Last Updated on February 19, 2025
Welcome to a comprehensive exploration of the often-confused terms Manufacturing Costs and Production Costs. In business and industry, these two concepts play a pivotal role in determining a company's financial health and efficiency. Although they may seem interchangeable at first glance, understanding their distinct meanings and implications can make a significant difference in optimizing operations, maximizing profits, and making informed decisions. Let's dive in!
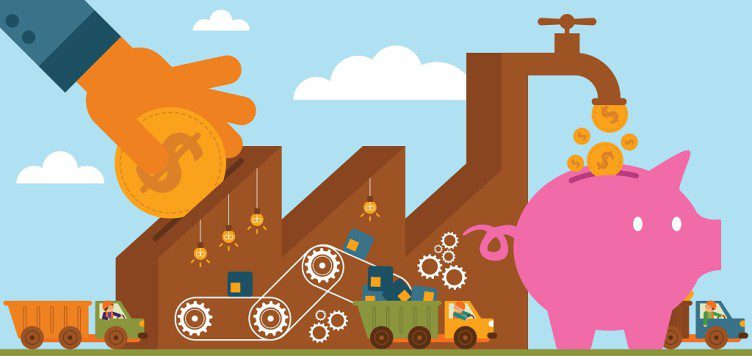
Understanding Manufacturing Costs
Manufacturing costs refer to the expenses incurred during the transformation of raw materials into finished goods. These costs are directly tied to the production process and can be categorized into three main components: direct materials, direct labor, and manufacturing overhead.
Production costs reflect all of the expenses associated with a company conducting its business while manufacturing costs represent only the expenses necessary to make the product.
Investopedia
Direct Materials
Direct materials encompass tangible inputs incorporated into the final product. This includes everything from raw materials like wood, metal, or plastic to smaller components like screws or wires. To calculate direct material costs, it is necessary to keep track of the quantities used and their individual prices.
Direct Labor
Direct labor pertains to wages or salaries paid to workers directly involved in manufacturing. These individuals are directly responsible for transforming raw materials into the finished product, and their wages are considered a direct cost of production.
Manufacturing Overhead
Manufacturing overhead accounts for all indirect costs incurred during production. These costs include factory utilities, equipment maintenance, factory rent, and other indirect labor costs. Calculating manufacturing overhead requires a comprehensive analysis of various expenses that support the production process but do not directly link to specific units of output.
For example, overhead costs in aviation maintenance, repair, and overhaul (MRO) companies encompass all indirect expenses that are not directly tied to the maintenance or repair of aircraft. These costs include items like rent, utilities, insurance, and administrative expenses. Based on the findings from the Oliver Wyman MRO Survey, it is noted that overhead costs typically make up about 20-30% of the total maintenance costs for commercial airlines.
How Do Changes in Production Volume Affect Manufacturing Costs?
As production volume rises, manufacturing costs follow suit. This means that, generally, the total manufacturing costs increase when the number of goods produced increases. This sensitivity to production changes is largely due to fixed and variable costs.
Variable Costs
- Materials and Labor: As more units are produced, more raw materials and labor are required. This leads directly to cost increases.
- Utilities and Maintenance: Higher production levels often result in increased energy consumption and more wear and tear on machinery, resulting in additional spending.
Fixed Costs
- Economies of Scale: While fixed costs such as rent or salaried staff do not fluctuate with production volume, the cost per unit can decrease with an increase in production. This is due to economies of scale, where spreading fixed costs over a larger number of units reduces the cost per item.
In summary, higher production volumes typically lead to increased total manufacturing costs, driven by variable expenses rise. However, the cost incurred per unit can decrease due to fixed costs being distributed over more units, optimizing overall efficiency.
Identifying and Understanding Production Costs
Production costs, on the other hand, are a broad term that encompasses all expenses incurred during the entire production cycle. This includes the initial raw material acquisition to the final product's delivery. While manufacturing costs are part of production costs, they include additional elements like transportation, packaging, and distribution expenses.
