Last Updated on April 11, 2024
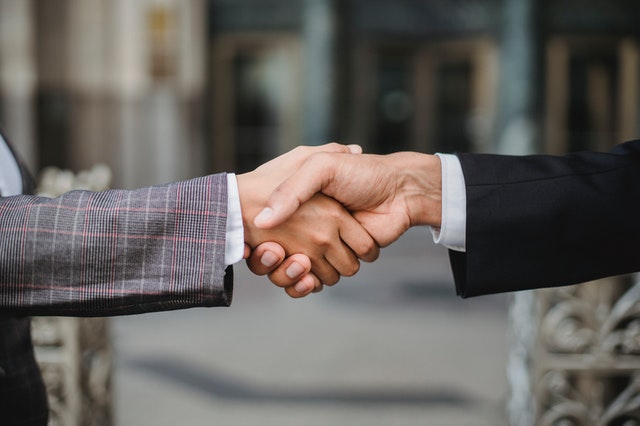
In today's dynamic manufacturing landscape, navigating the ever-evolving complexities of production can feel like scaling Mount Everest. Manufacturers constantly grapple with increasing demand, fluctuating costs, and the need to adapt to technological advancements. But what if there was a way to achieve peak performance without going it alone? Enter the strategic partnership with a secondary manufacturer. This collaboration can be the game-changer your business needs to surmount challenges and propel growth.
The Use of a Secondary Manufacturing Partner to Mitigate Risk
It is impossible to predict all the possible outcomes when a manufacturing partnership begins. A natural disaster or adverse weather can prevent a manufacturing operation or supplier from fulfilling its commitments. How will you respond if an event interrupts your production?
Another common problem is the change in production. The volume of an order may be too much for your current manufacturing partner or supplier if you are at capacity and suddenly have a large and expected order to fill.
By having a secondary manufacturing partner or supplier, these risks can be mitigated. The fallback plan should always be in place when offloading the excess volume or turning over part of the operation that was interrupted by the unexpected event to a secondary source.
“The most common reason to seek and develop a secondary source relationship with a supplier is simply to alleviate the risks associated with production interruptions due to complete dependence on one supplier for a portion of the component materials or assembly services.”
The Strategic Sourceror
Is There a Best Time to Implement a Secondary Manufacturing Partner Strategy?
The timing for implementing a secondary manufacturing partner strategy depends on various factors specific to your business, industry, and market conditions. However, there are some scenarios where implementing such a strategy might be particularly advantageous:
- Capacity Constraints: When your primary manufacturing facilities are operating at maximum capacity, and there is a growing demand for your products, it might be the right time to engage a secondary manufacturing partner to meet the increased production needs.
- Seasonal Demands: If your business experiences seasonal fluctuations in demand, having a secondary manufacturing partner can help you scale production during peak seasons without overburdening your primary facilities during slower periods.
- Geographical Expansion: When expanding into new markets or regions, partnering with local manufacturers through a secondary manufacturing strategy can help reduce transportation costs, shorten lead times, and navigate regulatory requirements more efficiently.
- Diversification of Risk: Relying solely on one manufacturing facility or location carries inherent risks. Having a secondary manufacturing partner can mitigate risks associated with supply chain disruptions, natural disasters, political instability, or unforeseen events affecting your primary operations.
- New Product Launches or Innovations: Introducing new products or innovations may require additional production capabilities that your primary manufacturing facilities cannot accommodate immediately. Engaging a secondary manufacturing partner can expedite the ramp-up process and facilitate faster market entry.
- Cost Optimization: Depending on the cost structure and capabilities of potential secondary manufacturing partners, integrating them into your supply chain may offer cost advantages through economies of scale, lower labor costs, or access to specialized expertise.
Boosting Specialization and Efficiency With A Secondary Manufacturing Partner
Imagine your manufacturing process as a well-oiled machine. Each component, from initial design to final assembly, plays a crucial role in smooth operation. However, just like a car doesn't need an engine to handle steering, not every manufacturer needs to be an expert at every stage of production.
