Last Updated on October 5, 2023
In the world of manufacturing, understanding your costs is paramount to success. Whether you're producing automobiles, consumer electronics, or food products, knowing where every dollar is spent can make or break your business. This is where manufacturing cost analysis comes into play. In this blog post, we will explore what manufacturing cost analysis is, why it is important, how to perform it, and the tools and best practices associated with it.
What Is a Manufacturing Cost Analysis?
Manufacturing Cost Analysis, often referred to as cost accounting or cost analysis, is a systematic process used by businesses to assess and understand the various expenses associated with the production of goods. This analysis aims to break down and evaluate all the costs involved in manufacturing a product, from the acquisition of raw materials to the delivery of the final product to customers.
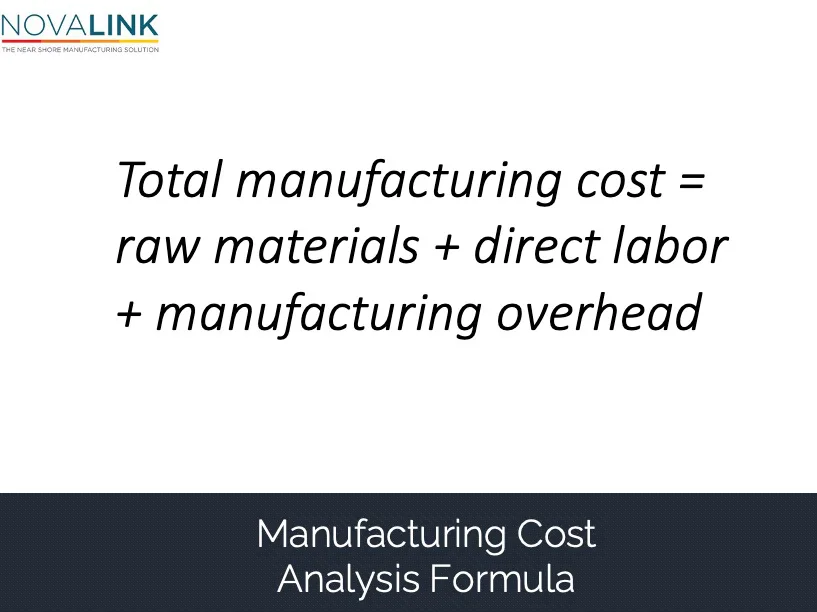
Benefits of a Manufacturing Cost Analysis
Cost analyses are beneficial as they make even the most complex business projects easier to understand. A thorough cost-benefit analysis puts all manufacturing projects in the simplest terms: benefits, minus all costs, equal net profit.
Another reason for conducting a manufacturing cost analysis is to understand and identify potential problems and benefits such as:
- Finding and estimating cost-saving opportunities
- Securing financing to provide for the costs of producing the manufactured product
- Calculating the true cost of production of the manufactured product
- When claiming government reimbursements, report the true cost of a program
The Importance of Manufacturing Cost Analysis
Here are some key reasons why cost analysis is of utmost importance:
- Cost Control and Reduction
- Manufacturing cost analysis helps identify cost drivers, allowing you to pinpoint areas where cost reduction is possible.
- By optimizing processes and finding cost-saving opportunities, you can enhance your company's bottom line.
- Pricing Strategies
- Knowing your manufacturing costs is essential for setting competitive prices while ensuring profitability.
- Accurate cost data helps you avoid underpricing products and leaving potential profits on the table.
- Competitive Advantage
- Understanding and managing your costs better than your competitors can give you a significant edge in the marketplace.
- Cost efficiency can lead to more competitive pricing or higher profit margins.
- Decision-Making
- A cost analysis informs crucial decisions like make or buy choices, product discontinuation, and scaling production.
- It provides the data needed to make informed, strategic choices that align with your business goals.
Steps in Performing a Manufacturing Cost Analysis
Performing a cost analysis involves several steps:
- Data Collection
- Gather financial data, including raw material costs, labor expenses, and overhead costs.
