Last Updated on June 16, 2025
![Why Vietnam's Manufacturing Industry is Facing Similar Challenges to China's [2024]](https://novalinkmx.com/wp-content/uploads/2020/10/319765_4709372212529105_vna_potal_thanh_pho_ho_chi_minh_tam_dung_hoat_dong_san_xuat_doi_voi_cong_ty_tnhh_pouyuen_viet_nam_4601617-7cmf0ao84otlhxtq3zkk95ajkgrdgb7nskpwb9176tc-jpeg.webp)
Manufacturers are seeking to relocate their operations to a new location amid the exodus of businesses manufacturing in China and reshoring to North America. Vietnam is one of the most popular alternative destinations, which manufacturers view as a viable alternative to China. However, manufacturing in Vietnam has many of the same problems as China (with the exception of trade tariffs). In this blog post we examine the problems of Vietnam as a manufacturing destination and why moving manufacturing to Mexico might be a better choice.
“With the U.S. and China tangled in a nasty trade fight, this should be Vietnam’s time to shine. Instead, it is becoming increasingly clear that it will be years, if ever, before this Southeast Asian nation and other aspiring manufacturing destinations are ready to replace China as the world’s factory floor. “
Wall Street Journal
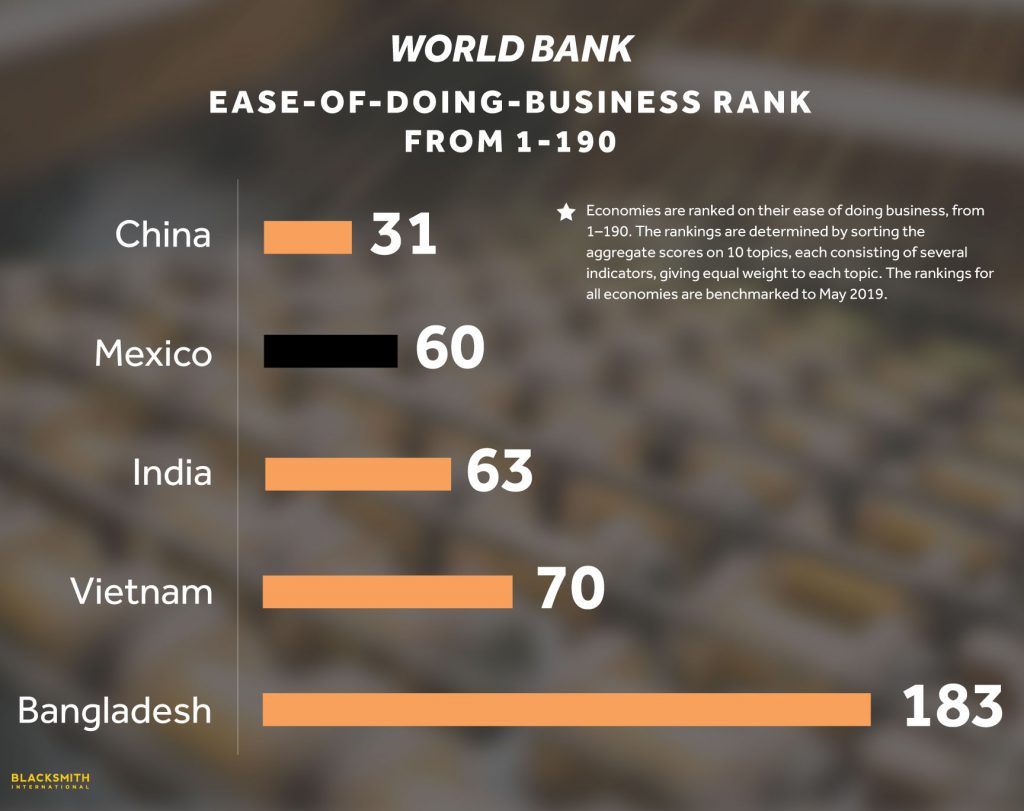
Source: Blacksmith International
Vietnam and the US Tariffs
President Trump announced reciprocal tariffs on Vietnam in April 2025.
Tariffs on Vietnam have been paused until July 2025. In Vietnam, which relies heavily on exports to the United States and foreign investment to grow, this could undermine growth.
