Last Updated on May 1, 2025
When it comes to manufacturing, companies are always looking for ways to reduce costs while maintaining quality. One of the biggest factors in this equation is the workforce. In this article, we’ll compare the workforce in Mexico and China to determine which is more skilled and cost-effective.
The Workforce in Mexico vs. China: A Comparative Analysis
The Workforce in Mexico
Mexico has emerged as a major player in the manufacturing industry due to its proximity to the United States and strong trade agreements. The country boasts a sizable workforce with diverse skill sets, making it an attractive option for businesses looking to establish or expand manufacturing operations.
Skill Level in Mexico
When it comes to the Mexican workforce's skill level, there is a wide range of capabilities available. The country has a robust education system that produces graduates in various technical and engineering fields. Mexico has invested heavily in vocational training programs to enhance its workforce's skill sets, particularly in areas such as automotive manufacturing, aerospace, and electronics.
In the realm of global trade, Mexico stands out as a significant player in several key industries:
- IT Industry: As the 3rd-largest exporter worldwide, Mexico has carved out a strong position in the global technology market.
- Aerospace Industry: Mexico ranks as the 6th-largest supplier to the American aerospace sector, reflecting the country's advanced manufacturing capabilities and skilled workforce.
- Medical Devices: Leading the supply chain to the U.S., Mexico dominates this industry with its well-developed infrastructure and expertise.
This combination of skilled labor and strategic industry presence underscores Mexico's role as a pivotal hub for manufacturing and exports. The synergy between education, vocational training, and industry leadership makes it a formidable competitor on the world stage.
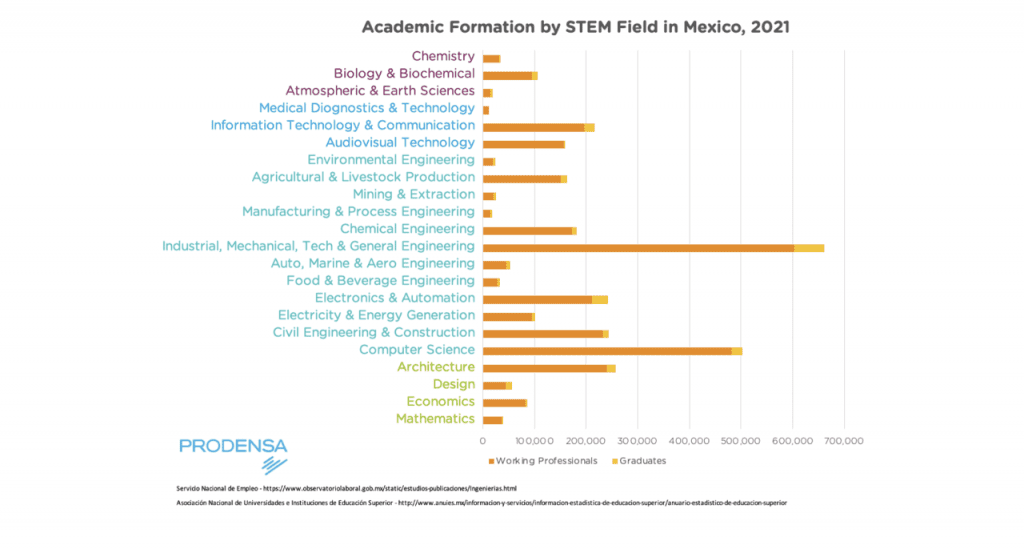
Source: LinkedIn "Stem Workforce in Mexico" https://www.linkedin.com/pulse/stem-workforce-mexico-robin-conklen/
Moreover, Mexico's proximity to the United States has allowed knowledge transfer and collaboration between Mexican and American companies. This has further contributed to Mexican workers' specialized skills development. Companies operating in Mexico can leverage this skilled workforce to achieve high-quality production and innovation.
In Tijuana and throughout Baja California, many students take advantage of exchange programs with California’s top universities. These programs not only foster international academic collaboration but also broaden students' perspectives and skills, preparing them for a global job market.
Some schools are even partnering with foreign companies for R&D and design projects. These partnerships allow students and faculty to engage in cutting-edge research and development, enhancing the educational experience and directly contributing to industry advancements. Through such collaborations, both educational institutions and businesses benefit from shared expertise and innovative solutions.