- Identify and categorize each cost component accurately.
- Cost Allocation
- Distinguish between direct and indirect costs and allocate them appropriately to specific products or projects.
- Calculating Total Manufacturing Cost
- Sum up all the direct and indirect costs to determine the total manufacturing cost for each product.
- Analyzing Cost Variances
- Identify favorable and unfavorable cost variances by comparing actual costs to budgeted costs.
- Conduct root cause analysis to understand the reasons behind these variances.
- Benchmarking and Industry Comparisons
- Compare your manufacturing costs with industry standards and benchmarks to assess your competitiveness.
- Creating Reports and Visualizations
- Present the data in a clear and comprehensible format, such as charts and reports, to aid decision-making.
Understanding Manufacturing Costs
Manufacturing costs can broadly be categorized into two groups: direct and indirect costs.
- Direct Costs
- Raw Materials: The cost of materials used in production, such as metals, plastics, or chemicals.
- Labor: The wages and benefits paid to employees directly involved in the production process.
- Manufacturing Overhead: These are indirect production costs, including utilities, maintenance, and depreciation on manufacturing equipment.
- Indirect Costs
- These are expenses not directly tied to the production of a specific product but necessary for overall operations, such as rent, office supplies, and management salaries.
Product Vs. Manufacturing Costs
It is worthwhile to remember that there is a difference between production and manufacturing costs. Production costs are the sum of all the expenses for the company doing business. However, manufacturing costs represent only the expense of making the product. A cost analysis will use both numbers to evaluate the total expense of a manufacturing business.
Production costs might include the fixed and changing costs of business operation. This may include:
- Cost of a facility
- Advertising
- Equipment
Manufacturing costs respond more to production volume changes. Generally, manufacturing costs can be associated with the same general categories of expenses: materials, labor, and overhead. All of these expenses are direct costs: For example, the salary of the company information technology workers and their equipment are not direct costs, but the salary and supplies of the factory workers are included.
Production Costs vs. Manufacturing Costs Example
Production costs and manufacturing costs are related concepts in business, but they refer to different aspects of producing costs. Let's clarify the difference between these two concepts with an example.
Production Costs Example:
Imagine a small clothing boutique that designs and produces custom-made dresses. The production costs for this boutique would include all the expenses directly associated with creating each dress.
Here's a breakdown of the production costs for the boutique:
- Raw Materials: This includes the cost of fabric, buttons, zippers, and other materials used to make the dresses.
- Labor Costs: The wages paid to the seamstresses who cut, sew, and assemble the dresses.
- Packaging Costs: The cost of packaging materials, such as garment bags and tags, used to present and protect the finished dresses.
- Direct Overhead: Any expenses directly linked to the dress production process, such as the electricity used for sewing machines and maintenance of the sewing equipment.
So, for the clothing boutique, production costs would be all the expenses specifically associated with creating the custom dresses they sell in their store.
Manufacturing Costs Example:
Now, let's consider a large-scale clothing manufacturing company that mass-produces dresses and distributes them to retail stores nationwide. Manufacturing costs for this company would encompass a wider range of expenses. This includes not only dress production costs but also other expenses related to running the manufacturing facility as a whole.
Here's a breakdown of the manufacturing costs for the clothing manufacturing company:
- Production Costs: Similar to the boutique, these would include all the expenses associated with producing each dress, such as raw materials, labor costs, packaging costs, and direct overhead related to the dress production.
- Indirect Labor Costs: This includes the wages of employees who are not directly involved in dress production but are essential for running the manufacturing facility, such as administrative staff, quality control inspectors, and maintenance workers.
- Indirect Materials Costs: Expenses related to materials used throughout the manufacturing facility but not directly in dress production. This might include office supplies, cleaning supplies, and spare parts for machinery.
- Facility Rent and Utilities: The cost of renting and maintaining the manufacturing facility, including expenses like rent, electricity, water, and heating/cooling.
