scale are not fully realized, resulting in higher production costs.
- Material Costs: Purchasing materials in small quantities can be more expensive per unit than bulk purchases. Suppliers often offer discounts for larger orders, which reduces material costs. In low-volume or short-run productions, manufacturers may not qualify for these discounts, leading to higher material expenses.
- Labor Efficiency: Efficient labor utilization is crucial for cost-effective production. In low-volume or short-run productions, the time spent on setup, changeovers, and coordination between production runs may outweigh the actual time spent on manufacturing. This inefficiency increases labor costs per unit.
- Waste and Scrap: Manufacturing processes often generate waste and scrap, which adds to production costs. In low-volume or short-run productions, the proportion of waste per unit produced may be higher than larger production runs. This results in increased per-unit costs due to waste disposal and material losses.
- Flexibility and Adaptability: Manufacturers may prioritize flexibility and adaptability in production processes to accommodate changes in customer demand or product specifications. However, low volume or short-run production often requires additional setup time and resources, contributing to higher overall costs.
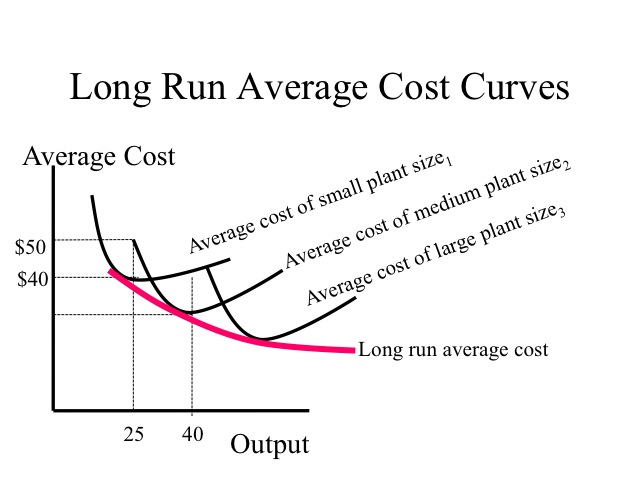
Expectation: I don't need a lot of money to get my nearshore manufacturing started.
Reality: Nearshore manufacturing requires a significant initial investment
In the case of a startup manufacturing operation, your nearshore project must be fully funded by an investor. There are several reasons for this:
- Initial Investment: Nearshore manufacturing requires a significant initial investment to establish production facilities, procure equipment, secure real estate, and hire skilled labor. These expenses can add up quickly and require substantial financial resources.
- Operating Costs: Beyond the initial setup costs, nearshore manufacturing operations incur ongoing expenses such as labor wages, utility bills, raw material procurement, equipment maintenance, and compliance with regulatory requirements. These operating costs can be substantial and must be factored into financial planning for manufacturing operations.
- Infrastructure Development: Developing the necessary infrastructure to support manufacturing activities, including transportation networks, utilities, and supply chain logistics, may require additional investment. Depending on the location and scale of the manufacturing operation, infrastructure development costs can vary but are typically significant.
- Market Research and Compliance: Conducting thorough market research to identify target markets, understand customer needs, and assess regulatory compliance requirements is essential for nearshore manufacturing. Investing in market research and ensuring compliance with local regulations and industry standards often entails financial expenditures.
- Risk Management: Like any business venture, nearshore manufacturing involves inherent risks that must be managed effectively. Allocating financial resources for risk mitigation strategies, contingency planning, and insurance coverage is essential to protect investments and ensure business continuity.
- Scaling Operations: While it may be possible to start with a small investment initially, scaling up nearshore manufacturing operations to meet growing demand or expand into existing markets often requires an additional capital infusion. Planning for future expansion and allocating funds accordingly is critical to long-term sustainability and growth.
While it may be possible to initiate nearshore manufacturing with less capital than traditional manufacturing models, the statement underestimates the financial requirements and complexities associated with starting and running a successful manufacturing operation. Adequate financial planning, prudent investment decisions, and diligent risk management are essential for nearshore manufacturing success.
