Last Updated on March 19, 2025
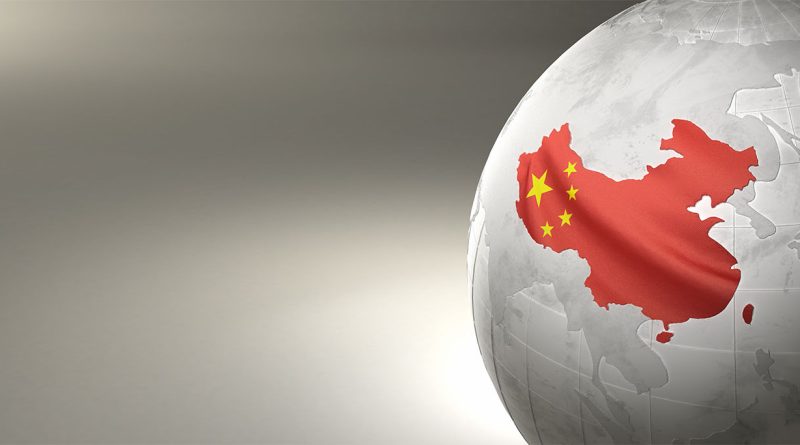
The global manufacturing landscape is shifting seismically. Companies are reconsidering their manufacturing footprint in China, driven by complex geopolitical tensions and evolving economic strategies. With President Trump's aggressive trade policies proposing a staggering 60% tariff on Chinese imports, manufacturing companies leaving China are seeking strategic alternatives to protect their business interests.
Meticulous Planning and Strategic Execution Are Key for Leaving China
Businesses today face unprecedented challenges in global supply chain management. Manufacturing companies leaving China will need to navigate the intricate process of relocating manufacturing operations. But how? The answer lies in meticulous planning and strategic execution.
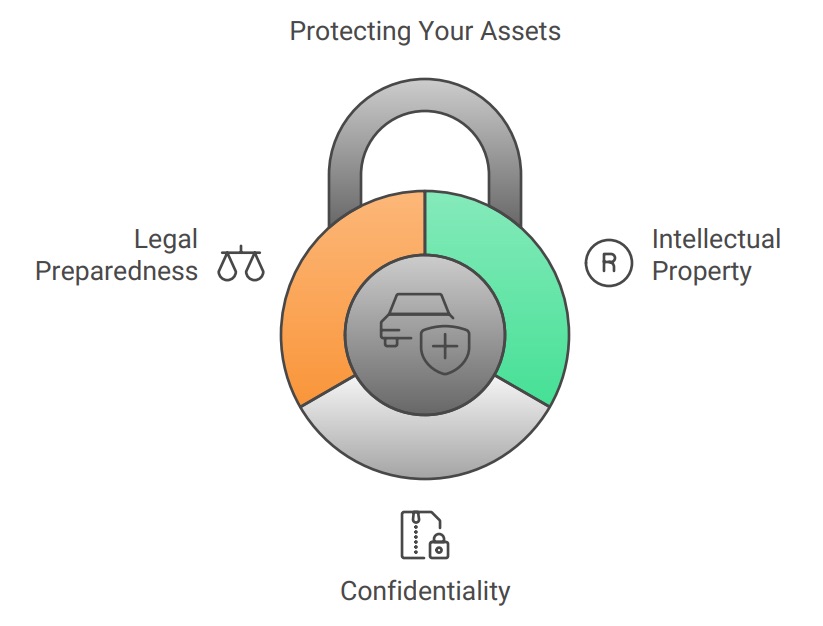
Protecting Your Assets: A Critical First Step
When exiting China, securing your assets is paramount. Manufacturers must:
- Retrieve tooling and molds before announcing relocation plans
- Establish clear ownership agreements for pre-paid products
- Protect intellectual property through comprehensive registration
Think of this step as locking your house doors before leaving. It protects what’s rightfully yours, even as you move operations elsewhere.
Intellectual Property: Your Hidden Vulnerability
Protecting your intellectual assets is more than a precaution—it's a survival strategy. Companies must proactively register trademarks, patents, and copyrights in China. This safeguards against potential retaliatory trademark filings and reduces legal vulnerabilities.
