Last Updated on June 13, 2024
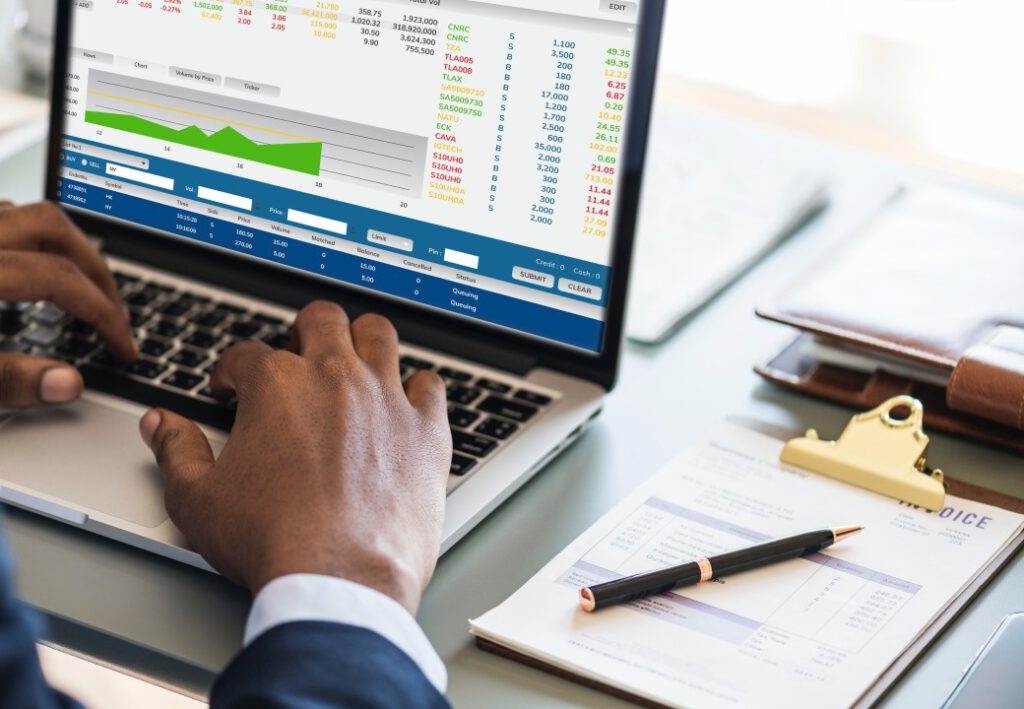
Manufacturing in Mexico presents a lucrative opportunity for companies looking to reduce operational costs while maintaining high-quality production. However, understanding the essential start-up costs for manufacturing in Mexico involved is crucial to a successful venture. Below, we outline the key expenses businesses must account for when setting up manufacturing operations in Mexico.
Facility Acquisition and Setup
Real Estate Costs
Securing an appropriate facility is one of the most important steps in manufacturing operations. This involves:
- Purchasing Land or Leasing Property: Costs vary significantly based on location, with major industrial hubs such as Monterrey, Guadalajara, and Mexico City generally commanding higher prices. Manufacturing cities in the northern part of the country near Texas, like Matamoros, are less expensive.
- Construction and Renovation: If constructing a new facility or renovating an existing one, expenses include materials, labor, and compliance with local building codes.
Utilities and Infrastructure
Setting up utilities is indeed crucial for manufacturing operational efficiency. Reliable and efficient utility services such as electricity, water, gas, and wastewater management are essential for the smooth operation of manufacturing processes.
Here are some reasons why setting up utilities is important for manufacturing operational efficiency:
- Reliable Power Supply: A stable electricity supply is critical for running machinery and equipment, ensuring consistent production and minimizing downtime.
- Water and Gas Supply: Access to clean water and gas is necessary for various manufacturing processes, such as cleaning, heating, and powering equipment.
- Wastewater Management: Proper wastewater management is essential for environmental compliance and preventing production disruptions.
- Cost Savings: Efficient utility setup can help reduce energy and water consumption, leading to cost savings and minimizing waste.
- Compliance: Ensuring utilities are set up correctly helps manufacturers comply with environmental and safety regulations.
NovaLink Nearshore Manufacturing can assist with setting up utilities and ensuring manufacturing operational efficiency. By outsourcing utility management to NovaLink, manufacturers can focus on their core operations while leveraging NovaLink's expertise in managing utility services.
Legal and Regulatory Compliance
Permits and Licenses
Start-up costs for manufacturing in Mexico involves acquiring various permits and licenses:
- Business Registration: Formal registration of the business with Mexican authorities.
- Environmental Permits: Compliance with environmental regulations to minimize ecological impact.
- Health and Safety Certifications: Ensuring the facility meets occupational health and safety standards.
