Last Updated on September 5, 2023
Today, wires are the lifelines that connect various electrical components, enabling power and information to flow seamlessly. Various industries depend on wire harnesses to organize and secure these connections, ensuring maximum performance and reliability. This article explores the intricacies of wire harness manufacturing, its significance, the manufacturing process, and the benefits of outsourcing. Furthermore, we will delve into why making wire harnesses in Mexico with a nearshore manufacturing partner like NovaLink can be a smart decision.
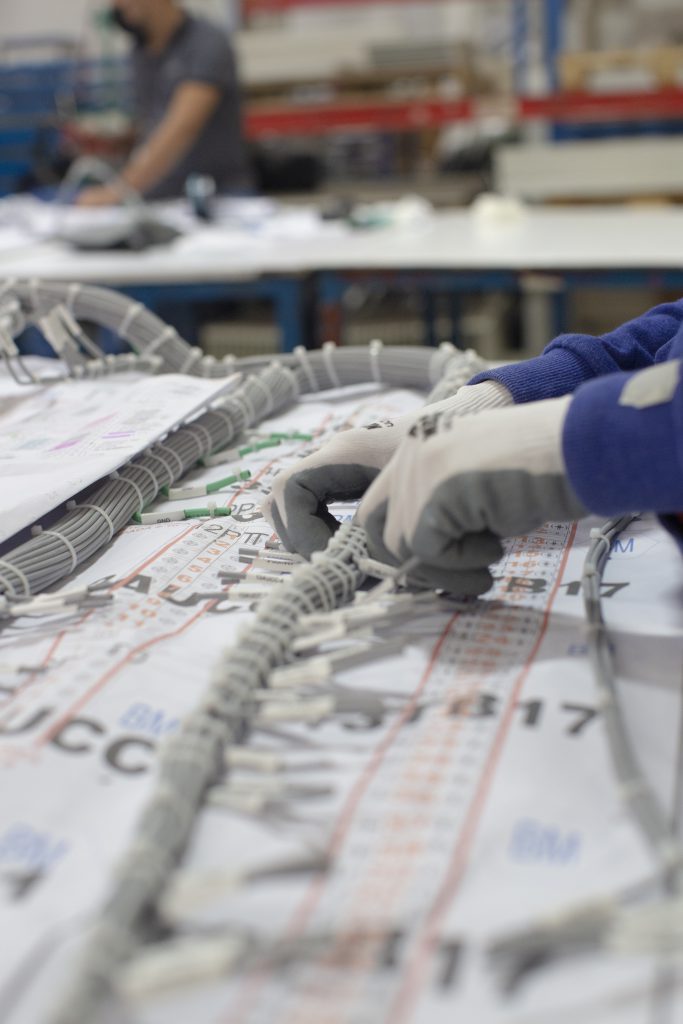
Wire Harness Manufacturing at NovaLink
Understanding Wire Harness Manufacturing
What is a Wire Harness?
Cable harnesses and wire harnesses are bundled arrangements of wires, cables, and connectors that transmit signals and power between different components in a system. The system serves as a centralized communication pathway, thereby simplifying the process of installation, maintenance, and troubleshooting.
Importance of Wire Harness Manufacturing
Wire harness manufacturing plays a pivotal role in industries such as automotive, aerospace, telecommunications, and consumer electronics. It ensures efficient electrical connectivity, reduces the risk of short circuits or wiring errors, enhances system reliability, and enables faster production cycles. Well-designed and properly manufactured wire harnesses contribute to improved overall system performance, durability, and safety.
Though transmitting electrical signals is the primary goal of a wiring harness, in the bigger picture, these electrical components are much more important than you’d realize. The harness makes connecting to larger components easier by combining the wiring into a single unit for a "drop-in" installation. Instead of multiple cables running in parallel, a wire harness provides a centralized connection point that is safe.
What Is the Importance of Wiring Harness?
Wire Harness Manufacturing and the Automotive Industry
Wire harness manufacturing plays a crucial role in the automotive industry, providing a vital component for the functioning of vehicles. A wire harness, also known as a cable harness or wiring assembly, is a bundled arrangement of wires, connectors, and terminals that transmit electrical signals and power throughout the vehicle. It serves as the central nervous system, connecting various electrical components and systems within the vehicle, including the engine, lighting, sensors, infotainment, and more.
