Last Updated on November 12, 2024
When managing a maquiladora, there are many factors to consider. From understanding cultural differences to navigating labor laws, managing a maquiladora workforce can be challenging. However, with the right strategies, you can unlock significant opportunities for growth and efficiency. A nearshore manufacturing partner like NovaLink can make this journey smoother by ensuring compliance, boosting productivity, and reducing costs.
What is a Maquiladora?
A maquiladora is a factory in Mexico run by a foreign company that exports its products to that company’s country. These facilities are primarily located near the U.S.-Mexico border and provide an excellent opportunity for companies to cut costs by taking advantage of lower labor costs and proximity to the U.S. market. Managing a maquiladora, however, involves more than just setting up operations—it requires a deep understanding of local practices and workforce management.
Why Managing a Maquiladora Workforce is Different
Managing a maquiladora workforce is not like managing a traditional workforce in the United States or Europe. Mexico faces unique challenges, including language barriers, cultural differences, and different labor laws. Employee expectations can vary significantly. A one-size-fits-all approach won't work. You need tailored strategies that cater to these specific circumstances.
Key Best Practices for Managing a Maquiladora Workforce
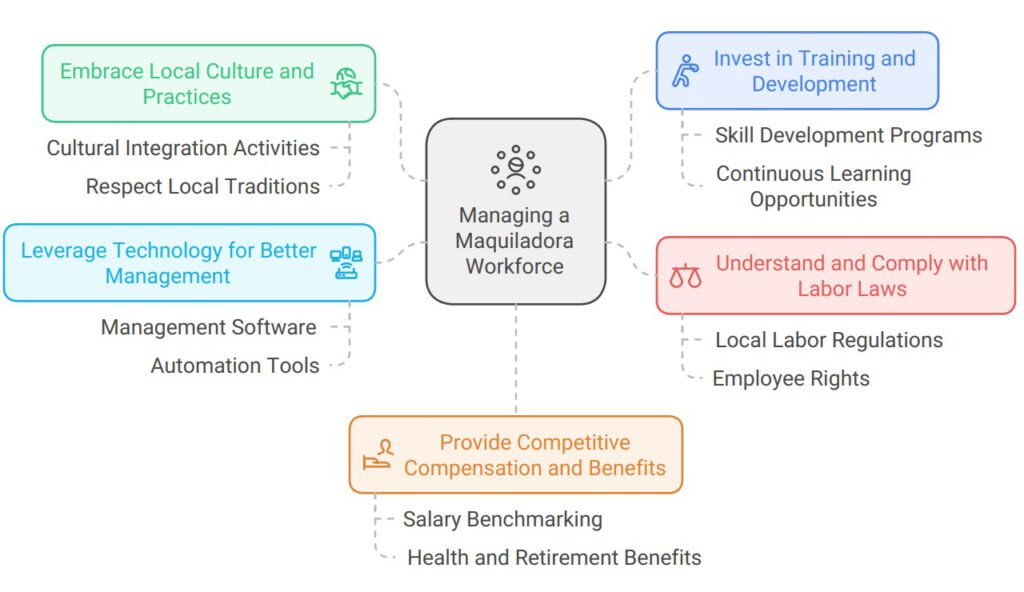
1. Embrace Local Culture and Practices
To effectively manage a maquiladora, you must embrace the local culture. Mexican work culture often places a high value on relationships and community. Showing respect for these values can lead to a more harmonious and productive workplace. This includes celebrating local holidays, understanding social norms, and fostering a family-like atmosphere.
To address this issue, leaders should take proactive steps to immerse themselves in Mexican culture and actively engage with their local teams. This approach involves more than just occasional visits or superficial interactions. Leaders should invest time in understanding the history, traditions, and values that shape the Mexican workplace culture. - LinkedIn
2. Invest in Training and Development
Well-trained workforces are essential for success in any manufacturing environment. Regular training programs can help employees acquire updated skills, improve efficiency, and stay updated with technological advancements. Training should be a continuous process that includes job-specific skills but also leadership and soft skills. By investing in your employees' growth, you will see improved job satisfaction and lower turnover rates.