Vietnam Is Directly Affected by the Impact
Most of the country's largest export sectors rely heavily on the US market, including textiles and garments, electronics, footwear, seafood, and furniture.
Vietnam exports nearly 30% of its total product to American consumers, so tariffs ranging from 10% to 40% could erode price competitiveness, trigger order cancellations, and force businesses to absorb margin losses or shift production.
Manufacturing in Vietnam Has The Same Logistics Problems As China
Companies that promote Vietnam as a manufacturing destination emphasize that the country's proximity to China makes it an ideal location. In any case, what is not stated is that both of these countries are located across the Pacific in Asia, and that if you decide to manufacture in Vietnam, you will almost certainly face the same issues you face in China as well. Due to its location in the Far East, Vietnam is a logistical challenge for manufacturing companies seeking to manage lean supply chains.
“The COVID-19 pandemic has taught us many things. One of the biggest lessons learned has been that we cannot take our supply chain for granted. If you are considering moving your production to Vietnam, take a long, hard look at your supply chain and make sure that you can get your inputs — from raw materials to components — into the country and to your partner’s factory. Examine how much that will cost.”
Gembah Blog
Long Distances to Ship Completed Products
It is approximately 7,641 miles across the Pacific ocean from the port of Long Beach, California to Haiphong Harbor, Vietnam's largest port (located in the northern part of the country outside of Hanoi).
It will take an additional 1,000 miles or more in freight shipping to deliver your products to another major city such as Houston, Boston, or New York. You will need to send your cargo through the Panama Canal to reach any Gulf Coast or Eastern seaboard states, nearly doubling the time it takes for your cargo to reach your destination...just as it does for shipping from Chinese ports.
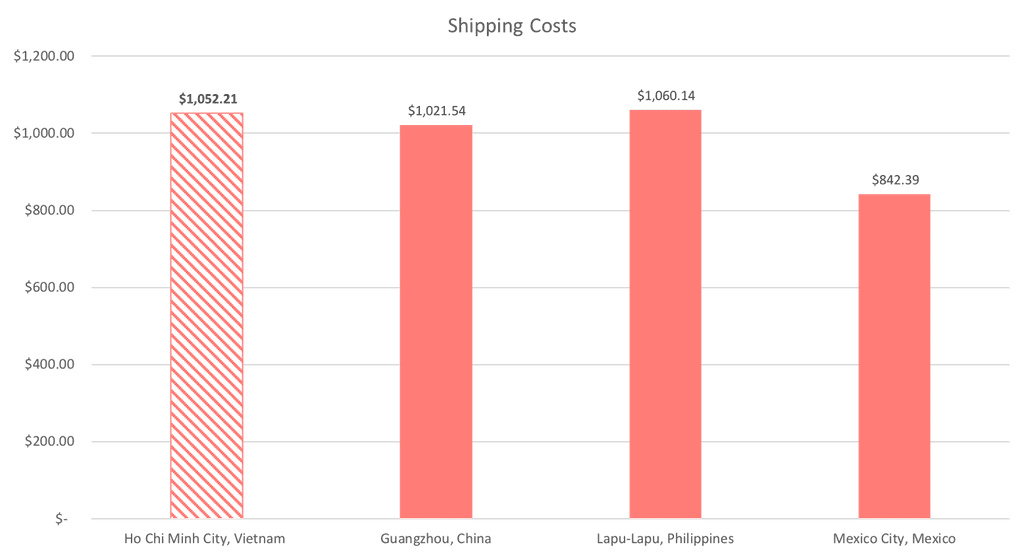
Source: Sourcify, “All You Need to Know about Manufacturing & Sourcing in Vietnam” https://www.sourcify.com/all-you-need-to-know-about-manufacturing-in-vietnam/
Vietnam Has Raising Labor Costs
Starting in July 2024, the minimum wage in Vietnam increased by 6 percent. It represents a compromise between the 6.48 to 7.3 percent requested by the Vietnam General Confederation of Labor and the 4.5 to 5 percent suggested by the Vietnam Chamber of Commerce and Industry. The minimum wage hike followed a two-year hiatus despite rising inflation rates, which may necessitate further increases.
