Last Updated on July 26, 2023
Traditionally, startups have outsourced their manufacturing operations to factories in Asia. However, with increasing offshore labor costs, product quality concerns, supply chain impacts, and rising tariffs, more and more companies are now shifting their manufacturing operations back to North America and Mexico. If you're considering starting a manufacturing operation in Mexico, it's essential to plan thoroughly and make well-informed decisions. In this guide, we will explore the best practices and considerations for successful startup manufacturing in Mexico.
Best Success Starts on Paper
The first and most crucial step in starting a manufacturing operation is thorough planning. Prior to starting the planning process for a manufacturing operation, it is imperative that you determine the scope of the entire operation. Without a clear plan, you are likely to fail.
Before you contact anyone about starting your manufacturing company, take the time to do your research and gather this information. Consider what other manufacturers on the market are doing and how they operate. In any case, you should at least consider the following:
- What Do You Want to Make: There will be different issues depending on the type of product you intend to make: if you plan on manufacturing outside the United States, you will need to understand how you intend to import it back into the United States. You will need to locate raw materials and equipment after you have determined what components you will need to manufacture your product. If you're manufacturing in Mexico, for example, the number of materials you import may affect the amount of import/export duties you have to pay. When you buy raw materials locally, you'll pay less duty later on your finished product.
Determining the materials you will need to make is done through the bill of materials. The bill of materials (BOM) is an extensive list of raw materials, components, and instructions for manufacturing your product.
- When Do You Want to Begin Manufacturing: Ensure all specifics are worked out before you arrive in Mexico to avoid delays in setting up your manufacturing company. Depending on your business size (if you do everything yourself), this could take months or even a year.
- Where Is Your Manufacturing Operation Going to Be Located: Location is key when it comes to manufacturing. You'll want to be near the US/Mexico border or a port of entry if you ship a lot into the U.S.
- Do You Want to Do It Yourself or Have a Partner: Foreign manufacturers can set up maquiladoras - or manufacturing facilities - in Mexico without having to go through all the paperwork. In Mexico, getting your manufacturing up and running yourself will be cheaper, but also more difficult and time-consuming. As you navigate the Mexican government's procedures and norms, going it alone will lead to a lot of mistakes. You'll want to find a manufacturing shelter partner in Mexico if you want things to move quickly.
A Maquiladora in Mexico is a factory or plant that is located near the Mexico/U.S. border. It is staffed by Mexican workers, but owned and operated by a U.S. company (although other countries, such as China, can also operate a Maquiladora). A Maquiladora allows manufacturers to operate duty-free and tariff-free.
Do a Manufacturing Cost Analysis
Profitability is key to a successful startup manufacturing venture. An in-depth manufacturing cost analysis helps determine that your project, partnered with a reputable nearshore manufacturing partner like NovaLink, is financially viable.
Manufacturing costs are divided into three categories: direct materials, direct labor, and manufacturing overhead. A simpler formula may be described as the following:

Even the most complex business projects can be simplified with cost analyses. A cost-benefit analysis puts all manufacturing projects into easy terms: benefits minus costs equal profits.
A helpful way to figure out manufacturing costs is to research your materials. If you want to make your own product, you'll need to know how many components you'll need.
Your product design may look amazing in drawings, but it has to be manufactured with real materials. What if the type of plastic you were initially going for gets dirty easily or loses its matte coating? You won’t know that unless you test dozens of materials.
G2 Learning
The Difference Between Production and Manufacturing Costs
Remember that production and manufacturing costs differ when analyzing costs. A company's production costs are all the expenses involved in doing business, but manufacturing costs are only the expenses involved in making the product. To figure out how much it costs to run a manufacturing business, you'll need both numbers.
A business's production costs can include both fixed and variable costs. This may include:
- Cost of a facility
- Advertising
- Equipment
Production volume affects manufacturing costs more. Materials, labor, and overhead all go into manufacturing costs. These expenses are all direct costs: For example, information technology workers' salaries and equipment are not direct costs, but factory workers' salaries and supplies are.
Knowing all your manufacturing and production costs will help you get financing for your manufacturing operation if you haven't already.