Production costs are variable costs that fluctuate directly proportionally to production activity. As production scales up or down, costs adjust accordingly.
Understanding the Role of Production Costs
To evaluate the total expenses of a manufacturing business, it's crucial to understand the impact of production costs. These costs are essential in determining the business's overall financial health. The revenue generated must exceed these total expenses for the company to achieve profitability. By calculating production costs accurately, businesses can assess whether they are operating efficiently and profitably.
Understanding Variable Costs
Businesses must monitor variable costs because they are directly tied to output levels. When production increases, expenses rise; when it decreases, they fall. Adaptability is crucial for the management of production budgets. By keeping a close watch on these costs, businesses can make informed decisions about scaling production and optimizing their expenses.
Common Examples of Variable Costs
- Materials and Supplies: These are the raw materials and components needed for production, and their cost varies with output volume.
- Labor Costs: Particularly with hourly wages or overtime, these costs change as the workforce is adjusted to meet production demands.
- Utilities: Energy consumption often aligns with production levels, influencing costs.
- Shipping and Distribution: Costs associated with delivering finished products can vary depending on the quantity produced and sent out.
Why Variable Costs Matter
Understanding and controlling variable costs can significantly impact profitability. Businesses that effectively manage these expenses can adapt faster to market changes and demand fluctuations, optimizing operations and profitability.
Incorporating Other Costs in Production Costs
Besides manufacturing costs, production costs may also involve administrative costs, marketing costs, and research and development expenses. These are essential components of the overall cost structure, as they contribute to the creation and delivery of the final product.
To fully understand production costs components, it's imperative to distinguish between fixed and variable costs.
Fixed Costs
These are expenses that remain constant regardless of production volume. They include:
- Building Rent: The cost of leasing facilities where production occurs.
- Advertising Budget: Funds allocated for product promotion.
- Business Equipment: The purchase or lease of machinery and tools necessary for production.
- Miscellaneous Expenses: Other costs that stay the same, such as insurance and salaries for permanent staff.
Variable Costs
These costs fluctuate with production volume changes:
- Supplies: Materials needed for creating the product that vary with output level.
- Wages: Payments to workers that may increase with overtime or additional shifts.
- Other Expenses: Any costs that change based on production scale, like utility bills.
By considering both fixed and variable costs, along with administrative, marketing, and research expenses, you gain a comprehensive view of the financial requirements necessary for producing and delivering a product. This understanding helps businesses strategize and optimize their operations efficiently.
Different Costing Methods
Manufacturing and production costs can be calculated using various costing methods. The most common methods are job costing, process costing, and activity-based costing (ABC). Companies may choose a specific costing method based on the complexity of their manufacturing processes and the level of accuracy required for cost allocation.
How Does the Rate of Production Affect Per-Item Cost and Profitability?
When a company ramps up its production levels, a chain reaction occurs that can greatly influence profitability. At the heart of this process is a crucial economic principle: the more you produce, the more you can lower the cost of making each item.
Breakdown of Per-Item Costs:
- Stable Fixed Costs: No matter how much you produce, certain expenses, like rent or salaries, don't change. These costs remain constant.
- Variable Costs: These are costs that vary with production volume, such as raw materials. While they increase with more production, they are offset by reduced fixed costs per item.
As production scales up, these stable fixed costs spread out over a larger number of items, causing the cost associated with each individual product to drop.
Impact on Profitability:
- Lower Manufacturing Costs: A decrease in per-item costs means that the business can sell products at competitive prices while maintaining a healthy margin of profit.
- Increased Profit Margins: By optimizing production to its fullest capacity, businesses can boost their profit margins after all expenses are factored in. This makes the operation not just profitable but more competitive in the market.
Manufacturing businesses determine the cost of production for each item by breaking down various expenses associated with its creation. This involves tallying all direct and indirect costs, such as materials, labor, and overheads.
- Direct Costs: These are straightforward expenses that directly relate to the production. This includes raw materials and the wages of workers actively involved in creating the product.