Increase in the Number of Graduates in the Fields of Engineering, Manufacturing, and Construction
Over the past decade, Mexico has seen a remarkable increase in the number of graduates in the fields of engineering, manufacturing, and construction. A decade ago, these fields had just over 60,000 graduates. Fast forward to today, and the number has nearly doubled, currently surpassing 110,000 annually. This impressive growth highlights the country's expanding focus on developing skilled professionals in these critical industries.
How Mexico's Labor Force is Boosting Manufacturing Growth
Mexico's manufacturing industries, particularly in sectors like aerospace, automotive, medical devices, and electronics, are witnessing remarkable growth. A key driver of this expansion is the country's dynamic labor force, which is attracting interest from global companies, including those from the United States.
Rise of a Skilled Workforce
Over the past decade, the number of engineering, manufacturing, and construction graduates in Mexico has seen a substantial increase. This surge, from just over 60,000 to nearly 114,000 graduates annually, underscores an educational transformation focused on skill development for advanced industries. The influx of over 110,000 engineers per year forms a solid foundation for innovation and manufacturing capability.
Transition to Complex Manufacturing
Mexico is moving beyond basic assembly operations, stepping up to produce sophisticated goods. It ranks as the third-largest exporter in the IT sector and a crucial supplier for the American aerospace and medical device industries. Such achievements highlight the country's ability to handle complex manufacturing needs, fueled by a workforce that is both skilled and adaptable.
Educational Initiatives and International Collaboration
With more than 2,500 higher education institutions, Mexico offers advanced training that aligns with industry demands. Some institutions collaborate with international companies on research and development projects, enhancing their relevance in the global market. In regions like Baja California, partnerships with top-tier California universities through exchange programs are popular, polishing the bilingual and technical skills of graduates.
Government Support and Vocational Training
The Mexican government plays a pivotal role in strengthening the labor market by investing in education and vocational training. Emphasizing both additional college coursework and trade schools, these initiatives ensure a steady pipeline of qualified professionals. Tailoring programs to meet specific industry needs provides invaluable hands-on experience, preparing students with practical skills sought by employers.
In summary, the coordinated efforts in education and skill development, coupled with strategic governmental support, make Mexico's labor force a fundamental pillar in propelling the growth and sophistication of its manufacturing industries.
How Do Training Programs in Mexico Provide Hands-On Experience for Students?
Training programs in Mexico are designed to immerse students in practical learning environments, bridging the gap between education and industry demands. These programs often include practical sessions that take place directly on job sites. This real-world exposure is invaluable, as it equips participants with the skills necessary to thrive in their chosen fields.
On-Site Learning Opportunities
Students have the chance to work alongside seasoned professionals, allowing them to observe and participate in actual work processes. This collaboration not only enhances their technical skills but also familiarizes them with the dynamics of a professional workplace.
Step-by-Step Skill Development
- Initial Training Modules: Students start with foundational lessons, which cover essential theories and methodologies.
- Practical Projects: These are gradually introduced, where students apply learned concepts in controlled, yet realistic settings.
- Job Site Engagements: Advanced stages of the programs involve assignments at real job sites, offering a hands-on approach under the supervision of experienced mentors.
By experiencing the day-to-day operations within their industry, students are much more prepared for employment upon program completion. This methodological approach boosts their employability, significantly easing the transition from education to a professional career path.
The Role of Local and Regional Governments in Supporting Mexico's Skilled Workforce
Local and regional governments in Mexico play a pivotal role in fostering a skilled workforce crucial for the nation's more advanced, technical industries. Their efforts are focused on enhancing the workforce through various strategic initiatives:
- Incentivizing Education and Training: These governments actively promote and incentivize specialized training programs designed to equip workers with the necessary skills for technical roles. By offering subsidies or financial support for education in fields like engineering, IT, and manufacturing, they ensure a steady flow of qualified professionals.
- Collaborating with Educational Institutions: They partner with universities, technical schools, and vocational institutions to align curricula with industry needs. This collaboration ensures that students graduate with practical, relevant skills that match the demands of high-tech sectors.
- Facilitating Industry Partnerships: Governments work closely with local and international companies to identify skill gaps and develop targeted training programs. By facilitating industry partnerships, they help create employment opportunities and boost workforce readiness for technical industries.
- Providing Employment Incentives: To attract and retain talent, some regions offer tax breaks or other incentives to companies that invest in workforce development. This not only supports individual career growth but also strengthens the local economy.
Through these comprehensive strategies, local and regional governments ensure that Mexico's workforce is well-prepared to thrive in increasingly complex technical industries.
