Last Updated on October 24, 2024
Introduction
Cost efficiency in manufacturing is essential for industrial and economic development. When determining where and how to manufacture, businesses face trade-offs that affect cost efficiency, quality control, and time to market. This guide will explore key strategies that help companies optimize their cost structure while maintaining operational efficiency and high-quality standards.
Balancing Labor Costs and a Skilled Workforce
The Importance of Low-Cost Labor Regions
Relocating operations to countries with lower labor costs, such as Mexico or other nearshore locations, is often considered the primary means of reducing manufacturing expenses. However, it's crucial to find the right balance between cost savings and skilled workforce availability. Opting for regions with cost-effective labor and specialized manufacturing expertise can maximize operational effectiveness.
Leveraging Local Expertise
Mexico offers a favorable balance between lower labor costs and access to a highly skilled workforce in various sectors, such as automotive, electronics, and textiles. By leveraging local expertise and industry-specific skills, companies can mitigate risks associated with poor quality and high turnover rates, which can undermine overall savings achieved through low wages.
Supply Chain Optimization for Cost Reduction
Nearshoring for Faster Turnaround and Lower Logistics Costs
Incorporating nearshoring strategies, such as setting up manufacturing operations in Mexico, enables businesses to reduce logistics costs and lead times compared to offshore locations in Asia. Mexico’s proximity to the U.S. provides faster shipping times and more responsive supply chains. This is critical for businesses that require just-in-time delivery models or aim to quickly react to changing market demands.
Reducing Dependence on Global Supply Chains
By minimizing dependency on long, complicated supply chains that span multiple continents, manufacturers can limit risks related to geopolitical tensions, trade tariffs, and supply chain disruptions. These risks have become more common in recent years. A more localized supply chain also reduces the environmental footprint, as transportation emissions are significantly lower.
Diversifying the supplier base in the supply chain is an important management strategy to reduce dependence on specific regions. By expanding the supplier network, companies can reduce risks, increase flexibility, optimise costs and drive innovation. Diversifying the supplier base requires careful evaluation, geographic analysis, supplier development, risk management and continuous monitoring. Implementing this strategy can help organisations build a more resilient supply chain that can withstand unexpected disruptions and ensure long-term success in today’s dynamic business environment. - Thomas Sandler
Technology Investment in Lean Manufacturing
Automation to Enhance Efficiency
The integration of automation technologies is a key factor in improving manufacturing productivity. By implementing Industry 4.0 technologies such as robotics, IoT (Internet of Things), and advanced analytics, manufacturers can streamline their processes, reduce labor costs, and maintain high quality control levels. Automated systems also ensure consistent production speeds, minimizing downtime and enabling businesses to meet tight deadlines.
Balancing Initial Costs with Long-Term Savings
While the upfront investment in automation and smart manufacturing technologies may seem high, the long-term savings generated through increased efficiency, reduced waste, and minimized error rates provide a substantial return on investment (ROI). Strategic investment in automation can give companies a competitive edge by reducing per-unit production costs and improving overall profitability.
Managing Trade-Offs in Material Costs and Quality
Selecting the Right Materials for Cost and Performance
Choosing the right raw materials is crucial for maintaining a balance between product quality and cost. Opting for lower-cost materials can reduce manufacturing expenses, but they may impact product durability, customer satisfaction, and long-term brand value. On the other hand, premium materials may elevate the cost but deliver a superior product that commands higher market prices.
Building Strong Supplier Relationships
Developing long-term partnerships with reliable suppliers ensures material quality consistency and enables manufacturers to negotiate better pricing and favorable payment terms. By establishing a stable network of suppliers, businesses can mitigate risks related to price fluctuations and supply shortages, ensuring consistent production flows.
Reducing Overhead Costs through Lean Operations
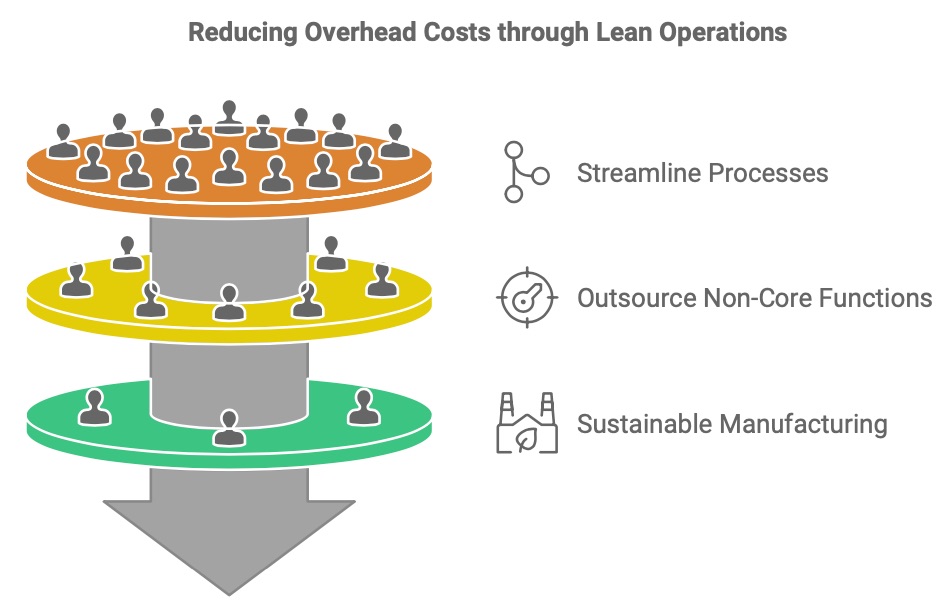
Streamlining Processes
Reducing unnecessary steps in manufacturing can drastically lower overhead costs. Lean manufacturing techniques such as value stream mapping (VSM) help identify areas where processes can be optimized, enabling businesses to eliminate inefficiencies. For example, adopting a just-in-time production model can reduce inventory holding costs and free up capital.