- Indirect Costs: These consist of expenses that don't directly tie to a single item but support the production process. Overheads like utility bills for running machinery, administrative salaries, and factory maintenance are typical examples.
- Fixed and Variable Costs: Fixed costs remain constant regardless of production volume, like rent and salaries. Variable costs fluctuate based on the number of items produced, such as costs for materials and energy.
Once these elements are examined, businesses calculate the total cost per unit by dividing the aggregate costs by the total number of units produced. Understanding these cost structures is crucial as it sets the foundation for establishing wholesale prices and ensuring profitability.
Thus, by raising production, a company can decrease the average cost of each product and enhance overall profitability. This strategic move often motivates businesses to push production to its limits, maximizing efficiency and returns.
What Are the Components of Production Costs in a Business?
Understanding production costs is crucial to business success. These costs are generally categorized into two main types: fixed and variable costs.
Fixed Costs
Fixed costs refer to expenses that remain constant regardless of production volume. These costs are predictable and do not fluctuate with business activity, making budgeting easier. Key examples of fixed costs include:
- Building Rent: Regular payments are required for leasing office or factory space.
- Advertising Budget: Consistent allocations for marketing and promotional activities.
- Business Equipment: Investments in tools and machinery necessary for operation.
- Miscellaneous Expenses: Other costs that remain stable and do not vary with production levels.
Variable Costs
Unlike fixed costs, variable costs fluctuate with production levels. As output increases or decreases, expenses adjust accordingly. The following variable costs include:
- Supplies: Materials needed for creating products that vary with production demands.
- Wages: Labor costs that change based on hours worked or units produced.
- Additional Expenses: Any other financial outlays that scale up or down with production activity.
By effectively managing both fixed and variable costs, businesses can optimize operations and improve profitability.
What are fixed costs in production costs?
Production costs are fixed costs that remain constant regardless of production or sales volume. These costs do not fluctuate with business activity and must be paid regardless of how much a company produces or sells. Here's a breakdown of typical fixed costs:
- Facility Lease or Mortgage: Payments for the space where business operations occur, whether it's a factory, office, or retail location.
- Marketing and Promotion: Allocates funds for advertising, promotions, and other marketing efforts planned over a set period.
- Business Equipment: Costs associated with machinery, computers, and other essential tools of the trade, which remain stable over time.
- Miscellaneous Operating Costs: Other regular outflows, such as salaries for permanent staff or insurance premiums, that are not influenced by production output changes.
Understanding fixed costs is crucial for businesses to manage budgets effectively and ensure profitability.
How can a business determine the break-even point in production?
To determine the break-even point in production, a business must first analyze its fixed and variable costs. Fixed costs remain constant regardless of output, while variable costs fluctuate with production levels. Here's a step-by-step guide to understanding the break-even point:
- Calculate Total Fixed Costs: Add up all expenses that do not change with production, such as rent, salaries, and insurance.
- Determine Variable Costs Per Unit: Identify how much it costs to produce one unit, considering materials, labor, and any other costs directly tied to production.
- Determine Selling Price Per Unit: Establish how much each product is sold for.
- Use the Break-Even Formula: [ \text{Break-even Point} = \frac{\text{Total Fixed Costs}}{\text{Selling Price per Unit} - \text{Variable Cost per Unit}} ]
Once the figures are plugged into the formula, the break-even point reveals the number of units to cover all costs. Producing and selling more than this amount will increase profitability.
Understanding this calculation helps businesses strategize pricing, cost management, and production efficiency. This ensures they can move beyond covering costs and into generating profit.
Key Differences and Essential Takeaways of Manufacturing Costs and Production Costs
To effectively manage business expenses, it's crucial to understand the nuances and overarching principles of both manufacturing costs and production costs. Let's delve into the essential takeaways and key distinctions between these two critical components of business finance:
Key Takeaways
- Production Costs: These encompass the total expenses of doing business, covering every aspect from inception to delivery.
- Manufacturing Costs: Specifically tied to the expenses directly involved in creating the product, such as raw materials and labor.