Product Specs & Prototypes: How to Make Your Idea Happen
Writing Product Specs
Writing detailed product specifications is essential before meeting with manufacturing partners in Mexico. A product specification describes exactly what the product will look like, what it will do, and what it will be.
Product management teams can also use these guidelines to optimize the product's features with information about the target audience. Any member of the product development team can use product specs to find out everything they need to know about a product.
A good product specification should include the following:
- Summary: An overview the product and your plan for production
- Business Case: How does this benefit the business or customer?
- User Personas: Who's this product for?
- User Stories: How does the user want to use your product?
- Designs: What does the product look like?
- Functional Specifications: Can you tell me about the product's technical details?
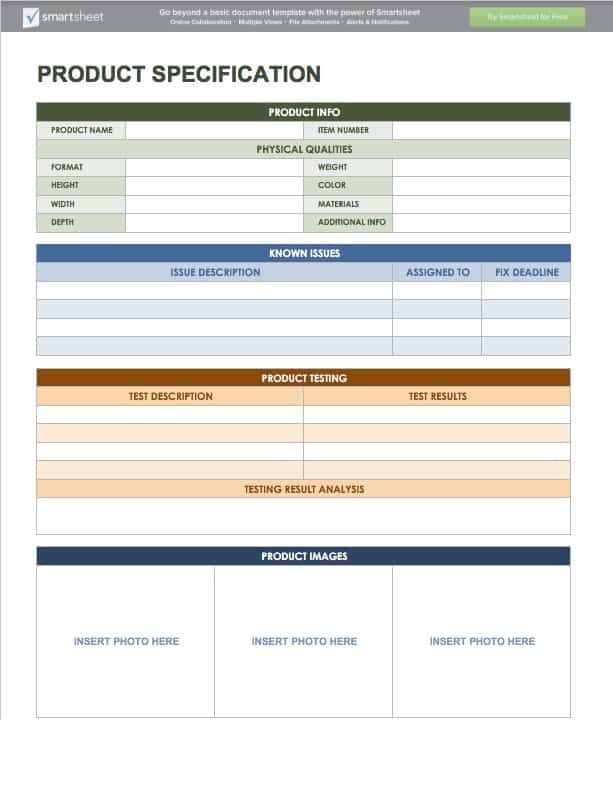
Source: 6 Steps To Write Product Specifications (+ Examples)
Make sure the product specifications are specific. In the early stages of product development, startups underestimate how complicated mass production can be. Manufacturers feel startups don't know what they want. Manufacturers will follow your specs exactly as you've given them. It’s your job to ensure all the details are 100% accurate.
If there is an obvious thing that common sense would tell you to change, if you do not explicitly tell them what to do, they will not do it," said Sterling of her experience. The only way to deal with this, Sterling and Uhrman agreed, is to spend a lot of time physically at the production site, especially during the early runs.
Julie Uhrman, Inc magazine

Source: Koobe Global: Choosing a manufacturing service model: What every startup should know
Making the Prototype
Once you have your very specific product specs, it's recommended you make a prototype of your product. Prototypes are examples of what you're going to make on a larger scale. Developing a prototype is highly recommended, as it provides a physical representation of your product and helps identify potential improvements or cost-saving measures. There are many benefits to this approach:
- You'll see if there are parts or steps to your product you didn't consider. It might also reveal steps in your specs you don't need.
- This will give you a good idea of what your finished product will look like. It'll help your manufacturing partner understand what you're doing. You can grasp the prototype design better when you have a physical product in hand than if it's just a theoretical idea.
- Prototypes will help you figure out what components you'll need, how much they cost, and how much manufacturing it will cost (approximately). This will help you figure out your cost per unit.
You may have to have several prototypes made before you find the right one for your manufacturing production.
On average I would expect to need at least 3 prototype iterations. This is true for both the product’s enclosure and the electronics. More advanced products may require as many as a dozen prototype iterations in order to get everything just right.
John Teele
There are hundreds of design firms that can help you get a prototype made. However, before you make the step of getting a prototype made, you need to understand intellectual property laws to make sure your rights are protected.

