Last Updated on November 12, 2024
Understanding the Key Differences Between Nearshoring, Offshoring, and Reshoring
Globalization has led to businesses adopting diverse manufacturing strategies to optimize costs, improve supply chain efficiencies, and meet consumer demand.
These goals can be achieved by choosing between nearshoring, offshoring, and reshoring. Taking a closer look at these shoring strategies and their benefits, challenges, and applications, let's examine their advantages and drawbacks.
What Is Nearshoring?
Nearshoring refers to the practice of moving business operations or manufacturing processes closer to a company's home country. For U.S.-based companies, nearshoring typically means relocating to neighboring countries such as Mexico or Canada.
Advantages of Nearshoring:
- Reduced Lead Times: With closer geographical proximity, shipping times are significantly reduced, improving supply chain responsiveness.
- Lower Labor Costs: Countries like Mexico offer competitive labor costs, often significantly lower than those in the U.S. or Canada.
- Cultural and Time Zone Alignment: Shared time zones and cultural similarities streamline communication and decision-making.
Challenges of Nearshoring:
Nearshoring presents several challenges, including cultural and language barriers, geographical limitations, and security and compliance risks. Differences in language, customs, and business practices can lead to misunderstandings, while data protection regulations and intellectual property laws may differ between countries. Time zone differences, even if relatively small, can also require adjustments for real-time communication and collaboration.
Other challenges include talent acquisition and retention, communication and collaboration, quality control, scalability, hidden costs, and governance and management. Competition for skilled professionals can be intense, and retaining talent can be difficult.
Organisations must have a long-term vision in mind. As nearshoring represents a significant change in how procurement teams source goods, they cannot afford to make decisions that only deliver immediate or short-term value – they need to consider how their supply chains will develop moving forwards. - Procurement Magazine
Offshoring: A Long-Established Global Strategy
Offshoring is the practice of relocating manufacturing or service functions to countries further away, often to regions like Asia. China, India, and Vietnam have long been major players in offshoring due to their low-cost labor and vast production capabilities.
Advantages of Offshoring:
- Cost Efficiency: Offshoring to countries with significantly lower labor costs can dramatically reduce production expenses.
- Skilled Labor Availability: Many offshore destinations have established industrial expertise and trained workforces in sectors like electronics, textiles, and technology.
- Scalability: Large production capabilities allow companies to scale operations rapidly offshore.
Challenges of Offshoring:
Offshoring can pose significant logistical and cultural challenges. For instance, longer lead times are a major concern, as the distance between production facilities and key markets can result in extended shipping times and increased vulnerability to supply chain disruptions. This can ripple throughout the production process.
Additionally, cultural and language barriers, as well as potential trade tensions, can further complicate offshoring operations. Different languages, business practices, and legal frameworks can hinder communication and collaboration. Moreover, the risk of tariffs, fueled by global trade tensions, can erode the cost advantages offshoring is intended to provide. This is particularly true between major trading partners like the U.S. and China.
Reshoring: Bringing Production Back Home
Reshoring is the strategy of bringing production or business operations back to the company's home country. For many U.S. businesses, reshoring has gained momentum due to concerns about supply chain resilience and national security.
Advantages of Reshoring:
- Supply Chain Control: Reshoring allows companies to closely monitor production, reducing disruption risk and ensuring product quality.
- Enhanced Flexibility: Being closer to the end market allows companies to respond quickly to changing consumer preferences and market dynamics.
- Brand Image and National Security: Reshoring initiatives often promote a "Made in America" ethos, appealing to consumers and fostering national security by reducing reliance on foreign suppliers.
Challenges of Reshoring:
Reshoring comes with significant challenges. One of the most substantial barriers is the high labor costs associated with hiring workers in developed countries like the U.S. These increased costs can offset the benefits of reshoring, making it difficult for companies to justify the move.
Additionally, reshoring often requires substantial capital investment. To make reshoring financially viable, companies may need to invest heavily in upgrading facilities, purchasing updated equipment, and implementing automation technologies. These upfront costs can be prohibitive, especially for smaller companies or those with limited resources. However, with careful planning and strategic investment, companies can overcome these challenges and reap the benefits of reshoring.
Key Considerations When Choosing Shoring Strategies
Selecting between shoring strategies such as nearshoring, offshoring, or reshoring requires a thorough analysis of several factors, including cost, lead time, supply chain complexity, and market conditions.
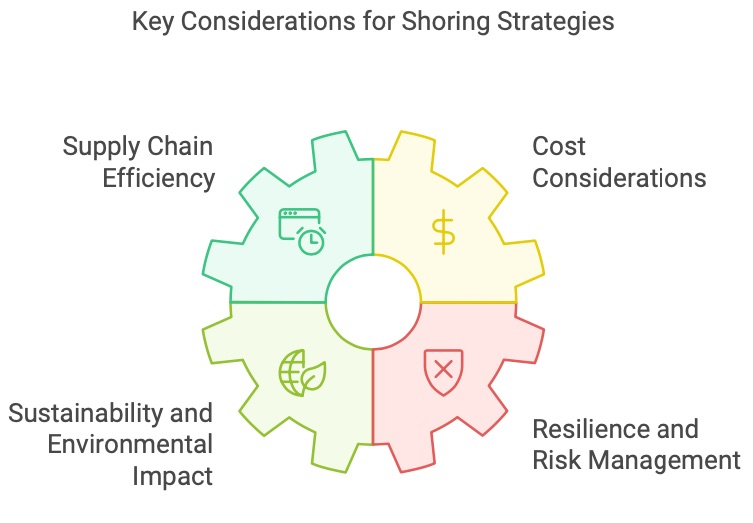
Supply Chain Efficiency
- Lead Time Reduction: Nearshoring reduces lead times due to geographical proximity, while offshoring typically involves longer shipping times.