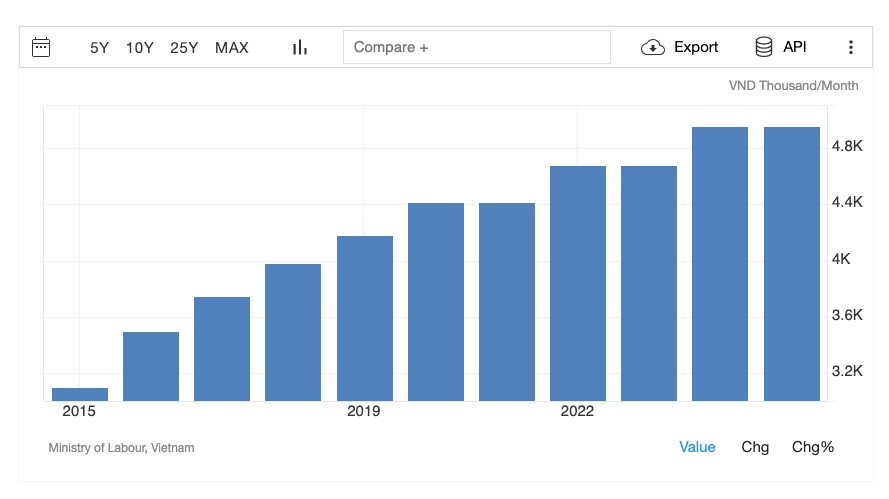
Vietnam Has a Poor Transportation Infrastructure
The transportation infrastructure in Vietnam is rated as weak and inconsistent, with some claiming it lags behind that of many other developed economies. Road transport infrastructure in Vietnam ranks 103rd globally, while seaports and air transport infrastructure rank 83rd and 103rd, respectively.
Vietnam only has 4 major ports: Hai Phong, Da Nang, Qui Nhon, and Ho Chi Minh City. Vietnam ranks 80 among 139 countries on the quality of port infrastructure, with an average score of 3.80 on a scale of 1 (lowest) to 7 (highest) between 2006 and 2018. This means Vietnam ranks lower than countries such as China, India, Thailand, and Sri Lanka. Vietnam has 44 seaports with a total capacity of 470-500 million tons per year. The Vietnam Port Association (VPA) states that 80 percent of container exports and imports go through smaller ports and ships, a process known as transshipment. The VPA also noted that goods owners have losses of approximately US$2.4 billion each year due not using deep-water ports.”
Vietnam briefing
Taking into account the fast trade growth and the slow improvement of infrastructure in Vietnam is one of the most important considerations. It has been decades since a major railway connecting Hanoi and Ho Chi Minh City, where the international airport is located, has been upgraded. Furthermore, the increased volume of trade poses the risk of ports reaching their maximum capacity.
In addition, only 20% of the roads on the national highway system in Vietnam are paved. In the event that the means of transporting the finished goods from the factory to the distribution center become unreliable, you will be introducing a level of risk into your supply chain.
The Sourcing Of Goods And Facilities in Vietnam Is Not As Good As In Mexico
Sourcing goods and facilities in Vietnam might not be quite as easy as in Mexico. Here's a breakdown of the pros and cons:
Mexico's Advantages in Sourcing:
- Proximity to the US: Mexico's location next to the US makes transportation and logistics much simpler, especially for companies based in North America. Shorter distances translate to faster deliveries and potentially lower costs.
- Established Supply Chains: Mexico has a long history of manufacturing for the US market. This means there's a well-developed network of suppliers and manufacturers familiar with US standards and regulations. Finding established vendors can be quicker and smoother.
- Similar Infrastructure: Mexico's infrastructure, including roads, ports, and transportation systems, is generally more developed than Vietnam's. This can make moving goods around within the country more efficient.
Vietnam's Sourcing Challenges:
- Limited Raw Materials: Vietnam may not have all the raw materials needed for certain products, requiring imports, often from China. This adds a layer of complexity to sourcing.
- Newer Supplier Network: While Vietnam's manufacturing sector is growing, the network of suppliers might be less extensive compared to Mexico's established system. Finding the right vendor for specific needs could take longer.
