Last Updated on February 26, 2024
In an assembly line in Mexico, workstations are arranged in a specific sequence to produce a product or service. At each station, pieces are added and coupled to build the original design until the product’s final assembly is obtained.
Assembly lines in Mexico assemble parts quickly and with less risk for maquiladora factory workers. An example of this prevalent in Mexico is automobile manufacturing, where the first step is installing the engine, the chassis, the roof, and the steering wheel assembly.
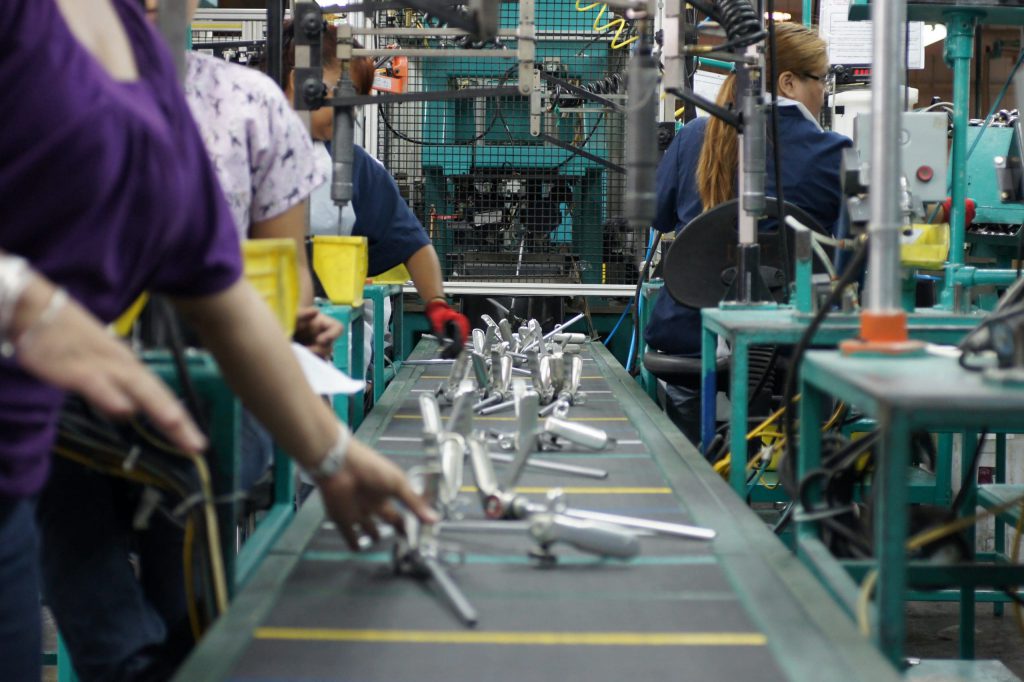
What Is an Automated Assembly Line?
In an automated assembly line, multiple workstations are linked by using a system for moving components and parts from one station to another based on complex algorithms for design, execution, control, and precision of work processes. As a result, a product is produced according to the specifications set forth.
13 Tips to Improve Assembly Lines in Mexico
Improving assembly lines in the country brings, as an immediate result, greater productivity with significant savings in time and reduction in production costs, in addition to guaranteeing high levels of quality and reliability.
Here are some tips for optimizing an assembly line in Mexico :
1. Define the Most Appropriate Assembly Line Design
Assembly lines in Mexico will be determined by the type of products to be produced. For example, if it will be in a continuous, flexible line or by workstations (cells).
In the case of products that are easy to handle and in small quantities, it is appropriate to use work cells, but if the products are heavy, then flexible lines are better.
The system’s design must be fluid and adequate for Mexican operators to guarantee the quality handling and treatment of each by-product.
Long distances to walk through assembly lines should be avoided. The product should go toward the operator rather than the other way around. The workstations must be ergonomic and have all the devices and/or accessories available to facilitate the work.
The objective is to comply with the established work times (flexible) so that product quality and compliance with safety regulations are guaranteed at all times.
2. Understand the Process
Before making any changes, it’s imperative to understand the assembly line process. Observe the operations and note any issues or areas to improve. Talk with the people working on the line and find out what they think. Gathering information from those closest to the process can help identify improvements.
3. Ensure a Balance of Production That Avoids Damage
On assembly lines in Mexico, previously prepared parts or elements are required that can be produced internally or acquired externally. These inputs must be stored or produced in the correct quantities to avoid excesses in inventories or, on the contrary, deficits that affect the production line and assembly of the products.
The balance of the process is essential. Everything must flow in a harmonious and synchronized way because, if it is not achieved, losses in production can be generated, and the system is no longer efficient. To achieve this awareness, technology tools must be incorporated for the logistic management of the process, such as the manufacturing execution system (MES), for maximum production efficiency and effectiveness.
4. Assess Current Efficiency
In the assembly line that is programmed, monitor the times used for each phase of the process once each month to determine if they are consistent or, on the contrary, if they need to be adjusted to maximize their efficiency without neglecting the exhaustion of human talent, quality, and safety.
Take a look at your production process from beginning to end to identify any bottlenecks and inefficiencies that could hamper your progress. Note how many items you can produce per shift and any problems that arise during production. Are there any tasks or processes that take too long or could be automated? Are there any areas where workers have to wait for machines or materials? Another critical step in assessing your current efficiency is tracking and analyzing your data.
Sometimes it happens that the machines need to be calibrated, or they deteriorate. The consequence of not doing this is slower movement on the assembly line.