Import and Export Regulations
For manufacturing companies importing raw materials or exporting finished products from Mexico:
- Customs Duties and Taxes: Understanding the costs associated with customs duties and value-added tax (VAT).
- Compliance with Trade Agreements: Leveraging trade agreements such as the USMCA to minimize tariffs and streamline cross-border trade.
Labor Costs
Recruitment and Training
Labor is one of the most significant start-up costs for manufacturing in Mexico:
- Hiring: Costs related to recruitment, including advertising vacancies and hiring services.
- Training Programs: Implementing comprehensive training programs to ensure the workforce is skilled and efficient.
- Benefits and Compensation: Labor laws in Mexico mandate certain benefits, such as social security, housing funds, and profit-sharing, which can add to labor costs.
- Compliance with Labor Regulations: Companies must comply with Mexico's labor laws, which can be complex and time-consuming, and may require legal or consulting fees.
- Staffing Levels: Manufacturing operations often require a significant workforce, which can drive up labor costs.
- Turnover and Retention: High employee turnover can lead to additional recruitment and training costs, while retention strategies, such as bonuses or incentives, can also add to labor expenses.
- Union Fees and Collective Bargaining: Depending on the location and industry, companies may need to negotiate with unions, which can impact labor costs.
Equipment and Machinery
Purchasing and Leasing
The cost of acquiring essential machinery and equipment for manufacturing in Mexico can be difficult if you try to do it on your own instead of working with a nearshore partner like NovaLink for the following reasons:
- Initial Purchase: Investing in state-of-the-art machinery to ensure high productivity and quality.
- Setup Costs: Manufacturers incur significant setup costs when preparing production lines, tooling, and equipment for manufacturing processes. With low volumes or short runs, setup costs are spread over a smaller number of units, leading to higher per-unit costs.
- Economies of scale: Economies of scale refer to cost advantages gained when production volume increases. Manufacturers can achieve lower per-unit costs by spreading fixed costs (such as machinery, labor, and overhead) across a larger number of units. In low-volume or short-run productions, economies of scale are not fully realized, resulting in higher production costs.
- Material Costs: Purchasing materials in small quantities can be more expensive per unit than bulk purchases. Suppliers often offer discounts for larger orders, which reduces material costs. In low-volume or short-run productions, manufacturers may not qualify for these discounts, leading to higher material expenses.
- Labor Efficiency: Efficient labor utilization is crucial for cost-effective production. In low-volume or short-run productions, the time spent on setup, changeovers, and coordination between production runs may outweigh the actual time spent on manufacturing. This inefficiency increases labor costs per unit.
- Waste and Scrap: Manufacturing processes often generate waste and scrap, which adds to production costs. In low-volume or short-run productions, the proportion of waste per unit produced may be higher than larger production runs. This results in increased per-unit costs due to waste disposal and material losses.
- Lack of Clarity: While having an idea for a product is a crucial starting point, it is essential to have a clear understanding of the product concept, design specifications, target market, and manufacturing requirements before engaging with a nearshore manufacturing company. Without a well-defined plan, the manufacturer may struggle to provide accurate guidance or support.
- Feasibility Assessment: Before manufacturing, it is essential to assess the feasibility of the product idea in terms of technical requirements, market demand, regulatory compliance, and production costs. Engaging with a nearshore manufacturing company prematurely without conducting feasibility studies may lead to unrealistic expectations or potential setbacks down the line.
Supply Chain and Logistics
Sourcing Raw Materials
Reliable and cost-effective sourcing of raw materials:
- Local Suppliers: Building relationships with local suppliers to reduce transportation costs and lead times.
- International Suppliers: Navigating import regulations and tariffs for materials not available locally.
Distribution Network
Establishing an efficient distribution network:
- Transportation Costs: Shipping finished products to domestic and international markets.
- Warehousing: Costs associated with storing raw materials and finished goods.
Summary of Key Costs
To successfully set up manufacturing operations in Mexico, businesses must thoroughly evaluate and budget for the following key areas:
- Facility Acquisition and Setup
- Legal and Regulatory Compliance
- Labor Costs
- Equipment and Machinery
- Supply Chain and Logistics
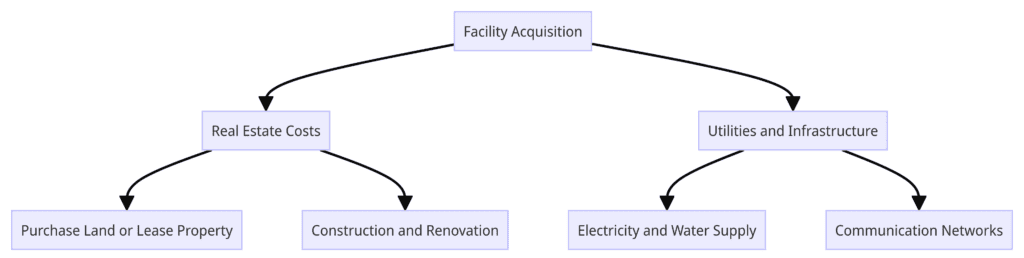
Properly planning and allocating resources for these start-up costs will facilitate a smooth and efficient entry into the Mexican manufacturing sector, positioning businesses for long-term success and profitability.