The Art of Carefulness in Relocation: Maintaining Confidentiality
Maintaining confidentiality during your manufacturing transition is crucial. Premature announcements can trigger:
- Supplier retaliation
- Employee uncertainty
- Local authorities complications
By keeping plans confidential until all preparations are complete, you reduce risks and maintain control over the process.
Managing sensitive data has become an integral part of every business, regardless of industry. While the manufacturing sector does not collect consumer data on a large scale, it generates and acquires other types of highly sensitive data such as source code, patents, designs, and proprietary information.
Manufacturers are often also part of the supply chain of larger organizations and need to sign non-disclosure agreements (NDAs) that guarantee data confidentiality and, for certain industries, even submit to information security assessments. - Endpoint Protector
Legal Preparedness: Anticipating and Mitigating Disputes
Manufacturing companies leaving China may face legal challenges, such as claims from suppliers, landlords, or employees. Be prepared to address these disputes with thorough documentation and legal support. Manufacturers should:
- Anticipate potential claims from suppliers
- Prepare comprehensive documentation
- Consider preemptive legal actions in neutral jurisdictions
It’s best to consult with an attorney familiar with Chinese employment law — perhaps one with offices in the U.S. as well as China. In-country local Chinese law firms may not have your best interest in mind. It’s best to use a multinational law firm with deep China experience. - Area Development
Supply Chain Resilience: Building New Partnerships
Developing alternative supply chains is not just a contingency—it's a competitive advantage. The COVID-19 pandemic highlighted the vulnerability of global supply chains, especially for those overly dependent on a single source or location. This revelation led many U.S. companies to reassess their supply chain strategies, recognizing the necessity of diversification and resilience.
Although it may be difficult to do initially, establish relationships with existing suppliers before exiting China to ensure:
- Smooth operational transition
- Minimal production disruptions
- Continued business continuity
By spreading operations across multiple countries, businesses can mitigate the risks associated with unexpected disruptions. This approach not only prepares companies for unforeseen events but also strengthens their overall market position. Diversifying supply chains is a strategic move that addresses past vulnerabilities while securing future growth.
Exploring Strategic Approaches to Manufacturing and Procurement
In today's dynamic global market, companies are re-evaluating their strategies for manufacturing and procurement to optimize cost and efficiency. This involves exploring various approaches like offshoring, nearshoring, reshoring, and 'rightshoring.' Each strategy offers unique benefits and challenges, significantly impacting a company's bottom line.
Offshoring
Offshoring continues to be a popular choice for reducing labor costs by moving production to countries with lower wages. However, it often involves longer lead times and complex supply chain logistics.
Nearshoring
For those seeking closer proximity to their home markets, nearshoring presents an attractive option. By relocating to neighboring countries, companies can enjoy reduced shipping times and simplified communication.
Reshoring
Some businesses are bringing operations back home through reshoring, driven by the desire to control quality, enhance sustainability, and respond to consumer demand for locally-made products.
Rightshoring
Rightshoring combines the best aspects of the above strategies, tailoring production locations to suit specific business needs and market demands.
Alternative Manufacturing Destinations: Mexico Emerges
For companies leaving China, Mexico offers a compelling alternative. Here's why Mexico stands out:
- Proximity to the U.S.: Shorter transit times reduce shipping costs and improve lead times.
- Skilled Workforce: Mexico has a skilled workforce in automotive, textiles, and electronics industries.
- Trade Benefits: The USMCA eliminates many tariffs, fostering a stable and favorable trade environment.
- Cultural Compatibility: Fewer cultural and linguistic barriers make business operations smoother than other regions.
By relocating to Mexico, manufacturers can enjoy cost savings, operational efficiency, and better access to North American markets.
Why U.S. Companies Are Moving Their Supply Chains From China to Mexico
Does Mexico have supply chain issues? In spite of the fact that all exporting companies face supply chain challenges, Mexico seems to face fewer challenges than other manufacturing countries, such as China. Supply Chain Brain has a list of reasons why companies are moving their supply chains from China to Mexico.
Ground Transport
Goods can be imported from Mexico via ground transport in a matter of days or even hours. This is never an option for goods manufactured in China, from which everything must come by ocean or air. The former is very time consuming (it can often take weeks), and the latter is very expensive.