Cost Factors in Mexico
In addition to skill level, cost factors play a crucial role in business decision-making. Mexico offers competitive labor costs compared to many developed countries, including the United States. Mexico's lower cost of living and wages make it an attractive destination for companies seeking to optimize their production costs while maintaining quality.
Mexico also offers tax incentives and free trade agreements that can further reduce business costs. These factors, combined with the availability of a skilled workforce, make Mexico an appealing choice for companies looking to streamline their manufacturing operations.
Understanding the Shelter Program in Mexico for Foreign Manufacturers
The shelter program in Mexico is crafted to provide foreign manufacturing companies with a simplified entry into the Mexican market while minimizing risk and liability.
Key Objectives of the Shelter Program:
- Risk Mitigation: By operating under a shelter program, foreign companies can bypass the necessity of establishing their own legal entity in Mexico. This structure significantly reduces exposure to local legal risks and liability concerns.
- Operational Simplicity: With the shelter model, companies are able to focus entirely on their core business—manufacturing. The complexities of permits, facility leasing, and administrative tasks such as HR and accounting are managed by the shelter operator.
- Control and Flexibility: While administrative burdens are outsourced, companies maintain full control over their production processes and manufacturing operations. This balance allows for efficient and straightforward expansion into the Mexican market.
- Cost Efficiency: By leveraging existing infrastructure and expertise, companies save on the costs and effort that would otherwise be spent on establishing and managing a new entity from scratch.
In essence, the shelter program acts as a bridge for foreign manufacturers, offering both operational advantages and strategic security while they navigate the complexities of international expansion.
The Workforce in China
China, often referred to as the "factory of the world," has long been a dominant force in global manufacturing. The country's massive population and industrial infrastructure have made it a manufacturing powerhouse. Let's explore the skill level and cost factors associated with the Chinese workforce.
Skill Level in China
China has made significant progress in improving its workforce's skill level over the years. The country has invested heavily in its education system, with a focus on the science, technology, engineering, and mathematics (STEM) fields. Chinese universities produce a large number of graduates in engineering and technical disciplines, ensuring a steady supply of skilled workers for the manufacturing sector.
Additionally, China's emphasis on vocational training programs and apprenticeships has further enhanced its workforce's skill sets. The country's strong work ethic and dedication to continuous improvement also contribute to its manufacturing excellence reputation.
Cost Factor in China
While China has long been associated with low labor costs, it is essential to note that wages have steadily increased in recent years. As the country's economy grows and labor rights become more of a focus, companies operating in China must navigate increased labor costs.
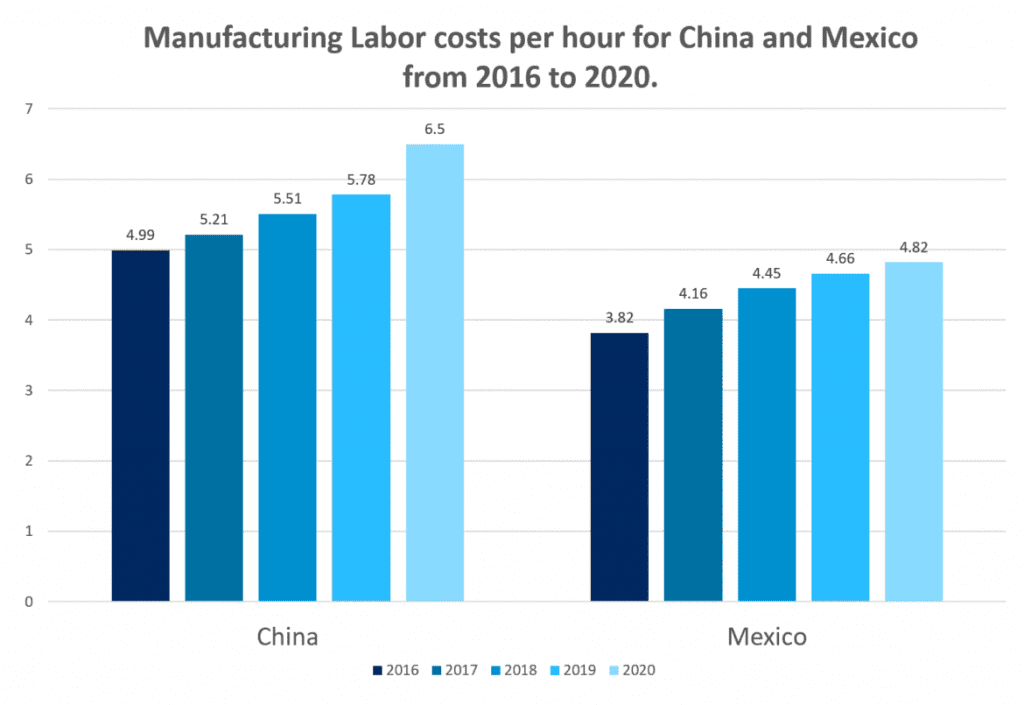
Source: Source: Manufacturing in Mexico vs China, Mexcentrix Strategic Solutions https://topforeignstocks.com/2021/05/24/comparing-manufacturing-labor-cost-in-china-and-mexico/
However, despite these rising costs, China still offers competitive advantages in terms of economies of scale and an extensive supply chain network. The country's established infrastructure and access to raw materials contribute to manufacturing cost efficiencies.