The importance of wire harness manufacturing in the automotive industry can be summarized as follows:
- Electrical System Integration: Modern vehicles are equipped with complex electrical systems that require efficient integration of numerous components. Wire harnesses simplify the installation process by consolidating the wiring into a single assembly. This standardized approach not only saves time during assembly but also ensures proper connections, reducing the risk of electrical faults and improving overall reliability.
- Enhanced Safety and Durability: Wire harnesses are designed to withstand the harsh operating conditions of the automotive environment, including vibration, temperature fluctuations, moisture, and exposure to chemicals. They are manufactured using high-quality materials and undergo rigorous testing to meet stringent safety and durability standards. Properly engineered wire harnesses minimize the risk of short circuits, electrical failures, and potential safety hazards, ensuring the safe operation of vehicles.
- Efficient Manufacturing and Cost Optimization: Wire harness manufacturing involves precise design, automated assembly processes, and streamlined production techniques. By outsourcing wire harness production to specialized manufacturers, automakers can leverage their expertise, advanced machinery, and economies of scale, resulting in cost savings and improved production efficiency. Standardized wire harnesses also simplify vehicle assembly, reducing labor time and costs on the assembly line.
- Flexibility and Scalability: Wire harnesses can be customized to meet the specific requirements of different vehicle models and configurations. Automotive manufacturers can easily adapt wire harness designs to accommodate technological advancements, changes in vehicle architecture, or the integration of new features. This flexibility allows for seamless integration of advanced safety systems, connectivity features, and emerging technologies, supporting the evolution of the automotive industry.
- Maintenance and Repairs: Wire harnesses are designed for easy installation, maintenance, and troubleshooting. When repairs or replacements are necessary, having a standardized wire harness makes the process more efficient, as technicians can quickly identify and replace the faulty components. This minimizes vehicle downtime and reduces repair costs, benefiting both vehicle owners and service centers.
Wire Harness Manufacturing Process
The manufacturing process of wire harnesses involves several stages, each contributing to the final product's quality and functionality:
- Design and Engineering: The wire harness manufacturing process begins with meticulous design and engineering. This stage involves understanding the system requirements, component interconnections, and electrical specifications. Designers create detailed schematics and layouts to determine the optimal routing, wire lengths, and connector types required for the harness.
- Material Selection: Once the design is finalized, the next step is selecting suitable materials. High-quality wires, cables, connectors, and protective sleeves are chosen based on factors such as voltage rating, current carrying capacity, environmental conditions, and industry standards. Careful material selection ensures long-term reliability and durability of the wire harness.
- Cutting and Stripping Wires: In this stage, wires are cut to the required lengths and stripped of their insulation, exposing the conductor. Advanced cutting and stripping machines automate this process, ensuring precise and consistent results while minimizing the risk of damage to the conductor.
- Crimping and Terminating: Crimping and terminating involve securely attaching connectors to the stripped ends of the wires. Specialized crimping tools and machines are used to create reliable electrical connections. The crimping process must be executed with precision, as improper crimps can lead to intermittent connections, signal loss, or premature failure.
- Harness Assembly: Once the individual wires are prepared, the harness assembly process begins. Skilled technicians carefully route and bundle the wires according to the design specifications, taking care to maintain proper wire orientation, separation, and strain relief. Harnesses are often secured with zip ties, tape, or woven sleeves for added protection and organization.
- Testing and Quality Control: After assembly, thorough testing and quality control measures are implemented to ensure the wire harness meets all performance and safety requirements. Continuity tests, insulation resistance tests, and high-voltage tests are performed to identify any defects or inconsistencies. Only harnesses that pass these rigorous tests are deemed ready for deployment.