There will always be a need for capital when starting up an outsourced manufacturing project in Mexico or relocating an existing one. However, with NovaLink, we have the infrastructure in place. We also provide the ability for a company to start small and grow into a larger footprint to meet its changing needs. This means that companies with whom we partner absorb the overhead proportional to the space and employee level required. Furthermore, NovaLink saves its customers upfront investment in that the client does not need to incorporate in Mexico or hire legal experts to negotiate union contracts and acquire permits. We already have this in place. NovaLink is also positioned to assist manufacturers with capital investment if required.
Jason Wolfe, NovaLink CEO
Expectation: I have an idea for manufacturing a product and I want a nearshore manufacturing company help me get it to reality.
Reality: Manufacturing a concept requires too many legal and logistical considerations
All manufacturing companies would love to be a part of the next big thing! However, getting a product from concept to reality will require much footwork on the client's part beforehand.
- Lack of Clarity: While having an idea for a product is a crucial starting point, it is essential to have a clear understanding of the product concept, design specifications, target market, and manufacturing requirements before engaging with a nearshore manufacturing company. Without a well-defined plan, the manufacturer may struggle to provide accurate guidance or support.
- Feasibility Assessment: Before manufacturing, it is essential to assess the feasibility of the product idea in terms of technical requirements, market demand, regulatory compliance, and production costs. Engaging with a nearshore manufacturing company prematurely without conducting feasibility studies may lead to unrealistic expectations or potential setbacks down the line.
- Communication and Collaboration: Effective communication and collaboration between the product developer and the manufacturing partner are crucial for bringing a product to reality. It is imperative to establish clear channels of communication, define roles and responsibilities, and align expectations regarding timelines, quality standards, and pricing structures. This is before initiating the manufacturing process.
- Resource Allocation: Developing an innovative product and bringing it to market often requires significant resources, including financial investment, time, and expertise. It is imperative to assess whether the nearshore manufacturing company has the capabilities, resources, and experience necessary to support the product development process effectively.
- Intellectual Property Protection: Protecting intellectual property rights is paramount when engaging with a manufacturing partner to bring an innovative product to market. It is essential to establish appropriate legal agreements, such as non-disclosure agreements (NDAs) and manufacturing contracts, to safeguard proprietary information and prevent unauthorized use or reproduction of the product design or technology.
- Market Research and Validation: Before manufacturing, it is advisable to conduct thorough market research and validation to assess the viability of the product concept, understand customer needs and preferences, and identify potential competitors. Engaging with a nearshore manufacturing company without market research may result in producing a product lacking market demand or competitive advantage.
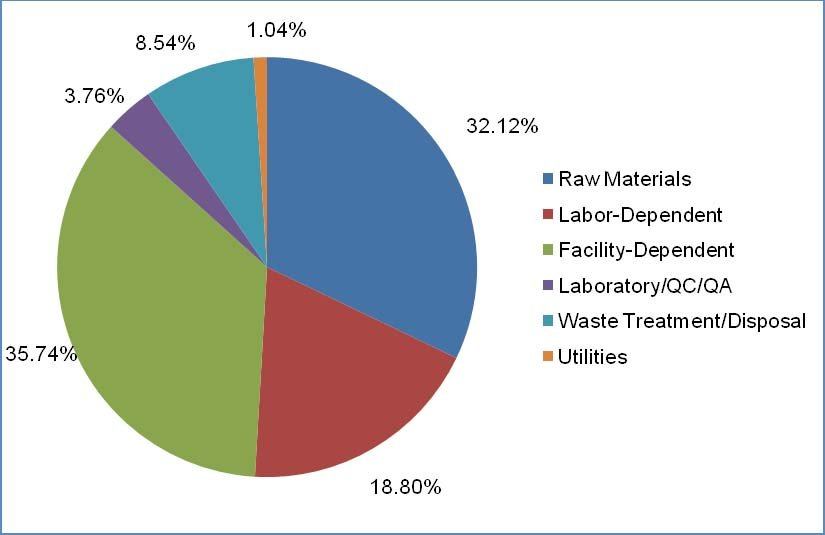
While seeking the assistance of a nearshore manufacturing company to bring a product idea to reality can be a viable option, it is important to approach the process thoughtfully, ensuring clarity, feasibility, communication, resource allocation, intellectual property protection, and market validation are addressed effectively. Rushing into manufacturing without proper planning and preparation may lead to challenges and setbacks in realizing the product vision.