- Inventory Management: Reshoring can improve supply chain control by reducing large buffer inventories, especially for businesses with just-in-time models.
Cost Considerations
- Labor Costs: Offshoring remains the most cost-effective option for labor-intensive industries, though rising wages in certain regions may shift this balance. Nearshoring offers competitive labor costs without the significant increase associated with reshoring.
- Tariffs and Trade Policies: Companies must stay aware of shifting tariffs, trade agreements, and regulatory environments, particularly when choosing offshoring destinations.
Sustainability and Environmental Impact
With increasing pressure from consumers and governments to adopt sustainable practices, the environmental impact of shoring strategies is crucial.
- Carbon Footprint: Nearshoring can reduce transportation's environmental impact due to shorter shipping distances.
- Energy Efficiency: Offshore production in regions with lax environmental regulations may generate higher emissions than reshoring operations, which often adhere to stricter sustainability standards.
Resilience and risk management
- Geopolitical Risks: Offshoring to politically unstable regions poses significant risks, including trade restrictions, regulatory changes, and civil unrest. Nearshoring and reshoring can mitigate some of these risks by keeping production within politically stable or familiar regions.
- Pandemic and Disruption Response: The COVID-19 pandemic exposed vulnerabilities in global supply chains. Nearshoring and reshoring emerged as viable solutions to improve resilience by reducing dependence on far-off suppliers.
Conducting a comprehensive total cost of ownership analysis is essential. This analysis involves evaluating labor costs and factors such as transportation costs, taxes, tariffs, inventory management, regulatory compliance, intellectual property protection, and any additional costs associated with reshoring or nearshoring. - Thomasnet
Conclusion: It Is Crucial to Choose the Right Shoring Strategy
Choosing the right shoring strategy is a critical decision for companies looking to optimize production costs, enhance supply chain efficiency, and manage risk. By carefully analyzing the benefits and challenges of nearshoring, offshoring, and reshoring, businesses can develop a tailored approach that meets their operational and strategic goals.horing, and reshoring, businesses can develop a tailored approach that meets their operational and strategic goals.
FAQ: Shoring Strategies
What are the key benefits of nearshoring compared to offshoring?
Nearshoring offers reduced lead times due to geographic proximity, competitive labor costs, and cultural alignment. In contrast, offshoring often involves longer shipping times but may provide even lower labor costs and access to large-scale production capabilities.
How do reshoring and nearshoring help improve supply chain resilience?
Both reshoring and nearshoring bring production closer to home markets, reducing the reliance on distant suppliers and minimizing the risks associated with global disruptions, such as political instability or pandemics. This proximity allows businesses to quickly adapt to changes in demand and market conditions.
Which industries benefit most from offshoring?
Labor-intensive industries, such as textiles, electronics, and technology, benefit significantly from offshoring due to lower labor costs and established production expertise in offshore locations like China, India, and Vietnam.
How does automation influence the decision between reshoring and offshoring?
Automation reduces labor dependency, making reshoring more attractive by offsetting higher labor costs in developed countries. It enables companies to achieve cost-efficiency through technological advancements rather than relying solely on cheaper offshore labor.
What are the environmental considerations when choosing shoring strategies?
Nearshoring typically reduces the carbon footprint associated with long-distance transportation, while reshoring often adheres to stricter environmental regulations. Offshoring to countries with less stringent environmental laws may lead to higher emissions and less sustainable practices.
Explore More: Discover Related Blog Posts
Expand your knowledge and delve deeper into more information about Nearshoring Manufacturing to Mexico with our curated collection of related blog posts.
- Mexico’s Customs Clearance: Why It’s Faster—and Smarter—for Manufacturers
- Setup Process for Manufacturing in Mexico: What You Should Know About Timelines, Permits, and Common Pitfalls
- Cost of Manufacturing in Mexico: What You Need to Know to Budget Right
- Smart Moves: Strategies for Manufacturing in Mexico That Actually Work
- Why “Plan Mexico” Might Be the Wake-Up Call Manufacturers Didn’t Know They Needed
About NovaLink
As a manufacturer in Mexico, NovaLink employs a unique approach that transcends the traditional model of shelter production. More than just the location of your manufacturing, we would like to become a partner in your manufacturing in Mexico. You will be able to relocate or initiate manufacturing for your company in Mexico in a low-cost labor environment with very little delay or up-front costs. Find out how we can help you by handling the manufacturing process.
There are NovaLink facilities in the border cities of Brownsville, Texas, Matamoros, Mexico, and Saltillo, Mexico.