- Interconnection: Both production and manufacturing costs must be included in the calculation of the per-item cost, ensuring comprehensive financial planning.
Manufacturing and Production Costs: Differences and Similarities
Now that we have examined the individual components of manufacturing costs and production costs, let's highlight the main differences between the two:
Scope of Expenses
The primary distinction lies in their scope. Manufacturing costs strictly pertain to production expenses, while production costs encompass all costs from inception to final delivery.
Inclusion of Non-Manufacturing Costs
Production costs include manufacturing costs but also administrative, marketing, and distribution costs.
Calculation
Manufacturing costs are calculated by summing up direct materials, direct labor, and manufacturing overhead. In contrast, production costs involve a more extensive calculation considering the entire production cycle's expenses.
Decision-Making Impact
Understanding the difference between manufacturing and production costs is crucial for making informed decisions. By analyzing these costs separately, companies can pinpoint areas of inefficiency and make cost-saving adjustments.
Why Businesses Expand Production to Maximum Capacity
Businesses are driven by various factors to increase production levels to full capacity. A primary motivator is the potential to lower the average cost per unit. By spreading fixed costs over more items, companies can achieve increased efficiency and profitability.
Financial Incentives
- Direct Link with Fixed Costs: As production increases, fixed costs remain unchanged. This directly impacts the per-item manufacturing cost, which falls as production rises. This direct relationship is crucial because it highlights how stable fixed costs can lead to increased profitability when spread over a larger number of units.
- Profitability Emphasis: A lower per-item cost makes the business more profitable, Their article succinctly illustrates why businesses are motivated to expand production to full capacity. The focus on profitability provides a strong economic incentive for expansion.
- Motivation for Expansion: Lower per-item fixed costs motivate businesses to expand production up to their total capacity. This clear connection ties the concept of fixed costs directly to the strategic decision to expand production, illustrating how businesses use stable fixed costs as a lever to enhance profitability.
Competitive Advantage
Producing at full capacity can also deter new entrants from entering the market. Companies with larger production outputs can set price points that challenge smaller or newer businesses to compete at.
Resource Optimization
Operating at maximum capacity allows businesses to make optimal use of their machinery, workforce, and facilities. This maximizes output and justifies the investment in expensive equipment and other fixed assets.
Expanding production to full capacity is a strategic move that helps businesses stay competitive and financially robust in a demanding marketplace.
Understanding Production vs. Manufacturing Costs: A Practical Example
Let's explore how a small company that fabricates gadgets calculates its production and manufacturing costs.
Setting the Scene
Imagine this company faces fixed expenses such as $800 for factory space and $100 for the upkeep of their machinery. These costs remain constant, no matter how much they produce. As production rises, the cost attributed to each gadget decreases, spreading these fixed expenses across more units.
Breaking Down the Costs
- Fixed costs: $900 per month for rent and maintenance.
- Variable Costs: These are directly tied to each gadget made. Every unit requires $10 for supplies.
- Selling Price: Each gadget retails for $100.
To determine the total production cost per month, combine fixed and variable costs. For instance, producing one gadget costs $900 (fixed) + $10 (variable) per gadget.
Profit Calculations
After deducting the $10 manufacturing cost from the selling price, the company makes $90 per gadget. To break even, they need to sell enough gadgets to cover $900 in fixed costs. Here, that equates to producing and selling 10 gadgets monthly.
Achieving Profitability
To generate profit, production must exceed this break-even point. Selling more than 10 gadgets moves the company into profitable territory, as each additional sale contributes to covering previously fixed expenses and generating profit.
This example highlights how understanding both production and manufacturing costs is key to a small business surviving but thriving in a competitive market.
Having a Solid Business Case
According to Enrique Reynoso, the Chief Financial Officer for NovaLink, avoiding the problem of not having enough finances to cover your manufacturing & production costs is done through having a solid business case.
“I think it is very important that before talking about funding needs, you should have a thorough plan for the project as supported by a solid business case. Within the business case will be the funding plan, so the business case is the most important thing for justifying the project.