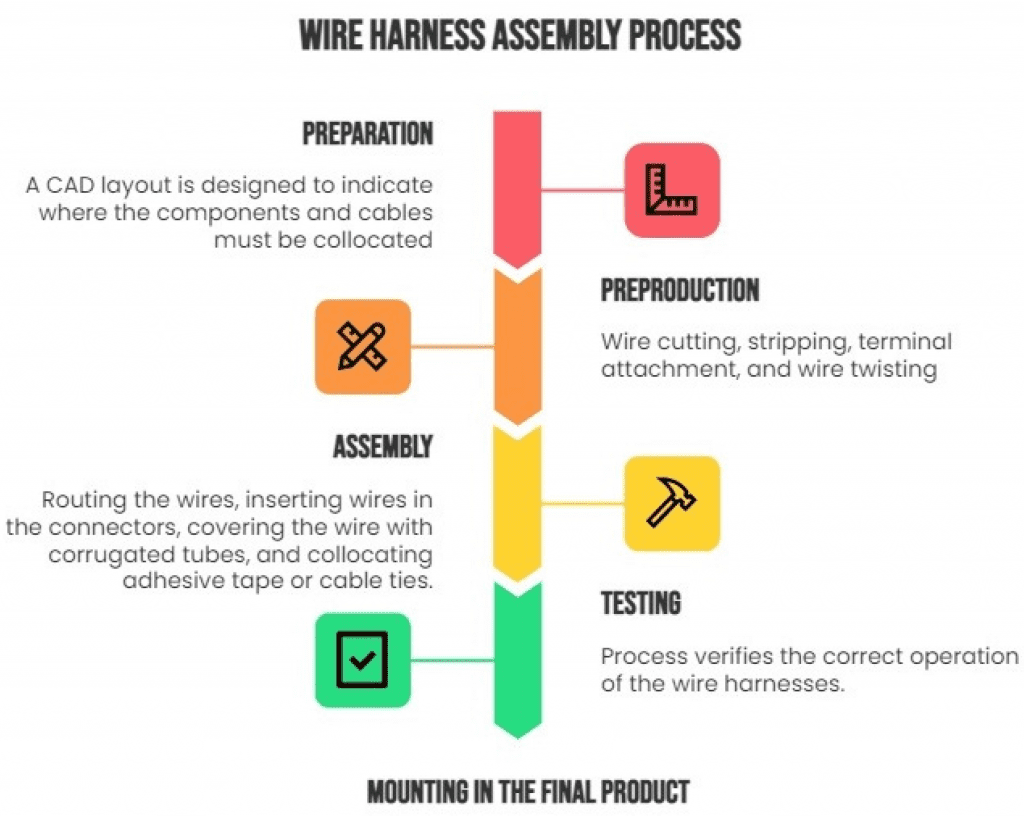
Benefits of Outsourcing Wire Harness Manufacturing
Outsourcing wire harness manufacturing offers numerous advantages for companies across different industries. Let's explore some of these benefits:
- Cost Savings and Expertise: Outsourcing wire harness manufacturing allows companies to leverage the expertise and economies of scale of specialized manufacturers. By partnering with experienced providers, businesses can access cost-effective solutions without the need for significant upfront investments in equipment, infrastructure, and labor.
- Access to Skilled Labor: Outsourcing to reputable wire harness manufacturers provides access to skilled labor with specialized knowledge in harness design, engineering, and manufacturing. These professionals stay updated with the latest industry trends, regulations, and advancements, ensuring high-quality products that meet or exceed industry standards.
- Proximity and Communication: Choosing a nearshore manufacturing partner like NovaLink in Mexico offers the advantage of geographical proximity. Being closer to the manufacturing site facilitates easier communication, faster response times, and efficient collaboration. This proximity reduces lead times, enhances project management, and enables seamless coordination between the company and the manufacturing partner.
- Supply Chain Optimization: Outsourcing wire harness manufacturing can streamline the supply chain. Manufacturing partners like NovaLink have established networks of suppliers, ensuring a steady supply of quality materials at competitive prices. This optimization reduces logistics costs, minimizes production delays, and enhances overall supply chain efficiency.
Outsourcing to a certified cable harness manufacturer will ensure better quality, durability and the wiring harnesses will be warrantied against performance failures for a minimum of 1 year.
When recommended manufacturing practices are not strictly adhered to, it is common for poor terminations to be the root cause of 80% of the system-level troubleshooting.
Advantages of Outsourcing Wire Harnesses Domestically
Wire Harness Manufacturing in Mexico: The NovaLink Advantage
Nearshore Wire Harness Manufacturing in Mexico
Mexico's emergence as a leading nearshore manufacturing destination for wire harnesses can be attributed to its strategic location, skilled labor force, favorable business environment, and robust infrastructure. These factors make Mexico an ideal choice for companies looking to manufacture wire harnesses with high quality, cost-effectiveness, and proximity to key markets.
Advantages of Manufacturing Wire Harnesses in Mexico
Using a nearshore manufacturing company such as NovaLink in Mexico to manufacture wire harnesses offers several advantages:
- Cost-Effectiveness: Mexico provides cost advantages due to lower labor and operational costs compared to many other countries. This cost-effectiveness translates into competitive pricing for wire harness manufacturing services.