When it comes to manufacturing, it is imperative that you obtain materials in which to produce your products. There are limited resources for materials in Vietnam, particularly in comparison with Mexico and China.
“Finding local suppliers in Vietnam is much more complicated than in China. And, since there are fewer options, their costs will generally be higher. If the supplier is far away from your factory, receiving incorrect or damaged components has a much higher impact as sending them back can be difficult.”
Manufacturing Improvement Blog
The availability of inexpensive manufacturing facilities is another challenge in Vietnam. With the relocation of manufacturing to Vietnam by other countries, the price for space has risen significantly and there is a shortage of space.
“The cost to rent industrial land on a long-term lease at one Vietnamese industrial park in 2018 also increased to $90 per square meter (10.76 square feet), up from $60 to $70 in 2017. And the monthly rent for existing factory buildings in industrial parks near Ho Chi Minh City has risen to $4 per square meter, up from $3 last year.
Time is of the essence for manufacturers looking to build new facilities in Vietnam. As one industrial park executive noted in late 2018: You must be quick… our land is running out soon. A lot of Chinese factory bosses come to visit our industrial park every week.“
InTouch
Vietnam Often Relies on China and Korea for Parts or Materials
One major vulnerability in Vietnam's manufacturing sector is its dependence on China for parts and materials. This creates a domino effect, where any disruptions in China's supply chain - factory shutdowns, port congestion, or raw material shortages - can ripple through to Vietnam. Vietnamese manufacturers suddenly find themselves unable to secure essential components, stalling production lines and delaying deliveries. This not only hurts Vietnam's businesses but can also damage its reputation as a reliable exporter.
Vietnam relies heavily on imports of intermediate goods such as semi-processed products and capital goods from China and South Korea, This has resulted in large trade deficits with these countries — in particular with China.
Vietnam Briefing
China and Vietnam have not always enjoyed a good relationship; the Vietnamese government cracked down on parts labeled "Made in Vietnam" as exporters in China used the ruse to avoid U.S. tariffs.
Vietnam Has Inexperienced Workers And Uneducated Workforce
Workers in Vietnam are often uneducated and unskilled, in contrast to their counterparts in Mexico or China: companies considering shifting manufacturing production to Vietnam should also consider the risks associated with a workforce that is relatively inexperienced with sophisticated manufacturing techniques.
A report by the Healy Consulting Group found that only 22 percent of the Vietnamese workforce has any certification from university, professional college, professional secondary school or vocational training. The number of untrained workers in China is similar (China’s 76 percent to Vietnam’s 78 percent) according to state-run China Daily, but they make up for deficiencies with their sheer numbers of workers.
As a result of the large number of companies relocating manufacturing to Vietnam and the rising demand for labor, wages have increased:
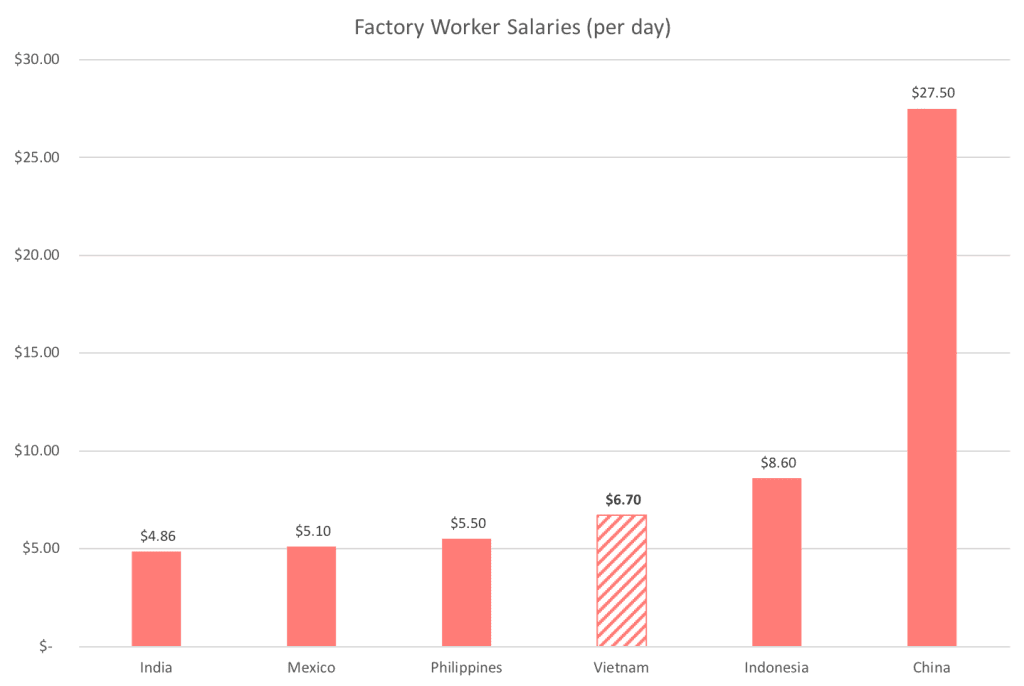
Source: Vietnam Global