- Depreciation: Allocation of the cost of machinery and equipment used in manufacturing over their useful life.
- Taxes and Insurance: Any property taxes and insurance premiums associated with the manufacturing facility.
So, for the clothing manufacturing company, manufacturing costs encompass a broader range of expenses, including not only those directly tied to dress production but also the overhead and operational costs necessary to run the entire manufacturing operation.
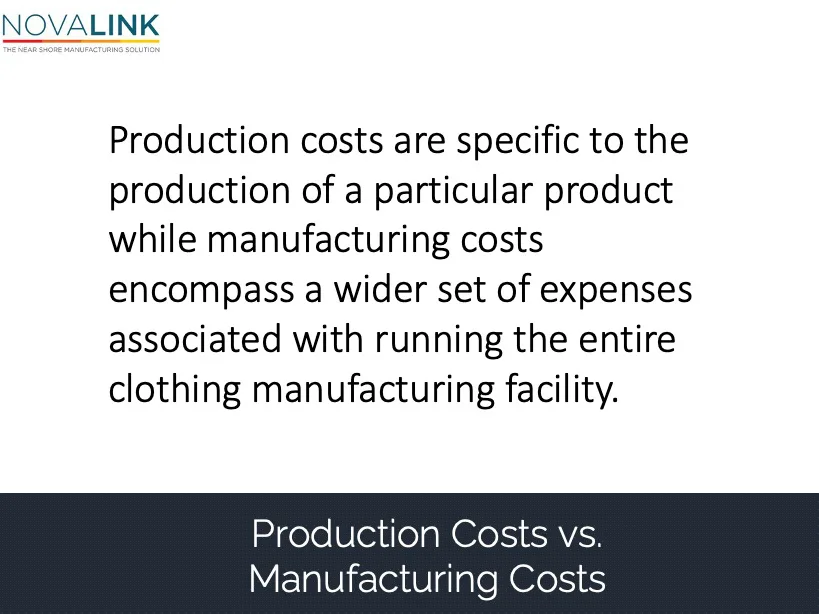
Labor and Manufacturing Overhead
After determining your product costs, the next significant phase in planning your manufacturing cost analysis is determining your production expenses. If your product needs direct labor (as is the case for most products manufactured in Mexico) your analysis must account for this, as well as the cost of manufacturing overhead.
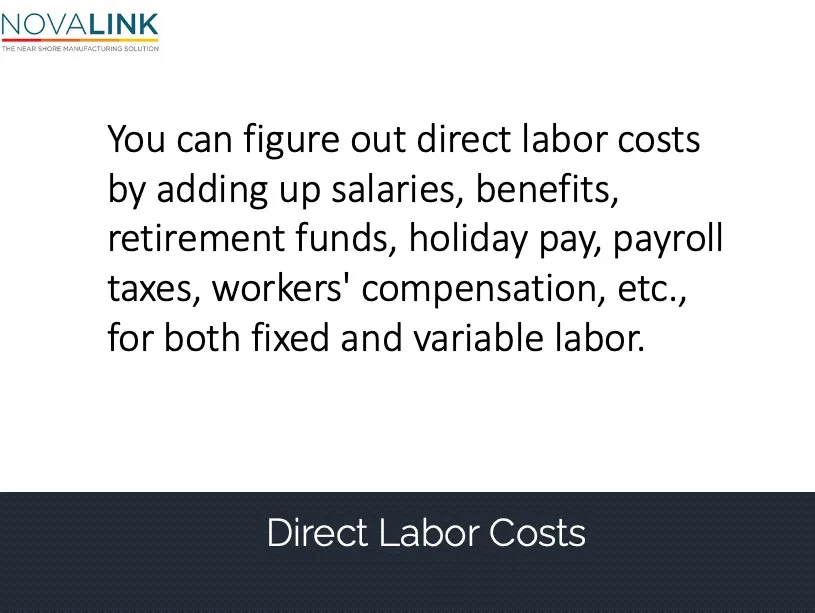
Manufacturing overhead covers expenses not directly tied to production costs. Common manufacturing overhead costs include:
- Utility bills (electricity, water, etc.)