"Trusted Partner" Status for Customs
The U.S. offers two programs that help facilitate faster and easier Customs processing for U.S.-Mexico trade: FAST and C-TPAT. Initiated after 9/11, FAST is a trusted traveler/trusted shipper program that allows expedited processing for commercial carriers who have completed background checks and fulfill certain eligibility requirements (much like TSA Precheck for air travelers). FAST certification is for drivers; C-TPAT is a broader program that shippers must apply for. Once a company is certified for C-TPAT, its drivers can then apply for FAST. There are no such programs for U.S.-China trade.
A Transparent Landscape
There are also new modern options for transport that make Mexico attractive. Companies can coordinate door-to-door transportation between the U.S. and Mexico, including procurement of trucks on both sides of the border, customs clearance, insurance, financing, and reporting. This allows manufacturers to focus on their core competency, rather than logistics, and can also reduce the need for big in-house shipping and logistics teams.
Small Language Barrier
Spanish is the second-most common language spoken in the U.S., making it relatively easy to communicate with partners in Mexico (and find bilingual staff and vendors).
Spanish is the second-most common language spoken in the U.S., making it relatively easy to communicate with partners in Mexico (and find bilingual staff and vendors).
Conclusion
The manufacturing exodus from China is more than a trend—it's a strategic realignment of global business operations. Success depends on careful planning, asset protection, and adaptable supply chain management.
Frequently Asked Questions
What are the primary risks of leaving manufacturing in China? Risks include potential intellectual property theft, supply chain disruptions, and legal complications from abrupt departures.
What are the Challenges and Limitations of Shifting Manufacturing to Vietnam? As companies explore alternatives to China for manufacturing, several challenges and limitations come to the forefront, particularly with countries like Vietnam.
1. Scale of Manufacturing Capacity
Vietnam's population is only a fraction of China’s. This significantly limits its ability to match China's extensive manufacturing output. With a manufacturing sector that represents just a sliver of China's capacity, Vietnam cannot accommodate the demands if numerous companies try to relocate their production simultaneously.
2. Infrastructure Development
Despite its robust growth, Vietnam's infrastructure is still developing. Large-scale production requires well-established transportation networks, power supplies, and logistics solutions which take time to mature to the level seen in China.
3. Skilled Workforce Availability
The availability of a skilled labor force is another challenge. While Vietnam has a young and dynamic workforce, scaling this to meet the complex demands of high-level manufacturing requires time and investment in education and training.
4. Economic Diversification
Many advanced economies seek to mitigate risks by diversifying their supply chains. However, the process of significantly reducing dependence on China will take years. Building a diverse manufacturing ecosystem capable of supporting this shift involves substantial financial and strategic commitments.
5. Policy and Regulatory Challenges
Navigating the policy landscape in a new country can be daunting. Companies must consider local regulations, trade policies, and potential barriers that can complicate operations when shifting manufacturing bases.
In summary, while Vietnam presents potential as a manufacturing hub, the transition from a China-centric model is laden with hurdles that require strategic foresight and considerable time to overcome.
What Impact have Rising Labor and Production Costs in China on U.S. Companies? In recent years, U.S. companies have faced significant challenges due to increasing labor and production costs in China. Initially drawn to China for its affordability, these businesses are now seeing those cost advantages diminish.
As China's workforce demands better pay and improved working conditions, labor expenses have surged. This shift, while favorable for Chinese workers' wellbeing, forces U.S. companies to reconsider their cost-benefit analysis. Increased wage expectations mean that manufacturing in China is no longer the bargain it once was.
Moreover, the escalating prices of energy, raw materials, and meeting more stringent regulatory standards have compounded these issues. U.S. companies, as a result, experience tighter profit margins and may need to re-evaluate their global supply chain strategies. Consequently, some are exploring alternative manufacturing locations or even reshoring operations to maintain financial viability.
In summary, rising costs in China are prompting U.S. firms to adapt by seeking new solutions to preserve competitiveness in the global market.
How long does a typical manufacturing relocation process take? Depending on complexity, relocations can take 12-24 months for comprehensive planning and execution.
Are there tax implications for moving manufacturing out of China? Yes, companies must carefully navigate international tax laws and potential tariff structures in new manufacturing locations.
What countries are most attractive for manufacturing relocation? Mexico, Vietnam, India, and some Eastern European countries are emerging as attractive alternatives.