Expectation: My nearshore manufacturing partner can provide me with the equipment I need to begin manufacturing.
Reality: Finding and sourcing the equipment is very time-consuming and will delay the beginning of production
Nearshore manufacturing partners such as NovaLink can help their customers obtain equipment for their production if they do not have the necessary machinery. However, finding and sourcing the equipment is very time-consuming (as well as finding the labor to run the equipment) and will delay production. In addition, there are several other factors to consider:
- Equipment Availability: While some nearshore manufacturing partners may offer equipment rental or leasing options, not all companies have the capacity or capability to provide the specific equipment needed for a particular manufacturing process. Equipment availability may vary depending on the type of manufacturing operation, industry specialization, and technological requirements.
- Compatibility and Suitability: Even if a nearshore manufacturing partner offers equipment, it is essential to ensure that the equipment is compatible with the manufacturing processes, production volumes, and quality standards required for the intended product. Using unsuitable or outdated equipment may compromise product quality, efficiency, and manufacturing performance.
- Cost Considerations: Acquiring manufacturing equipment can involve significant upfront costs, maintenance expenses, and depreciation over time. While leasing or renting equipment may provide flexibility in cash flow, it is imperative to consider the long-term financial implications and total cost of ownership associated with equipment procurement.
- Technical Support and Maintenance: In addition to providing equipment, a manufacturing partner should also offer technical support, training, and maintenance services to ensure optimal performance and uptime. Depending solely on the availability of equipment without adequate support mechanisms in place may pose challenges in troubleshooting issues, optimizing production processes, and addressing equipment failures or downtime.
- Ownership and Control: Depending on the contractual agreements and arrangements with the manufacturing partner, there may be limitations or restrictions regarding ownership, control, and access to the equipment. Clarifying the terms and conditions regarding equipment usage, ownership rights, and access privileges is essential to avoid misunderstandings or disputes in the future.
- Scalability and Flexibility: As manufacturing requirements evolve and production volumes fluctuate, it is imperative to assess whether the manufacturing partner's equipment can scale and adapt to changing business needs effectively. Investing in flexible and scalable equipment solutions ensures agility, responsiveness, and competitiveness in dynamic market environments.
Prospective customers may wish to consult with a company like NovaLink beforehand to understand better the equipment they may need and its cost. The options option of finding the equipment for itself will help to shorten the timeline and get production off the ground more rapidly.
Expectation: I will need a large labor pool to start nearshore manufacturing
Reality: Depending on the product, you may not need a large labor production staff to start
This depends on the product a company seeks to produce. A simple product may only require five employees to manufacture. While on the other hand, a larger, more complex product that requires more machinery, or a product that needs to be assembled, will need more labor.
Cut and sew products, especially ones with multiple pieces to be created and assembled, like a handbag or complex garment, are very labor-intensive. However, some products require simple assembly and can be produced in a single unit may require less labor. The most effective way to determine if a product will require a large labor pool to produce is to have a specification/demo made and have Novalink’s engineers examine it. Then, the company's manufacturing experts can determine if the product needs a large assembly in Mexico team to make it.