- Equipment depreciation
- Factory supplies
- Quality inspectors
- Maintenance and repair
- Sanitation
- Administrative staff (bookkeepers, managers)
- Equipment setup personnel
- Material handlers (e.g., forklift operators)
- Facility-related costs (property taxes, insurance).
Challenges in Manufacturing Cost Analysis
Despite its benefits, a cost analysis comes with its fair share of challenges, including data accuracy and availability, the complexity of cost allocation, changing economic conditions, and technological advancements.
Best Practices for Effective Manufacturing Cost Analysis
To make the most of a cost analysis, consider these best practices:
- Regularly update cost data to reflect changes in your business.
- Promote cross-functional collaboration to ensure all aspects of cost analysis are considered.
- Embrace continuous improvement, using analysis insights to drive positive change.
- Explore advanced analytics and automation to enhance accuracy and efficiency.
Conclusion: In a Competitive Market, Manufacturing Cost Analysis Is an Essential Tool
Manufacturing cost analysis is an indispensable tool for businesses seeking to thrive in a competitive market. By understanding and managing your costs effectively, you can make informed decisions, optimize your operations, and maintain profitability. Embrace cost analysis as a strategic asset, and watch your business flourish in the complex landscape of modern manufacturing.
Partnering with a Nearshore Manufacturing partner like NovaLink can be a game-changer for businesses looking to conduct a robust cost analysis but also achieve overall manufacturing success. NovaLink offers an exceptional blend of advantages, such as geographical proximity, cultural alignment, and cost-effective labor, making them an ideal partner. Their local presence allows for easy collaboration, real-time communication, and hands-on oversight, which are essential for accurate cost analysis and efficient production. NovaLink's expertise in manufacturing and supply chain management can streamline processes, reduce lead times, and enhance product quality. By choosing NovaLink as a manufacturing partner, businesses can benefit from their extensive industry knowledge and experience. This ensures a smoother journey towards cost efficiency and production excellence.
FAQs on Doing A Manufacturing Cost Analysis
1. What is a manufacturing cost analysis, and why is it important?
A cost analysis is a systematic evaluation of all expenses associated with the production of goods. It is essential because it helps businesses understand and control costs, make informed decisions, set competitive prices, and maintain profitability.
2. What costs are typically included in a manufacturing cost analysis?
A cost analysis typically includes direct costs like raw materials, labor, and manufacturing overhead, as well as indirect costs such as facility rent, utilities, administrative expenses, and depreciation of equipment.
3. How can manufacturing cost analysis benefit my business?
A cost analysis can benefit your business by identifying cost-saving opportunities, optimizing processes, supporting pricing strategies, providing a competitive advantage, aiding in decision-making, and ultimately improving your bottom line.
4. What tools and software are useful for conducting a manufacturing cost analysis?
Tools like spreadsheet software (e.g., Excel), cost accounting software, Enterprise Resource Planning (ERP) systems, and data visualization tools are commonly used for conducting a cost analysis, helping streamline the process and improve accuracy.
5. Is manufacturing cost analysis a one-time effort, or should it be an ongoing practice?
A cost analysis is not a one-time effort; it should be an ongoing practice. Businesses benefit from regularly updating cost data, conducting continuous improvement initiatives, and adapting to changing economic conditions to maintain competitiveness and profitability.
About NovaLink
As a manufacturer in Mexico, NovaLink employs a unique approach that transcends the traditional model of shelter production. More than just the location of your manufacturing, we would like to become a partner in your manufacturing in Mexico. You will be able to relocate or initiate manufacturing for your company in Mexico in a low-cost labor environment with very little delay or up-front costs. Find out how we can help you by handling the manufacturing process.
There are NovaLink facilities in the border cities of Brownsville, Texas, Matamoros, Mexico, and Saltillo, Mexico.