Moving Manufacturing to Mexico Can Save Time and Paperwork
Additionally, moving manufacturing to Mexico can save time and paperwork, which will ultimately result in significant cost savings. For these reasons, U.S. goods and services trade with Mexico totaled an estimated $577.3 billion in 2021.
Reduction in Legal Liability
A foreign investor doing business in Mexico through a Mexican subsidiary has traditionally been protected from liability for the debts and obligations of the Mexican subsidiary.
Knowledge of Mexico Business Practices
Manufacturing companies often make the mistake of assuming they know enough about Mexico to do it on their own. The majority of shelter manufacturers can assist you in cutting through the red tape in starting your manufacturing operation by providing analyses, site visits, classifications, permits, factory setup, and training. Also, Mexico's industrial capabilities make choosing a location for a manufacturing operation less difficult; most places in the country have some sort of industrial facility, although some locations are more suitable than others.
Quick Setup Model
There are many factors that influence this, such as equipment, training and sourcing materials. However, some companies who are interested in starting manufacturing in Mexico can do so within a month. Since many shelter manufacturing companies are incorporated in Mexico, and hold current maquiladora permits, there is no legal aspect to this process.
Protection of Intellectual Property
Intellectual property theft is a tremendous problem in China. The new USMCA agreement strengthens intellectual property rights even further in Mexico, with one of its main objectives to protect the Intellectual Property Rights of products between the United States, Mexico, and Canada. In accordance with the Office of the United States Trade Representative:
“The United States, Mexico, and Canada have reached an agreement on a modernized, high-standard Intellectual Property (IP) chapter that provides strong and effective protection and enforcement of IP rights critical to driving innovation, creating economic growth, and supporting American jobs.”
By enforcing these rights, it becomes very difficult, if not impossible, for companies manufacturing in Mexico to have their intellectual property rights stolen.
FAQ's on Start-up costs for manufacturing in Mexico
1. What are the main advantages of setting up manufacturing operations in Mexico?
The primary advantages of setting up manufacturing operations in Mexico include lower labor costs, proximity to the United States market, favorable trade agreements such as the USMCA, a skilled workforce, and a growing industrial infrastructure. These factors collectively make Mexico an attractive destination for manufacturing businesses looking to reduce costs while maintaining high production quality.
2. How do I obtain the necessary permits and licenses to operate a manufacturing facility in Mexico?
To operate a manufacturing facility in Mexico, you need to register your business with the appropriate Mexican authorities, obtain environmental permits, and ensure compliance with health and safety regulations. It is advisable to work with local legal experts or consulting firms who are familiar with the regulatory landscape to streamline the process and ensure full compliance.
3. What should I consider when choosing a location for my manufacturing facility in Mexico?
When choosing a location for your manufacturing facility, consider factors such as proximity to suppliers and customers, availability of skilled labor, local infrastructure, real estate costs, and the region's economic stability. Industrial hubs like Monterrey, Guadalajara, and Mexico City are popular choices due to their well-developed infrastructure and strategic locations.
4. What are the typical costs associated with setting up utilities in a new manufacturing facility in Mexico?
Setting up utilities in a new manufacturing facility involves costs for installing and connecting electricity and water supply, as well as establishing reliable communication networks. These costs can vary based on the facility's size and location. It is essential to budget for these expenses to ensure your operations run smoothly and efficiently from the start.
5. How can I effectively manage labor costs when starting a manufacturing operation in Mexico?
To effectively manage labor costs, focus on thorough recruitment processes to hire skilled workers, invest in comprehensive training programs, and offer competitive wages and benefits to attract and retain talent. Additionally, understanding and complying with Mexican labor laws regarding salaries, benefits, and working conditions will help manage labor costs and maintain a productive workforce.
About NovaLink
As a manufacturer in Mexico, NovaLink employs a unique approach that transcends the traditional model of shelter production. More than just the location of your manufacturing, we would like to become a partner in your manufacturing in Mexico. You will be able to relocate or initiate manufacturing for your company in Mexico in a low-cost labor environment with very little delay or up-front costs. Find out how we can help you by handling the manufacturing process.
There are NovaLink facilities in the border cities of Brownsville, Texas, Matamoros, Mexico, and Saltillo, Mexico.