3. Understand and Comply with Labor Laws
Navigating Mexico’s labor laws can be complex. These regulations cover everything from the minimum wage and overtime pay to working conditions and employee rights. It is crucial to stay up-to-date with these laws to avoid costly penalties. Partnering with a knowledgeable nearshore manufacturer like NovaLink can help ensure compliance with all local regulations.
4. Leverage Technology for Better Management
Managing a large, often geographically dispersed workforce, such as those in
Maquiladoras, presents significant challenges. Modern HR software simplifies this by automating key functions like scheduling, payroll, and labor law compliance.
By centralizing these tasks, companies can reduce administrative burdens and ensure processes are consistently applied across the workforce, regardless of location.
5. Provide Competitive Compensation and Benefits
While labor costs are lower in Mexico, competitive compensation remains critical to attracting and retaining top talent. Maquiladoras operate on tight margins and depend heavily on a highly efficient, productive workforce to meet demanding production schedules and quality standards. Top talent, including skilled workers, supervisors, and managers, plays a critical role in ensuring operations run smoothly, minimizing downtime, and maximizing output. Losing experienced employees can disrupt workflow, lower productivity, and cause delays in meeting client demands, ultimately affecting the company's bottom line.
How Nearshore Partners Like NovaLink Can Help Manage a Maquiladora
Partnering with a nearshore manufacturing expert like NovaLink can significantly ease maquiladora management complexities. With deep knowledge of local laws, culture, and best practices, NovaLink can help you navigate the challenges of managing a workforce in Mexico. We offer end-to-end solutions, from hiring and training to compliance and logistics, allowing you to focus on your core business operations.
Conclusion
Managing a maquiladora workforce in Mexico can be rewarding if done correctly. By embracing local culture, investing in training, complying with labor laws, prioritizing communication, leveraging technology, and offering competitive compensation, you can build a productive and engaged workforce. Partnering with a nearshore manufacturing company like NovaLink ensures local expertise and resources needed to manage your maquiladora efficiently.
By adopting these best practices, you will optimize your operations and create a thriving, motivated workforce. Remember, managing a maquiladora isn’t just about overseeing a factory—it's about building relationships, fostering growth, and driving success.
FAQs for Managing a Maquiladora Workforce in Mexico
1. What is a maquiladora, and why is it important?
A maquiladora is a manufacturing operation in Mexico run by a foreign company, primarily for export back to that company's country. It is essential because it offers cost savings and access to skilled labor, helping businesses stay competitive.
2. How does NovaLink help in managing a maquiladora?
NovaLink provides expertise in local labor laws, recruitment, training, compliance, and logistics. This ensures smoother operations, fewer risks, and higher efficiency in managing a maquiladora.
3. What are the key challenges in managing a maquiladora workforce?
The main challenges include navigating cultural differences, language barriers, and complying with local labor laws. Understanding these factors is crucial for successful workforce management.
4. Why is understanding local culture important for managing a maquiladora?
Embracing local culture helps build trust, improves employee satisfaction, and fosters a positive work environment, ultimately leading to better productivity and reduced turnover.
5. What role does technology play in managing a maquiladora?
Technology streamlines HR processes, improves communication, and provides valuable insights into workforce performance, making it easier to manage a maquiladora efficiently.
Explore More: Discover Related Blog Posts
Expand your knowledge and delve deeper into Maquiladoras in Mexico with our curated collection of related blog posts.
- What Type of Company Should Not Move to Mexico?
- Mexico’s Manufacturing Workforce in 2025: A Game-Changer for Global Industry
- How to Find the Best Maquiladora for Your Manufacturing Needs
- Strategic Measures to Fortify Mexico’s Textile Industry Under President Claudia Sheinbaum
- Labor vs. Land: What Costs More in Mexican Manufacturing?
About NovaLink
As a manufacturer in Mexico, NovaLink employs a unique approach that transcends the traditional model of shelter production. More than just the location of your manufacturing, we would like to become a partner in your manufacturing in Mexico. You will be able to relocate or initiate manufacturing for your company in Mexico in a low-cost labor environment with very little delay or up-front costs. Find out how we can help you by handling the manufacturing process.
There are NovaLink facilities in the border cities of Brownsville, Texas, Matamoros, Mexico, and Saltillo, Mexico.