- Skilled Workforce: The Mexican labor force is well-educated and technically proficient. Wire harness manufacturers undergo rigorous training to ensure that their products meet international standards and are of the highest quality.
- Proximity and Time Zone: As a result of its proximity to the United States, wire harness manufacturing can be conducted in a shorter period of time and at a lower cost. As a result of the reduced distance between manufacturing facilities in Mexico and customer locations in the United States, production schedules can be met more quickly and customer demands can be met more effectively. Furthermore, wire harness manufacturers can save money in the long run due to lower logistics costs associated with shorter shipping distances.
- Cultural Affinity: Mexico's cultural affinity and business practices that align with North American companies greatly benefit wire harness manufacturing. The shared cultural similarities between Mexico and North America create a conducive environment for collaboration, understanding, and successful partnerships. Mexican workers often possess a good understanding of North American business norms, which facilitates effective communication and reduces potential language and cultural barriers that can impede project progress.
Conclusion: Wire Harness Manufacturing in Mexico Has Advantages
Wire harness manufacturing is an essential process that ensures efficient electrical connectivity and reliability in various industries. Outsourcing wire harness manufacturing offers numerous benefits, including cost savings, access to expertise, proximity advantages, and supply chain optimization.
Choosing a nearshore manufacturing partner like NovaLink in Mexico further enhances these advantages. Mexico provides a cost-effective manufacturing environment with a skilled workforce and cultural affinity to North American companies. Proximity to the United States enables faster response times, reduced shipping costs, and seamless communication.
By partnering with NovaLink for wire harness manufacturing in Mexico, companies can leverage these benefits to streamline their operations, improve efficiency, and meet their production needs effectively.
FAQs
Here are some frequently asked questions about wire harness manufacturing:
Q1: What industries benefit from wire harness manufacturing? Wire harness manufacturing is vital in industries such as automotive, aerospace, telecommunications, consumer electronics, medical devices, and more. Any industry that requires efficient electrical connectivity can benefit from wire harnesses.
Q2: Why is it important to ensure quality in wire harness manufacturing? Ensuring quality in wire harness manufacturing is crucial to maintain reliable electrical connections, prevent system failures, and ensure the safety of users. High-quality harnesses contribute to overall system performance and longevity.
Q3: How can outsourcing wire harness manufacturing save costs? Outsourcing wire harness manufacturing eliminates the need for significant upfront investments in equipment, infrastructure, and labor. It allows companies to access cost-effective solutions, leverage specialized expertise, and optimize their production costs.
Q4: What are the advantages of nearshore manufacturing in Mexico? Nearshore manufacturing in Mexico offers advantages such as lower labor and operational costs, a skilled workforce, proximity to the United States, and cultural affinity. These factors contribute to cost savings, faster response times, and effective collaboration.
Q5: How can NovaLink support wire harness manufacturing in Mexico? NovaLink, as a nearshore manufacturing partner in Mexico, provides expertise in wire harness design, engineering, and manufacturing. They offer cost-effective solutions, a skilled labor force, supply chain optimization, and efficient communication for successful wire harness production.
About NovaLink
As a manufacturer in Mexico, NovaLink employs a unique approach that transcends the traditional model of shelter production. More than just the location of your manufacturing, we would like to become a partner in your manufacturing in Mexico. You will be able to relocate or initiate manufacturing for your company in Mexico in a low-cost labor environment with very little delay or up-front costs. Find out how we can help you by handling the manufacturing process.
There are NovaLink facilities in the border cities of Brownsville, Texas, Matamoros, Mexico, and Saltillo, Mexico.
Explore More: Discover Related Blog Posts
Expand your knowledge and delve deeper into electronics manufacturing in Mexico with our curated collection of related blog posts.
- Car Brands Made in Mexico: A Look at Global Manufacturing Powerhouses
- Shifting Gears: Top 5 Automotive Manufacturing Trends in Mexico
- How Kitting Services in Mexico Streamline Your Manufacturing Operations
- The Auto Industry’s Production Advantage in Mexico: Analyzing the Factors Driving Mexico’s Success as a Global Automotive Manufacturing Hub
- Beyond the Maquiladora: Exploring the Diversification of Mexican Manufacturing