Last Updated on January 9, 2025
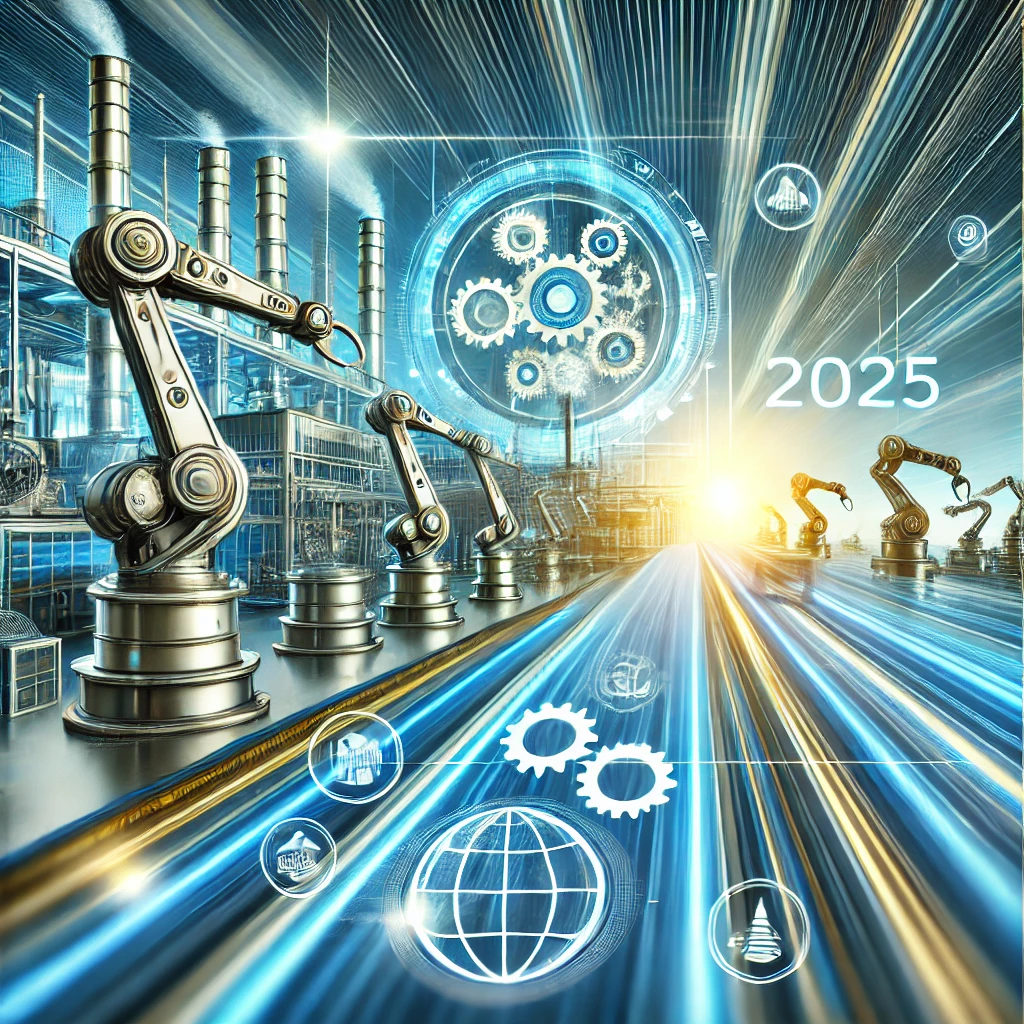
The manufacturing industry is not slowing down. If anything, it’s getting more unpredictable. Supply chain hiccups, economic twists, and global uncertainties aren’t temporary; they’re the new normal. Waiting for stability isn’t just wishful thinking—it’s a recipe for falling behind. To thrive in 2025, companies need manufacturing operations strategies built for uncertainty. This includes embracing agility, planning for the unexpected, and, yes, looking to nearshoring in Mexico to reduce risks while improving efficiency. Here’s how to turn challenges into opportunities with five key strategies.
1. Shorten Your Supply Chain (Because Distance Equals Risk)
When every link in your supply chain is stretched thin, delays and disruptions are inevitable. Long supply routes are more vulnerable to unforeseen problems like port closures, geopolitical tensions, or skyrocketing shipping costs.
What nearshoring to Mexico offers:
- Proximity: Being close to the U.S. reduces transit times and shipping costs.
- Stability: Mexico’s strong trade agreements, such as USMCA, create a reliable framework for cross-border business.
- Adaptability: Faster turnaround times make it easier to respond to shifting customer demands.
For example, a company sourcing parts from Asia might face weeks of delays during a port strike. By moving operations closer, manufacturers can avoid bottlenecks.
2. Plan for Flexibility—Not Perfection
Perfect plans rarely survive the first challenge. Flexibility must be baked into your operations. This means being ready to pivot when the unexpected happens.
Key steps to building flexibility:
- Diversify suppliers: Work with multiple vendors across different regions to ensure steady supply.
- Invest in technology: Tools like real-time tracking and predictive analytics give you insight to adapt quickly.
Mexico’s well-established manufacturing ecosystem allows businesses to source from a wide range of suppliers. It’s a built-in advantage for companies aiming to maintain flexibility without sacrificing quality or cost.
3. Strengthen Your Workforce (Because Machines Aren’t Everything)
While automation is crucial, human ingenuity still plays a huge role in overcoming challenges. Investing in a capable, well-trained workforce can give your operations a competitive edge.
Mexico’s workforce advantage:
- Skilled talent: Mexico offers a growing pool of workers trained in electronics, automotive, and aerospace manufacturing.