What Potential Does India have to Rival China as a Manufacturing Superpower?
India holds significant promise as a formidable player on the global manufacturing stage. This potential is rooted in several key factors that position the country favorably:
- Expanding Manufacturing Base: India is rapidly increasing its manufacturing capacity, particularly in high-tech industries. Companies are increasingly partnering with local manufacturers to produce a wide range of products, including electronics and automotive parts. This trend is bolstered by strategic government initiatives aimed at boosting the industrial sector.
- Skilled Labor Force: The availability of a large pool of skilled and semi-skilled labor makes India an attractive destination for manufacturing. With investments in education and training, the workforce is increasingly capable of handling complex manufacturing processes, which is essential for competing on a global scale.
- Growing Domestic Market: India's burgeoning consumer market provides a powerful incentive for companies to set up manufacturing operations in the country. As consumer demand grows, so does the need for locally produced goods, enhancing the appeal of India as a manufacturing hub.
- Innovation and Development: Significant investments in research and development are placing India at the forefront of innovation. This focus not only supports domestic industries but also attracts global partners seeking cutting-edge solutions and technologies.
- Strategic Government Policies: Pro-business policies and initiatives, such as the "Make in India" campaign, aim to simplify regulations and provide incentives for foreign companies to establish manufacturing bases. These efforts enhance India's competitiveness on the global stage.
In summary, India's potential to rival China stems from its expanding manufacturing infrastructure, large and capable workforce, strong domestic market, commitment to innovation, and supportive government policies. These elements combined suggest a promising future for India's role as a global manufacturing powerhouse.
How is Eastern Europe Emerging as a Manufacturing Hub for US Companies?
Eastern Europe is quickly becoming a focal point for U.S. Companies looking to expand their manufacturing operations. One of the key drivers for this trend is the region's strategic location. Being closer to Western markets offers companies in Eastern Europe a valuable logistical advantage over Asian locations. This proximity reduces shipping times and costs, making it an appealing option for timely market access.
Additionally, the aerospace industry in countries like Poland is thriving. Aerospace firms have taken notice, setting up manufacturing facilities to tap into the burgeoning local talent pool and expertise, which are often more cost-effective than in Western counterparts.
Moreover, countries such as Hungary have become hotspots for electronics and appliance manufacturing, drawing in major international companies. This expansion is due in part to the competitive labor market and favorable business environments that Eastern Europe offers.
Finally, recent geopolitical developments have influenced corporate strategies, leading several companies to reconsider their presence in Russia. As businesses withdraw and seek alternative locations, Eastern Europe stands out as an attractive alternative for setting up manufacturing operations, further solidifying its role as an emerging hub for U.S. Companies.
How can companies minimize financial risks during relocation? Thorough due diligence, phased transitions, and maintaining multiple supply chain options can help mitigate financial risks.
Explore More: Discover Related Blog Posts
Expand your knowledge and delve deeper into manufacturing in Mexico vs. China with our curated collection of related blog posts.
- The Workforce in Mexico vs. China: Which is More Skilled and Cost-effective?
- Environmental Sustainability: Why Manufacturing in Mexico is More Responsible Than in China [2024]
- The Importance of Intellectual Property Protection in Mexico versus China [2024]
- The Pros and Cons of Outsourcing Manufacturing to Mexico vs. China [2025]
- Mexico’s Proximity Gives It the Edge Over China
- 5 Reasons Why Mexico is a Better Choice for Manufacturing Than China
- Benefits of Manufacturing in Mexico vs. China: Which Country Offers More Value for Your Business?
- The Impact of Trade Agreements on Manufacturing in Mexico and China
- Closeness Counts: Why Sourcing For Manufacturing in Mexico Trumps China for Business Success [2024]
About NovaLink
As a manufacturer in Mexico, NovaLink employs a unique approach that transcends the traditional model of shelter production. More than just the location of your manufacturing, we would like to become a partner in your manufacturing in Mexico. You will be able to relocate or initiate manufacturing for your company in Mexico in a low-cost labor environment with very little delay or up-front costs. Find out how we can help you by handling the manufacturing process.
There are NovaLink facilities in the border cities of Brownsville, Texas, Matamoros, Mexico, and Saltillo, Mexico.