Source: SoFeast: How Many Prototypes Are Needed Before We Get ‘Perfection?’
Labor Laws and Protecting Your Rights
You should know the manufacturing and intellectual property laws in the country where you want to manufacture. This is whether it's in the US, Mexico, or overseas in China. You might doom your startup manufacturing operation if you don't know how to navigate the laws of the country you're working in or protect yourself from having your idea stolen.
The process of setting up a manufacturing plant in a foreign country like Mexico can be complicated. Getting to know Mexican regulations and laws, as well as U.S. laws and customs, will save you time and frustration.
Labor Law in Mexico
Labor law in Mexico establishes the relationship between employee and employer. An employment contract reaffirms this. The company you choose to work with, such as NovaLink, will set the terms of employment in this contract. The length of the workday, rest days, salary, and vacations, among others, need to be considered.

Source: Oyster: History of labor and employment laws in Mexico
IMMEX & USMC
Familiarize yourself with the IMMEX and USMCA programs, as they can offer cost-saving benefits and streamline your manufacturing process in Mexico. There are many reasons why USMCA is so beneficial, but the most significant one is that you'll save money. Some examples include lower tariffs between nations, encouraging investment in industrial buildings in North America, and opening up international markets.
IMMEX ("Manufacturing, Maquila, and Export Services Industries Program," also called "Maquiladora" in Spanish) helps companies save on labor costs. Companies that use the IMMEX program save money on operations they wouldn't if they used other manufacturing options, like China. With IMMEX, manufacturers can export supplies and equipment duty-free to Mexico, manufacture or assemble them, and then re-ship them to the US. American manufacturers can also access a large and skilled labor pool through the IMMEX program.
Protecting Innovation With Mexico's Intellectual Property Laws
Incentives for innovation, development, and protection of foreign companies' IP have been built into Mexican law for decades. Mexico is one of the top 10 Latin American and Caribbean economies for IP protection.
Trade in the region was boosted by the United States-Mexico-Canada Agreement (USMCA). As of July 1, 2020, the USMCA replaces NAFTA with 21st-century legal protections. USMCA also includes provisions to strengthen Mexico's IP policy framework in addition to recognizing the benefits of effective IP protection.
Working with a Shelter Partner
Do you plan to manufacture your products in-house or outsource them to a vendor for your startup manufacturing operation? It is not as simple as it may appear to make the decision. Your end product's cost, quality, and delivery date are affected by a number of factors.Here are some things to consider when determining whether to manufacture in-house or outsource:
- The cost of working with a shelter manufacturer might be higher, but there is no doubt they will be able to assist you in cutting through the red tape and getting your production operating more quickly. For example, if you choose to manufacture in Mexico with a shelter partner, Customs Trade Partnership Against Terrorism (CTPAT) and IMMEX certifications can take a while. If you work with a shelter manufacturer who's already CTPAT and IMMEX compliant, you won't have to worry about getting those certifications.
- What are the manufacturing costs, including labor and overhead? Will you need to invest in equipment or hire new employees? Are there any additional costs associated with outsourcing, such as shipping charges and customs clearance fees? Working with a shelter manufacturing partner can get all of these problems solved easily and quickly.
- Delivery date: If you’re in a hurry to get your product made and out to the market, outsourcing may be the better option.
- If your knowledge of complex manufacturing is lacking, outsourcing to a shelter manufacturing partner can save you time and money overall.
Of course, the manufacturing solution and country that makes the best sense for your company will depend on many factors, not least among them your size and experience and ability to “go it alone”. But for many companies looking at Mexico as a solution to tariff costs/shipping costs/geopolitical risks/quality issues/intellectual property theft problems, Mexico’s shelter manufacturing model offers a relatively fast, reliable, low-risk way to rearrange your supply chain in uncertain times.”