Having a small labor and production staff for a nearshore manufacturing project may suffice during the initial stages when operations are relatively small-scale and demand is manageable. However, as production scales up due to increasing success and market demand, it becomes imperative to plan for a larger labor force. Scaling up production necessitates higher production vol
umes, tighter deadlines, and potentially more complex manufacturing processes. A larger staff enables the company to handle the increased workload efficiently, maintain production quality, and meet customer expectations. Additionally, a larger labor force can offer flexibility in scheduling, allow for specialization in different areas of production, and enhance overall productivity. By anticipating the need for expansion and strategically planning for a larger staff, nearshore manufacturing projects can better position themselves to capitalize on growth opportunities. This will enable them to sustain long-term success in the competitive marketplace.
Expectation: There will be a lot of government red tape when starting a nearshore manufacturing operation.
Reality: Government regulations are common in manufacturing, but a nearshore manufacturing partner can help you navigate them.
Any large manufacturing project, whether in the United States or Mexico, will require you to navigate through the regulations associated with that country – which is an inevitable reality. However, it does not have to be a bureaucratic nightmare that stops your project in its tracks. There are experts in nearshore manufacturing companies like NovaLink that can help you navigate your way through the required regulations, forms, and inspections.
In addition, as mentioned previously, the more legwork committed on the front end of your project, the easier it will be for you to anticipate what is required from the bureaucracy of your country of origin, like Mexico, to allow you to budget time and plan for these contingencies.
Conclusion: Navigating the Realities of Nearshore Manufacturing
In conclusion, starting nearshore manufacturing requires a nuanced understanding of the expectations versus reality paradigm. While the promise of efficiency and cost savings is enticing, businesses must navigate a complex landscape of challenges and opportunities. By building strategic partnerships, embracing technology, and prioritizing operational excellence, businesses can unlock the full potential of nearshore manufacturing and drive sustainable growth in a competitive global market.
FAQs about Starting Nearshore Manufacturing
Q1: What should I expect when starting nearshore manufacturing?
A1: When starting nearshore manufacturing, you can expect benefits such as reduced costs, shorter supply chains, improved communication, and easier logistics management. Additionally, nearshore manufacturing can provide access to a skilled labor force, regulatory alignment, and proximity for quality control and coordination.
Q2: Is it realistic to expect a seamless transition when starting nearshore manufacturing?
A2: While nearshore manufacturing offers numerous advantages, it is important to recognize that a seamless transition may not always be immediate. Factors such as cultural differences, language barriers, supply chain adjustments, and learning curves can impact the initial transition. However, with proper planning, effective communication, and collaboration with experienced partners, the transition can be smooth over time.
Q3: What are the common challenges businesses face when starting nearshore manufacturing?
A3: Some common challenges include adjusting to a different business culture, understanding local regulations and labor laws, establishing reliable supplier networks, managing logistics, and aligning production processes. Cultural differences and language barriers can also pose communication and collaboration challenges. However, working closely with experienced partners can help navigate these challenges effectively.
Q4: Can I expect cost savings when starting nearshore manufacturing?
A4: Yes, nearshore manufacturing often offers cost savings compared to domestic manufacturing or offshoring. Factors such as lower labor costs, reduced shipping expenses, and improved supply chain efficiencies contribute to cost savings. However, it is crucial to consider other factors like initial setup costs, taxes, tariffs, and ongoing operational expenses when evaluating the overall cost-effectiveness.
Q5: How long does it typically take to see the benefits of nearshore manufacturing?
A5: The timeline for experiencing the benefits of nearshore manufacturing can vary depending on factors such as project complexity, the maturity of your manufacturing processes, and the level of preparation and collaboration. While some benefits may be noticeable in the early stages, it generally takes time to optimize operations, establish efficient supply chains, and build strong relationships with local partners.
About NovaLink
As a manufacturer in Mexico, NovaLink employs a unique approach that transcends the traditional model of shelter production. More than just the location of your manufacturing, we would like to become a partner in your manufacturing in Mexico. You will be able to relocate or initiate manufacturing for your company in Mexico in a low-cost labor environment with very little delay or up-front costs. Find out how we can help you by handling the manufacturing process.
There are NovaLink facilities in the border cities of Brownsville, Texas, Matamoros, Mexico, and Saltillo, Mexico.