5. Develop Goals for Improvement
Set measurable and achievable improvement goals. Make sure to establish timeframes for each goal and milestones to check progress. When setting goals, think about overall efficiency, quality control, cost reduction, and safety.
6. Create a Productive Environment
In a production chain in Mexico, where labor is of the essence, and a manufacturer wants to be productive while maintaining quality standards, it is essential to maintain a healthy organizational climate. Critical to doing this is establishing rest intervals with relaxing physical or mental activity.
An example of this might be providing a suitable dining room with music, a television, or other amenities that stimulate staff to increase production, quality, safety, order, and cleanliness.
For the purpose of establishing these policies, it is vital to train the personnel in security management and provide them with the supplies that the staff requires for the execution of their duties.
7. Develop Goals for Improvement
Set measurable and achievable goals for improvement. Make sure to set timeframes for each goal and have milestones in place to check progress. When setting goals, think about overall efficiency, quality control, cost reduction, and safety.
8. Improve, Automate, and Standardize Processes
The efficiency and effectiveness of an assembly line in Mexico begins by respecting work procedures and safety protocols.
Human talent is the best tool to optimize processes. Still, operators will only be effective if they have good practices and pre-established mechanisms in terms of security and other areas.
9. Implement asynchronous Systems
In those production systems in Mexico based on workstations, where each has a different time for the execution of the activity, and the manufacturer wants the entire line to be synchronized, it is most likely that the time will be affected since each workstation has its own time.
The best way to work around this problem is to use asynchronous times since execution times can be variable.
In the station with the highest variable time, the next phase is entered when it ends or completes the critical cycle to start the next workstation.
However, the products downstream of this station can continue until the end of their production cycle.
In this sense, it is better to determine the flexible working times in each workstation.
10. Establish an Ergonomic Assembly Line
An essential point to consider in an assembly line in Mexico is that the work environment, tools, and activities match the workers' physiological, anatomical, and psychological characteristics so that they do their tasks effectively.
These seven critical criteria will greatly help manufacturers and encourage their intelligent optimization of assembly line operations in Mexico.
11. Streamline Assembly Station Tasks
Look for ways to reduce the number of steps required to complete each task. Consider using tools and equipment that can help workers complete tasks more quickly and efficiently.
12. Increase Productivity of Packing and Shipping Stations
Optimize the flow of materials through the packing and shipping stations to reduce waste and increase efficiency. Consider using automated systems to move materials and reduce the need for manual labor.
13. Invest in Employee Training
Provide your employees with the training they need to work efficiently and safely. Make sure they understand the assembly line process and how to use the tools and equipment effectively. Encourage them to share their ideas for improving the process.
FAQs on Assembly Line Efficiency
1. How can companies optimize assembly line operations in Mexico to enhance efficiency?
To optimize assembly line operations in Mexico, companies should focus on streamlining workflows, implementing lean manufacturing principles, and investing in technology to automate repetitive tasks. Additionally, fostering a culture of continuous improvement and providing regular training to workers can contribute to increased operational efficiency.
2. What role do cross-cultural considerations play in managing assembly lines in Mexico?
Cross-cultural considerations are crucial in managing assembly lines in Mexico. Understanding and respecting cultural nuances, communication styles, and work preferences can improve team collaboration and morale. Employing bilingual staff, conducting cross-cultural training, and promoting a diverse and inclusive workplace can help bridge cultural gaps and enhance overall productivity.
3. How can companies address logistical challenges when operating assembly lines in Mexico?
To tackle logistical challenges in Mexico, companies should develop robust supply chain strategies, establish strong relationships with local suppliers, and leverage advanced logistics technologies. Implementing just-in-time inventory practices and having contingency plans for potential disruptions, such as border issues or transportation delays, are essential for maintaining smooth assembly line operations.
4. What legal and regulatory considerations should companies be aware of when running assembly lines in Mexico?
Companies operating assembly lines in Mexico must navigate various legal and regulatory requirements. This includes compliance with labor laws, environmental regulations, and trade agreements. Working closely with legal advisors, staying updated on legislative changes, and ensuring proper documentation for imports and exports are vital to avoid legal complications and ensure a compliant operation.
5. How can environmental sustainability be incorporated into assembly line operations in Mexico?
To integrate environmental sustainability into assembly line operations in Mexico, companies can adopt eco-friendly practices, invest in energy-efficient technologies, and implement waste reduction initiatives. Collaborating with local environmental agencies, obtaining certifications for sustainable practices, and engaging with the community on environmental initiatives can enhance a company's reputation while contributing to a greener and more socially responsible operation.
About NovaLink
As a manufacturer in Mexico, NovaLink employs a unique approach that transcends the traditional model of shelter production. More than just the location of your manufacturing, we would like to become a partner in your manufacturing in Mexico. You will be able to relocate or initiate manufacturing for your company in Mexico in a low-cost labor environment with very little delay or up-front costs. Find out how we can help you by handling the manufacturing process.
There are NovaLink facilities in the border cities of Brownsville, Texas, Matamoros, Mexico, and Saltillo, Mexico.
Explore More: Discover Related Blog Posts
Expand your knowledge and delve deeper into more information about packaging solutions in Mexico with our curated collection of related blog posts.
- Smart Moves: Strategies for Manufacturing in Mexico That Actually Work
- How Kitting Services in Mexico Streamline Your Manufacturing Operations
- Streamlining Your Operations: How Kitting Services Can Help You Compete in Mexico
- Packaging Solutions in Mexico: Crafting Success in Every Box
- Assembly lines in Mexico: 13 Tips to Optimize Their Operations