“Vietnam’s low labor cost appeal to foreign investors is facing decline due to a rapid rise in minimum wages across the country, experts warned. According to reports from global financial information services provider Fitch Group, Vietnam was among three countries in East and South East Asia that saw the largest year-on-year average minimum wage growth rates between 2015 and 2019 with 8.8 per cent, just behind Laos and China with of 14.6 per cent and 9.8 per cent, respectively.“
Vietnam Global
Over-Reliance on Foreign Investment in Vietnam
For technology and capital, Vietnam relies heavily on Foreign Direct Investment (FDI). This can make them vulnerable to external economic shifts. Relying heavily on FDI for technology and capital can expose Vietnam to the risk of sudden withdrawal or reduction of investments by foreign companies. This can disrupt the country's economic stability and hinder its technological growth, as it becomes reliant on external sources for its development.
FDI continues to play a key role in driving Vietnam’s economic growth and development. Vietnam’s customs authority reported that so-called FDI companies exported $274 billion worth of goods in 2022, representing 74 percent of total goods exports. The government, at both central and municipal levels, actively seeks to attract FDI.
US Department of State: 2023 Investment Climate Statements: Vietnam
Manufacturing in Mexico is a Better Option
It is better, more cost-effective and strategically sound to relocate your manufacturing operations to a facility in Mexico for all the reasons outlined above. In contrast to the problems you experience with Asian operations, manufacturers using Mexico do not experience the same difficulties:
- Sourcing is easy and can be brought from the U.S. thanks to the USMCA. Like China, Vietnam does not have a trade agreement with the U.S.
- The Mexican workforce is educated and very skilled & plentiful.
- Shipping from Mexico, by air, land, sea or rail is cheaper than coming across the Pacific ocean.
FreightWays reports that prices for shipping continue to rise and don't appear to be slowing anytime soon.
“The index shows Asia-U.S. West Coast rates at $18,345, six times higher than a year ago, and the price for shipping to the U.S. East Coast quadrupled to $19,620 per forty-foot equivalent unit. Rates from Asia to Northern Europe climbed 4% since last week and are more than eight times higher than a year ago and 2.5 times more than at the start of the year. “
Besides the high rates, there is another issue: due to congestion in many American ports; many ships are unable to leave Asian ports, and those that do leave spend many weeks at sea before being delivered.
Conclusion
The analysis of the data in this report indicates that, despite the fact that manufacturing in Vietnam may offer some immediate benefits, it is more cost efficient to operate manufacturing operations in Mexico over the long run.
NovaLink has the process of getting started with manufacturing in Mexico down to a precise science. Whether you are a large corporation or a small business trying to get off the ground, NovaLink has the process, consulting for supply chain, software, facilities and manpower to get your business up and running quickly and efficiently with minimal cost.
FAQs: Vietnam's Manufacturing Challenges and Why Manufacturing in Mexico Might Be a Better Choice
- What are the similarities between Vietnam's manufacturing industry and China's in terms of challenges?