Harris Bricken Blog
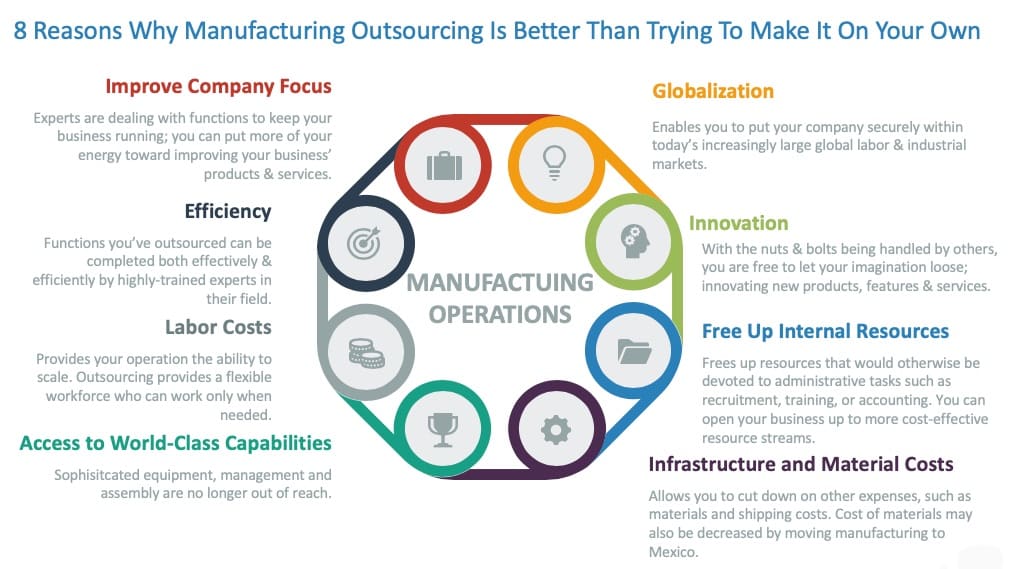
Conclusion: Startup Manufacturing Is a Learning Experience
Overall, the startup manufacturing process can be thought of as a learning experience, one that you or someone in your organization will likely be taking part in. The most critical thing is to take your time, consult with or partner with the right people, and integrate everything you learn as you progress towards developing a facility with the right capabilities, resources and talent in place to ensure that your product is built as efficiently and cost-effectively as possible.
FAQs for Startup Manufacturing
1. What are the key considerations for startups looking to begin manufacturing operations in Mexico?
Startups should consider factors like the type of product they want to manufacture, how they plan to import it into the United States, the location of their manufacturing facility, and whether they want to work with a partner or set up the operation themselves.
2. How can I conduct a thorough manufacturing cost analysis to ensure the financial viability of my project?
To conduct a comprehensive cost analysis, consider direct materials, direct labor, and manufacturing overhead. Research material costs, production volumes, and any fixed or variable expenses involved in the manufacturing process.
3. Why is it important to create detailed product specifications and develop prototypes before starting manufacturing in Mexico?
Product specifications provide clear guidance for manufacturing partners and ensure that startups get exactly what they want. Prototypes help identify potential design improvements and allow for a better understanding of the final product.
4. What are the labor laws in Mexico, and how can I protect my intellectual property rights while operating there?
Mexican labor laws establish the employer-employee relationship, and a comprehensive employment contract is essential. To protect intellectual property, startups can take advantage of Mexico's strong IP protection laws and understand the provisions under the USMCA.
5. Should I consider working with a shelter manufacturing partner, and how can they assist in navigating the complexities of setting up a manufacturing facility in Mexico?
Working with a shelter manufacturing partner can be beneficial as they are already familiar with the Mexican regulations and can help expedite processes like obtaining certifications. They also provide a low-risk option for rearranging the supply chain in uncertain times. Startup manufacturing is made simpler with a manufacturing partner.
About NovaLink
As a manufacturer in Mexico, NovaLink employs a unique approach that transcends the traditional model of shelter production. More than just the location of your manufacturing, we would like to become a partner in your manufacturing in Mexico. You will be able to relocate or initiate manufacturing for your company in Mexico in a low-cost labor environment with very little delay or up-front costs. Find out how we can help you by handling the manufacturing process.
There are NovaLink facilities in the border cities of Brownsville, Texas, Matamoros, Mexico, and Saltillo, Mexico.