Enrique Reynoso
The purpose of a well-written business case is to clearly outline the investment rationale, including the financial, operational, and market/end customer justifications.
From a cost perspective, the business case will lay the foundation for the project and determine whether it is economically viable. In terms of the financial aspect, you can divide it into the following categories:
- In the first instance, how much investment will be required to begin the business? At the time of the initial startup, any capital investment required would be included in the costs.
- Second, there is the requirement for working capital. Materials are one component of working capital. Material purchases are required for production trials, startup inventory, and replenishment inventory.
- Third, initial startup and ongoing working capital required to maintain the operation: materials, operating expenses, and distribution costs. Potential customers will need to consider these items in their business case, which will then determine what funding requirements are necessary. As a result of preparing the business case, it may become apparent that the company does not necessarily have the funds to cover the startup costs and the necessary working capital.
Typically, the customer will want to retain a certain number of weeks of operating expenses to fund production until the operation has reached a steady state. The potential customer may not have that funding at the time, but the business case will help them determine what they need. As part of our business case inputs, NovaLink provides feedback to potential customers.
Conclusion: The Path to Informed Decision-Making
In conclusion, the difference between manufacturing costs and production costs lies in their scope, calculation, and impact on decision-making. As a subject matter expert, knowing these distinctions empowers businesses to optimize operations, minimize costs, and enhance profitability.
FAQs on The Difference Between Manufacturing Costs and Production Costs
Can manufacturing costs be higher than production costs?
A: Yes, it is possible if the production process is simple and streamlined, and the majority of expenses occur during manufacturing.
How does understanding manufacturing cost help in determining the selling price and profitability of the business?
A: Understanding manufacturing cost is crucial for a business as it allows for the determination of the selling price of the finished product. By considering all the expenses incurred in production, including direct costs like raw materials and labor, as well as indirect costs like rent and utilities, the business can calculate the total manufacturing cost. This cost, in turn, helps in setting an appropriate selling price that covers all expenses and ensures profitability for the business.
In a manufacturing setting, the ability to evaluate total expenses is paramount. A company must ensure that its revenue surpasses these expenses to achieve profitability. Businesses often calculate their expenses in terms of cost per item, which is critical for pricing strategies.
- Direct Costs: Raw materials and labor.
- Indirect Costs: Rent, utilities, and other overheads.
As production rates increase, revenue grows while fixed costs remain consistent. This scenario results in a lower per-item manufacturing cost, enhancing profitability. The concept of economies of scale is essential here—expanding production to full capacity can significantly increase profit margins.
By reducing per-item fixed costs, businesses are motivated to scale up production, which aligns with their goals of maximizing profitability after accounting for all variable costs.
Are production costs the same as total costs?
A: No, production costs cover expenses from raw materials to final delivery, while total costs include all expenses related to running a business.
What are the indirect costs included in manufacturing cost?
A: Indirect costs included in manufacturing cost are expenses such as rent, utilities, and administrative expenses. These costs are not directly tied to the production process but are necessary for the overall manufacturing operations.
How can businesses reduce manufacturing costs?
A: Businesses can reduce manufacturing costs by optimizing production processes, negotiating with suppliers for better prices, and investing in efficient machinery.
What is the significance of accurate costing methods?
A: Accurate costing methods help businesses determine product pricing, assess profitability, and make informed decisions on resource allocation.
Can production costs be lowered without compromising quality?
A: Yes, by implementing efficient supply chain management, reducing waste, and optimizing logistics, businesses can lower production costs while maintaining product quality.
About NovaLink
As a manufacturer in Mexico, NovaLink employs a unique approach that transcends the traditional model of shelter production. More than just the location of your manufacturing, we would like to become a partner in your manufacturing in Mexico. You will be able to relocate or initiate manufacturing for your company in Mexico in a low-cost labor environment with very little delay or up-front costs. Find out how we can help you by handling the manufacturing process.
There are NovaLink facilities in the border cities of Brownsville, Texas, Matamoros, Mexico, and Saltillo, Mexico.