A secondary manufacturing partner acts as an extension of your team, bringing specialized expertise and advanced capabilities to the table. This allows you to focus on your core competencies, whether product design, quality control, or final assembly.
Think of it this way: You wouldn't expect your bakery to grow its own wheat, mill the flour, and bake the bread, would you? By partnering with a flour mill, the bakery can optimize its resources and deliver exceptional products without getting bogged down in extraneous tasks.
Secondary Manufacturing Process for Your Finished Product
For your finished product, a secondary manufacturing partner may be able to provide you with a secondary manufacturing process. Secondary manufacturing typically involves additional processes beyond the initial manufacturing steps to transform raw materials or partially completed goods into final products. This can include assembly, finishing, packaging, labeling, and other steps necessary to prepare the product for distribution and sale.
For instance, if a company produces components or parts, a secondary manufacturing partner may handle the assembly of these components into finished products. This secondary manufacturing stage adds value to the components by creating a market-ready product. This includes:
- Casting and Molding
- Forming
- Separating
- Conditioning
- Finishing
- Assembling
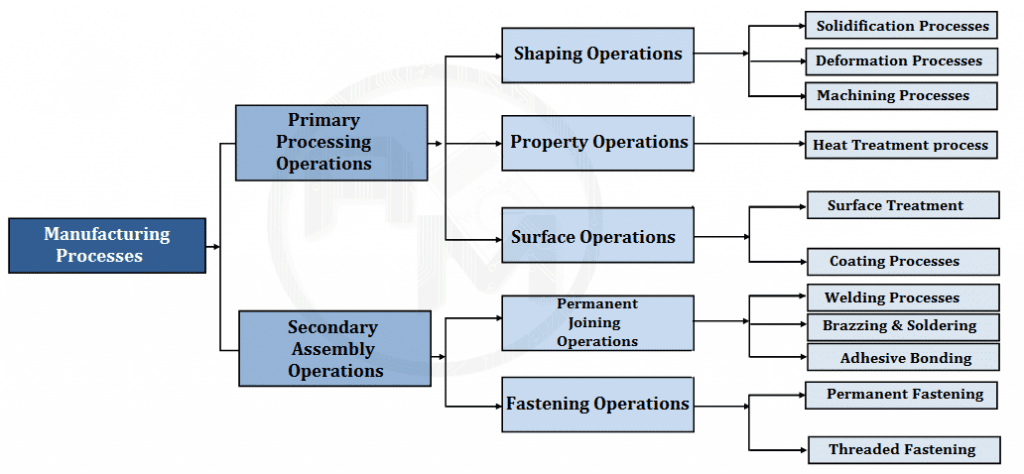
Finding a Secondary Manufacturing Partner Is Less Expensive Than Starting a New Line
Finding a secondary manufacturing partner is often less expensive than starting a new production line from scratch. There are several reasons for this cost advantage:
- Infrastructure Costs: Setting up a new production line requires significant investment in infrastructure, including purchasing or leasing manufacturing equipment, acquiring suitable facilities, and establishing necessary utilities and support systems. In contrast, partnering with a secondary manufacturing partner allows you to leverage their existing infrastructure, reducing upfront capital expenditures.
- Time and Resources: Developing a new production line entails extensive planning, design, procurement, installation, and testing processes, which consume valuable time and resources. By collaborating with a secondary manufacturing partner, you can expedite the production process and focus your resources on core business activities such as product development, marketing, and distribution.
- Operational Efficiency: Established manufacturing partners often possess streamlined processes, optimized workflows, and experienced personnel, leading to higher operational efficiency and lower production costs compared to starting anew. Additionally, secondary manufacturing partners may have access to economies of scale, bulk purchasing discounts, and specialized expertise that can further drive down costs.
- Flexibility and Scalability: Partnering with a secondary manufacturing partner offers greater flexibility and scalability compared to investing in new production lines. You can adjust production volumes, shift manufacturing locations, or diversify product lines more easily in response to changing market demands, without incurring the rigidity and sunk costs associated with dedicated facilities.
- Risk Mitigation: Starting a new production line entails inherent risks, including market uncertainties, technology adoption challenges, and operational disruptions. By collaborating with an established manufacturing partner, you can mitigate these risks by leveraging their industry knowledge, market insights, and proven track record of successful production.