Both Vietnam and China face similar challenges in their manufacturing industries, including:
a) Rising labor costs: Both countries have experienced an increase in labor costs over the years, reducing the cost advantage they once enjoyed.
b) Supply chain complexity: As manufacturing operations become more globalized, managing complex supply chains involving multiple countries can pose challenges in terms of logistics, coordination, and quality control.
c) Intellectual property concerns: Protecting intellectual property rights can be a challenge in both Vietnam and China, although China has been historically associated with more significant IP infringement issues.
d) Environmental concerns: Both countries face environmental challenges, such as pollution and sustainability issues, which can impact manufacturing operations and compliance with environmental regulations.
- Why might manufacturing in Mexico be a better choice compared to Vietnam?
Manufacturing in Mexico offers several advantages over Vietnam, including:
a) Proximity to the United States: Mexico's geographical proximity to the United States provides logistical advantages, shorter lead times, and lower shipping costs, making it an attractive option for companies targeting the North American market.
b) Established supply chains: Mexico has well-established supply chains and strong integration with the North American Free Trade Agreement (NAFTA), providing a stable and reliable manufacturing ecosystem.
c) Skilled labor force: Mexico boasts a skilled labor force with expertise in various industries, including automotive, aerospace, electronics, and medical devices.
d) Intellectual property protection: Mexico has made significant strides in improving intellectual property protection, offering better legal frameworks and enforcement mechanisms compared to countries like China and Vietnam.
- How does Mexico's business environment compare to Vietnam's?
Mexico's business environment has several advantages over Vietnam, including:
a) Free trade agreements: Mexico has an extensive network of free trade agreements, including NAFTA (now USMCA), which provides preferential access to the United States, Canada, and other markets worldwide.
b) Stable political and economic climate: Mexico has a stable political environment and a robust economy, making it an attractive destination for foreign investment.
c) Infrastructure: Mexico has a well-developed infrastructure with modern transportation networks, reliable energy supply, and industrial parks that cater to manufacturing needs.
d) Cultural and language proximity: Mexico shares cultural and language similarities with the United States, facilitating business communication and collaboration.
- What are the benefits of manufacturing in Mexico for companies? Manufacturing in Mexico offers numerous benefits for companies, such as:
a) Cost advantages: Mexico provides cost advantages through competitive labor rates, reduced shipping costs, and minimized trade barriers through free trade agreements.
b) Access to markets: By manufacturing in Mexico, companies gain access to the large North American market, enabling them to serve customers efficiently and respond quickly to market demands.
c) Supply chain integration: Mexico's strong integration with global supply chains, especially in industries like automotive and electronics, allows companies to tap into an established ecosystem and collaborate with experienced suppliers.
d) Skilled labor force: Mexico has a large pool of skilled workers with expertise in various industries, ensuring companies can find the talent needed for their manufacturing operations.
- Is manufacturing in Mexico a long-term solution for companies? Manufacturing in Mexico can be a long-term solution for companies due to its strategic advantages, such as proximity to key markets, established supply chains, and a skilled labor force. Mexico's stable business environment and favorable trade agreements contribute to its attractiveness as a long-term manufacturing destination. However, companies should conduct thorough market research, consider industry-specific factors, and evaluate their unique needs to determine if Mexico aligns with their long-term manufacturing strategy.
Explore More: Discover Related Blog Posts
Expand your knowledge and delve deeper into more information found in our Manufacturing in Mexico Guide with our curated collection of related blog posts.
- Mexico’s Customs Clearance: Why It’s Faster—and Smarter—for Manufacturers
- Setup Process for Manufacturing in Mexico: What You Should Know About Timelines, Permits, and Common Pitfalls
- Cost of Manufacturing in Mexico: What You Need to Know to Budget Right
- The Mexico-U.S. Tariff Cheat Sheet Every Business Needs to Stay Competitive in 2025
- How Turnkey Manufacturing in Mexico Simplifies the Supply Chain
About NovaLink
As a manufacturer in Mexico, NovaLink employs a unique approach that transcends the traditional model of shelter production. More than just the location of your manufacturing, we would like to become a partner in your manufacturing in Mexico. You will be able to relocate or initiate manufacturing for your company in Mexico in a low-cost labor environment with very little delay or up-front costs. Find out how we can help you by handling the manufacturing process.
There are NovaLink facilities in the border cities of Brownsville, Texas, Matamoros, Mexico, and Saltillo, Mexico.