- Affordable labor: Competitive wages make workforce investments sustainable.
- Collaboration opportunities: Many companies work directly with technical schools and universities to tailor training programs.
A motivated and skilled workforce isn’t just a line item in your budget—it’s an insurance policy against operational hiccups.
4. Embrace Modular Manufacturing (Because One-Size-Fits-All Doesn’t Work)
Manufacturing isn’t a one-size-fits-all operation anymore. You need facilities and processes that can quickly adapt to changes in demand, product design, or market conditions.
Why modular setups matter:
- Scalability: Easily increase or decrease production without massive overhauls.
- Product variety: Adapt lines to produce different goods as needed.
Mexico has become a hub for modern, modular manufacturing facilities, especially in industrial hubs like Matamoros, Monterrey, Guadalajara, and Querétaro. These setups offer the flexibility to keep pace with market demands while minimizing downtime.
5. Prioritize Resilience Planning (Because It’s Not “If” but “When”)
Disruptions will happen—it’s only a matter of time. The key is being prepared to weather them with minimal impact.
How to plan for resilience:
- Build inventory buffers: Maintain enough stock to keep operations running through short-term supply interruptions.
- Scenario testing: Identify potential risks and practice how your business would respond.
- Collaborate with suppliers: Share risk management strategies to ensure alignment.
By nearshoring to Mexico, manufacturers benefit from reduced transportation risks and faster response times to unexpected events. This makes it easier to build resilience into their operations.
Conclusion: Don’t Wait for Normal—Adapt to What’s Next
The truth is, there’s no “normal” coming back. Manufacturing in 2025 will demand agility, foresight, and resilience. Companies that embrace uncertainty and adjust their strategies will lead the way.
Nearshoring to Mexico isn’t just a cost-cutting measure—it’s a foundational strategy for reducing risks, staying flexible, and achieving operational excellence in an unpredictable world. Start implementing these manufacturing operations strategies, and you’ll be ready for whatever comes next.perations strategies, and you’ll be ready for whatever comes next.
Why Mexico Is the Hub of Nearshoring Growth
Mexico stands at the heart of North America's nearshoring boom. Its manufacturing capacity, skilled workforce, and competitive costs make it the preferred destination for foreign direct investment (FDI).
Advantages of Mexico for Nearshoring
- Strategic Location: Sharing a border with the U.S., Mexico offers unparalleled proximity to North American markets.
- Cost-Competitive Labor: Mexican labor rates are highly competitive with China and Southeast Asia.
- Advanced Manufacturing: Mexico boasts thriving industries in automotive, aerospace, textiles, and electronics.
- Favorable Trade Agreements: Beyond USMCA, Mexico is part of numerous bilateral agreements enhancing market access.
Industrial Parks and clusters
Industrial clusters across Mexico cater to specialized sectors. These parks provide:
- Access to skilled labor.
- Integrated supply chain ecosystems.
- Proximity to key logistics hubs.
Potential Challenges
While nearshoring offers numerous advantages, businesses must navigate challenges such as:
- Infrastructure Bottlenecks: Upgrading roads, ports, and rail networks remains critical.
- Regulatory Compliance: Understanding and adhering to Mexican labor and environmental laws.
- Cultural and Operational Alignment: Bridging cultural differences to ensure smooth collaboration.
Strategic Solutions
- Infrastructure Investment: Government and private sector initiatives drive modernization projects.
- Strong Partnerships: Partnering with experienced nearshore service providers mitigates risks.
- Comprehensive Due Diligence: Leveraging market research and local expertise to ensure compliance.
FAQs on Manufacturing Operations Strategies
1. Why is nearshoring to Mexico a strong strategy for 2025?
Nearshoring offers reduced transit times, lower shipping costs, and less exposure to global disruptions, all while leveraging Mexico’s skilled workforce and strong trade agreements.
2. How does modular manufacturing help in uncertain times?
Modular setups allow companies to quickly scale production up or down and switch between products, enabling them to adapt to market changes or disruptions without major retooling.
3. What industries benefit most from nearshoring in Mexico?
Industries like automotive, aerospace, electronics, and medical devices often see the greatest benefits due to Mexico’s specialized infrastructure and skilled labor.
4. How can companies ensure successful nearshoring operations?
Research potential regions, establish local partnerships, and invest in training your workforce to align with operational goals. Experienced local advisors can simplify the process.
5. Is nearshoring more expensive than offshoring?
While initial costs might be higher than offshoring, nearshoring reduces long-term expenses by lowering shipping costs, improving time-to-market, and minimizing disruption risks.
Explore More: Discover Related Blog Posts
Expand your knowledge and delve deeper into more information about Reduce Manufacturing Costs with our curated collection of related blog posts.
- How Mexico Is Strengthening Supply Chains for Long-Term Stability
- 3 Hidden Costs You’re Avoiding by Manufacturing in Mexico (And Why It Matters)
- Mexico’s Customs Clearance: Why It’s Faster—and Smarter—for Manufacturers
- Setup Process for Manufacturing in Mexico: What You Should Know About Timelines, Permits, and Common Pitfalls
- The Most Overlooked Advantage of Mexico’s Logistics Infrastructure
About NovaLink
As a manufacturer in Mexico, NovaLink employs a unique approach that transcends the traditional model of shelter production. More than just the location of your manufacturing, we would like to become a partner in your manufacturing in Mexico. You will be able to relocate or initiate manufacturing for your company in Mexico in a low-cost labor environment with very little delay or up-front costs. Find out how we can help you by handling the manufacturing process.
There are NovaLink facilities in the border cities of Brownsville, Texas, Matamoros, Mexico, and Saltillo, Mexico.