Conclusion
Choosing between Mexico and China for manufacturing operations involves careful consideration of various factors, including the skill level and cost-effectiveness of the workforce. Both countries offer unique advantages, with Mexico's proximity to the United States and competitive labor costs, and China's vast industrial infrastructure and supply chain network.
FAQs (Frequently Asked Questions)
1. Are there any language barriers when working with the Mexican workforce?
No, language barriers are not a significant concern when working with the Mexican workforce. English proficiency is relatively high among professionals, especially in the manufacturing industry. Additionally, many companies provide language training programs to ensure effective communication and collaboration with international partners.
2. Does China have an advantage in terms of infrastructure compared to Mexico?
Yes, China has a well-developed infrastructure that supports its manufacturing capabilities. The country has invested heavily in building highways, railways, ports, and other transportation systems. These infrastructure developments facilitate the movement of goods, raw materials, and workers, contributing to the overall efficiency of the manufacturing sector.
3. Which country offers better intellectual property protection?
China has taken significant steps in recent years to improve its intellectual property protection laws and regulations. While there have been concerns in the past, the Chinese government has shown a commitment to enforcing intellectual property rights. Mexico also has a legal framework in place to protect intellectual property, but the enforcement may vary compared to China.
4. How does the cultural aspect influence the workforce in Mexico and China?
Culture plays a significant role in the workplace dynamics of both Mexico and China. Mexican culture is known for its warmth, hospitality, and strong family values. In contrast, Chinese culture emphasizes discipline, hierarchy, and collective harmony. These cultural differences can influence management styles, communication approaches, and teamwork within organizations.
5. What are the key considerations for businesses when choosing between Mexico and China?
When choosing between Mexico and China, businesses should consider factors such as skill sets required for their specific industry, cost considerations, market access, intellectual property protection, infrastructure, and cultural compatibility. Conducting a thorough analysis of these factors will help businesses make an informed decision that aligns with their strategic objectives.
6. Is it possible to benefit from the advantages of both Mexico and China?
Yes, some companies choose to leverage the advantages of both Mexico and China. This approach, known as nearshoring, involves establishing manufacturing operations in Mexico to cater to the North American market while maintaining a presence in China to tap into the Asian market. By strategically utilizing the strengths of each country, businesses can maximize their competitiveness and market reach.
About NovaLink
As a manufacturer in Mexico, NovaLink employs a unique approach that transcends the traditional model of shelter production. More than just the location of your manufacturing, we would like to become a partner in your manufacturing in Mexico. You will be able to relocate or initiate manufacturing for your company in Mexico in a low-cost labor environment with very little delay or up-front costs. Find out how we can help you by handling the manufacturing process.
There are NovaLink facilities in the border cities of Brownsville, Texas, Matamoros, Mexico, and Saltillo, Mexico.
Explore More: Discover Related Blog Posts
Expand your knowledge and delve deeper into manufacturing in Mexico vs. China with our curated collection of related blog posts.
- The Workforce in Mexico vs. China: Which is More Skilled and Cost-effective?
- Environmental Sustainability: Why Manufacturing in Mexico is More Responsible Than in China [2024]
- The Importance of Intellectual Property Protection in Mexico versus China [2024]
- The Pros and Cons of Outsourcing Manufacturing to Mexico vs. China [2025]
- Mexico’s Proximity Gives It the Edge Over China
- 5 Reasons Why Mexico is a Better Choice for Manufacturing Than China
- Benefits of Manufacturing in Mexico vs. China: Which Country Offers More Value for Your Business?
- The Impact of Trade Agreements on Manufacturing in Mexico and China
- Closeness Counts: Why Sourcing For Manufacturing in Mexico Trumps China for Business Success [2024]