In addition to capacity, scale-up at the new source, cost measures, and supply chain mitigation, the implementation of a second source is also subject to many factors and risks. Nonetheless, if the advantages of a secondary manufacturing source outweigh the tradeoffs in price, capacity, and risk mitigation, then you should absolutely consider it.
Selecting a Competitive Partner for Secondary Manufacturing
Having a secondary manufacturing partner or supplier has benefits, but you should proceed with caution and choose your new source wisely: Not all secondary sourcing manufacturing partners are up to the task. Be prepared to thoroughly vet their capabilities to determine if they are the right fit for your operations with respect to quality (very critical), consistency and timeliness.
“When it comes to finding a secondary supplier, often their best ability is availability. Do they have a reputation for doing whatever it takes to get the job done? Are they flexible enough to be responsive to your needs, especially after an unforeseen impediment jeopardizes your on-time production schedule? Will they work with you to ensure seamless quality, consistency and fulfillment? Seeking out honest answers to these questions will help you determine the fit and future of a secondary sourcing partnership.”
3 Reasons Why Manufacturers Should Work with Secondary Sourcing Partners
Conclusion: Building a Collaborative Future
The key to a successful secondary manufacturing partnership lies in collaboration and open communication. By clearly defining expectations and establishing seamless communication channels, you can foster a mutually beneficial relationship that drives innovation and shared success.
Partnering with a secondary manufacturer is not a sign of weakness; it's a strategic move towards enhanced efficiency, cost optimization, and long-term growth. By embracing collaboration and leveraging the expertise of others, manufacturers can unlock their full potential and conquer the ever-evolving challenges of the industry.
FAQs on Secondary Manufacturing Partners
Q1: What is a secondary manufacturing partner?
A1: A secondary manufacturing partner refers to a company or supplier that specializes in providing secondary manufacturing services to complement the primary manufacturing process. These services may include assembly, packaging, labeling, finishing, testing, or any other processes necessary to complete the final product.
Q2: Why is choosing the right secondary manufacturing partner important?
A2: Choosing the right secondary manufacturing partner is important as they play a critical role in the overall manufacturing process. They contribute to the final product's quality, efficiency, and timely delivery. A reliable and competent partner ensures seamless coordination between primary and secondary manufacturing, leading to a smooth production flow and customer satisfaction.
Q3: What factors should be considered when selecting a secondary manufacturing partner?
A3: When selecting a secondary manufacturing partner, key factors to consider include their expertise and capabilities in the required manufacturing processes, quality control measures, capacity to handle production volumes, reliability in meeting deadlines, proximity to the primary manufacturing facility, and their track record in the industry. Effective communication and a good cultural fit are also important considerations.
Q4: How can a secondary manufacturing partner contribute to cost savings?
A4: A secondary manufacturing partner can contribute to cost savings by offering specialized expertise and equipment, reducing the need for capital investment in secondary manufacturing processes. They can optimize production efficiency, minimize waste, and improve resource allocation. Additionally, partnering with a secondary manufacturer in a lower-cost region can offer cost advantages compared to performing secondary manufacturing in-house.
Q5: What role does collaboration play in successful partnership with a secondary manufacturer?
A5: Collaboration is crucial for a successful partnership with a secondary manufacturer. It involves clear communication, sharing of technical specifications, and aligning goals and expectations. Regular collaboration facilitates smooth production handoffs, ensures quality standards are met, enables problem-solving, and promotes a mutually beneficial and long-lasting partnership.
About NovaLink
As a manufacturer in Mexico, NovaLink employs a unique approach that transcends the traditional model of shelter production. More than just the location of your manufacturing, we would like to become a partner in your manufacturing in Mexico. You will be able to relocate or initiate manufacturing for your company in Mexico in a low-cost labor environment with very little delay or up-front costs. Find out how we can help you by handling the manufacturing process.
There are NovaLink facilities in the border cities of Brownsville, Texas, Matamoros, Mexico, and Saltillo, Mexico.