Outsourcing Non-Core Functions
Outsourcing non-essential functions such as warehousing, packaging, and logistics to specialized service providers can help manufacturers focus on their core competencies. By outsourcing these activities, companies can reduce their in-house operational burden and benefit from third-party providers' expertise, resulting in overall cost reductions.
Optimizing Energy Usage
Sustainable Manufacturing for Long-Term Savings
Energy consumption is a significant operational cost for manufacturers, but adopting sustainable practices can mitigate this. Investing in energy-efficient machinery, renewable energy sources, and waste reduction programs can lower utility expenses and create long-term savings. Implementing green manufacturing techniques can also enhance brand reputation and align with corporate social responsibility (CSR) goals.
Conclusion
Achieving cost efficiency in manufacturing requires a holistic approach that considers labor, supply chain management, technology investment, material sourcing, and energy use. By carefully managing these trade-offs, companies can maintain competitiveness, improve profitability, and ensure consistent product quality.
Maximizing cost efficiency involves not just focusing on one aspect but integrating various strategies that reinforce each other. Nearshoring, automation, lean manufacturing, and smart material selection are all key components of a robust, cost-effective manufacturing strategy that meets today’s complex market demands.
FAQ's on Cost Efficiency in Manufacturing
1. What is cost efficiency in manufacturing?
Cost efficiency in manufacturing refers to optimizing production processes to minimize costs while maintaining or improving the quality of products. It involves balancing factors such as labor costs, material selection, supply chain management, and technology investments to achieve the best possible financial outcomes.
2. How can nearshoring help reduce manufacturing costs?
Nearshoring reduces manufacturing costs by locating production closer to key markets, which decreases logistics expenses, shortens delivery times, and enhances supply chain responsiveness. For example, nearshoring to Mexico can significantly cut shipping costs for U.S. companies compared to manufacturing in Asia.
3. What role does automation play in cost-efficient manufacturing?
Automation enhances cost efficiency by streamlining production processes, reducing labor costs, minimizing errors, and improving production speed. Technologies like robotics and IoT systems allow for more consistent output and faster turnaround, ultimately lowering per-unit production costs.
4. How can manufacturers manage material costs without compromising quality?
Manufacturers can manage material costs by selecting the most suitable materials that balance performance and price, establishing strong supplier relationships to negotiate better rates, and optimizing inventory management. Additionally, evaluating material options based on long-term durability and customer satisfaction can lead to more cost-effective decisions.
5. What are some strategies to reduce overhead costs in manufacturing?
Overhead costs can be reduced by adopting lean manufacturing principles, outsourcing non-core functions like packaging and logistics, and streamlining production processes to eliminate inefficiencies. Implementing energy-efficient machinery and sustainable practices can also help cut utility expenses over time.
Explore More: Discover Related Blog Posts
Expand your knowledge and delve deeper into more information about Reduce Manufacturing Costs with our curated collection of related blog posts.
- How Mexico Is Strengthening Supply Chains for Long-Term Stability
- 3 Hidden Costs You’re Avoiding by Manufacturing in Mexico (And Why It Matters)
- Mexico’s Customs Clearance: Why It’s Faster—and Smarter—for Manufacturers
- Setup Process for Manufacturing in Mexico: What You Should Know About Timelines, Permits, and Common Pitfalls
- The Most Overlooked Advantage of Mexico’s Logistics Infrastructure
About NovaLink
As a manufacturer in Mexico, NovaLink employs a unique approach that transcends the traditional model of shelter production. More than just the location of your manufacturing, we would like to become a partner in your manufacturing in Mexico. You will be able to relocate or initiate manufacturing for your company in Mexico in a low-cost labor environment with very little delay or up-front costs. Find out how we can help you by handling the manufacturing process.
There are NovaLink facilities in the border cities of Brownsville, Texas, Matamoros, Mexico, and Saltillo, Mexico.